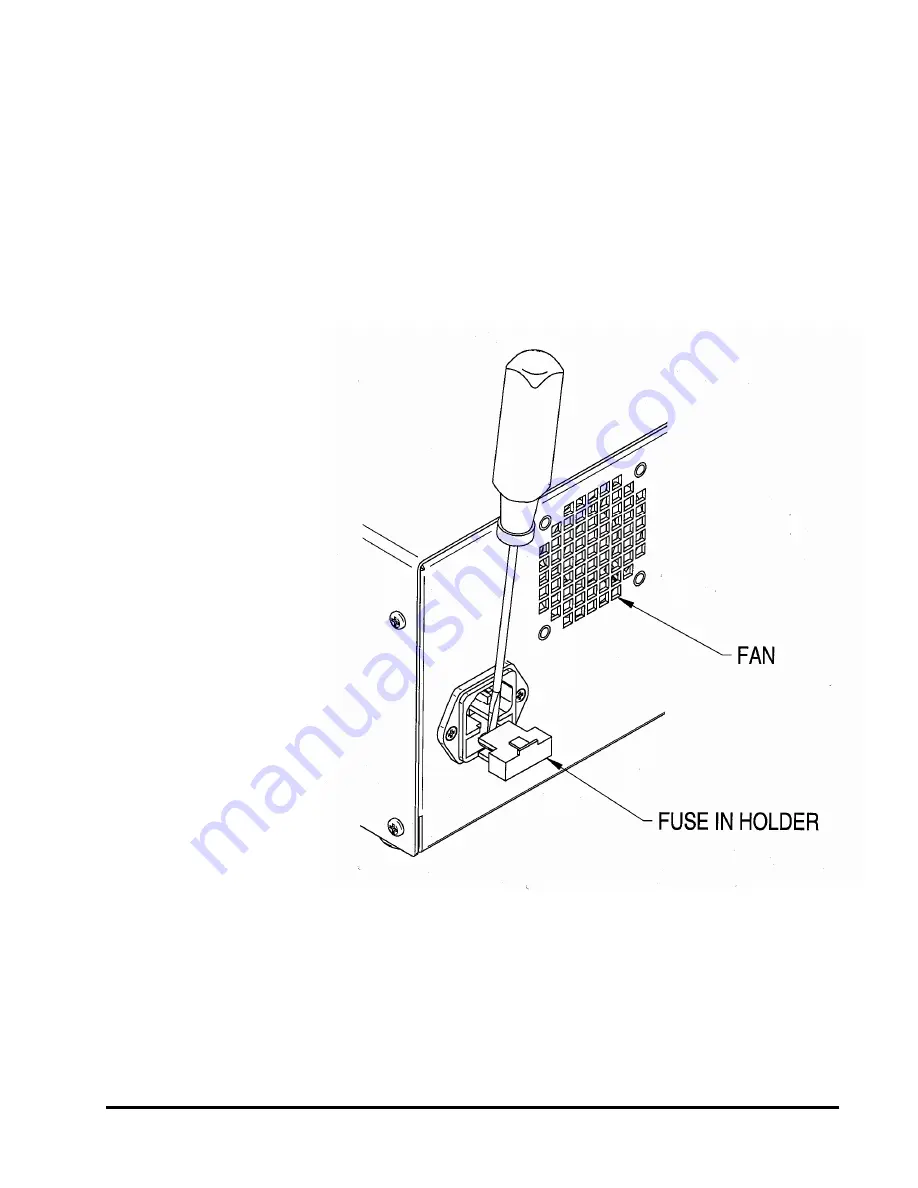
7-15
5.9 Fuse
Replacement
Three fuses protect the Binary Solvent Delivery Module. Two of
the fuses are located in the power entry module at the rear of the
cabinet and are in series with the AC input line. The other fuse is
located on the circuit board and is in series with the 24 VDC supply.
Troubleshooting the fuses is straightforward. If the power cord is
plugged in and the on/off power entry switch is on and the display
does not light, check the two fuses in the power entry module. To gain
access to these fuses, gently pry off the cover plate with a small flat-
bladed screwdriver. Replace with fuses of the correct rating: 2 A slow-
blo for 120 VAC systems.
Summary of Contents for BINARY SOLVENT DELIVERY MODULE
Page 2: ......