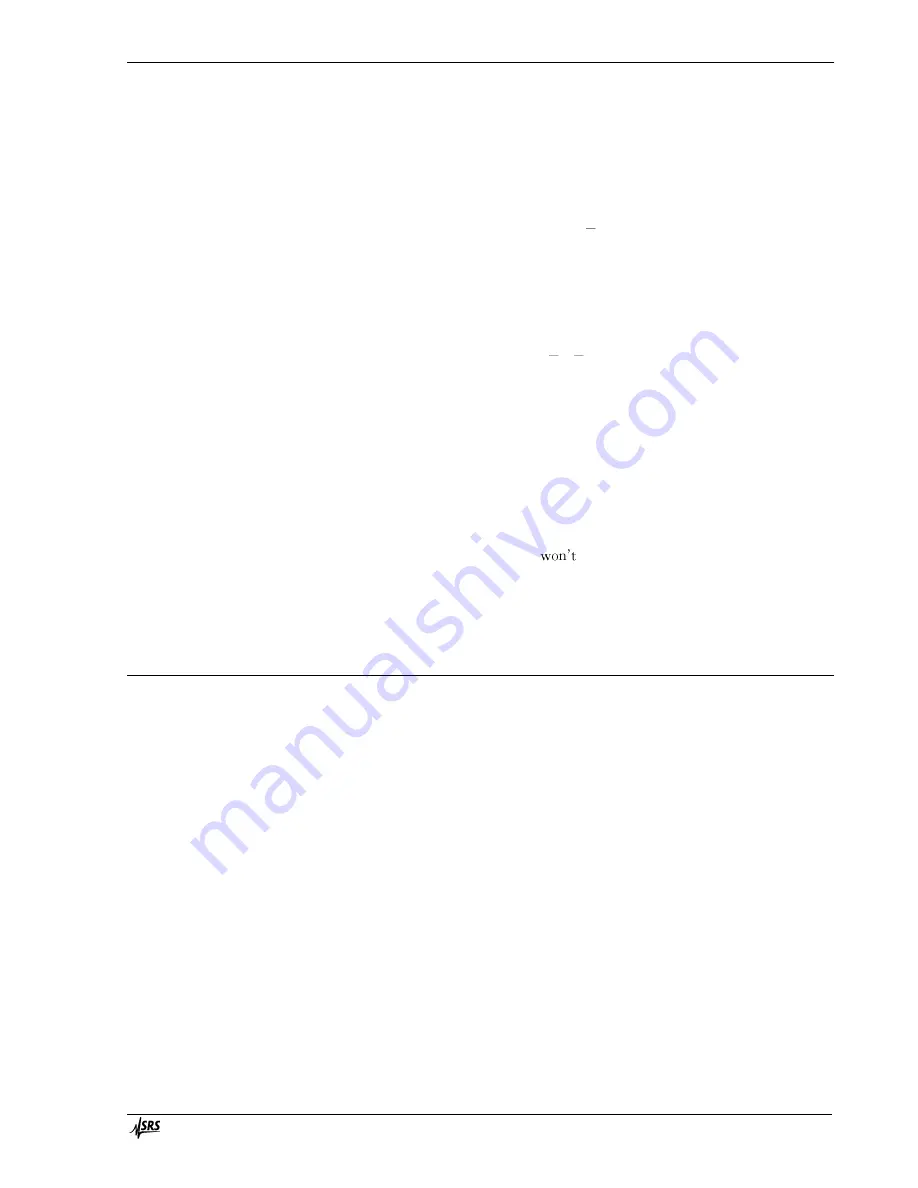
Operation
31
CTC100 Programmable Temperature Controller
As the actual temperature approaches the setpoint, the proportional output Y
p
decreases to zero, at
which point no power is supplied to the heater.
Normally, however, some power is required to keep the heater at the setpoint, which is why the
integral feedback algorithm is needed. It multiplies the error by a constant (I) and adds the result
to the previous integral output:
Y
i
(t) = I · E(t) + Y
i
(t 1)
As the temperature approaches the setpoint, the rate of change of the integral output Y
i
drops to
zero.
Derivative feedback tries to predict what the temperature will be in the future by multiplying
the rate of temperature change by a constant, D:
Y
d
(t) = D * (T(t 1) T(t))
If the temperature is increasing (and D is positive), derivative feedback reduces power to the
heater; if the temperature is decreasing, derivative feedback increases power to the heater.
The output of the PID feedback loop (i.e., the heater power) is the sum of the three feedback
algorithms:
Heater power = Y
p
(t) + Y
i
(t) + Y
d
(t)
The key challenge to using a PID feedback loop is determining the best feedback gains. The
constants P, I, and D are different for every apparatus and must be determined experimentally. As a
general rule, if the gains are too low, the feedback
respond enough to temperature
variations; if they are too high, the feedback responds too much and overshoots the setpoint, and
both heater power and temperature may begin to oscillate. The faster the temperature changes in
response to the heater, the larger the gains can be.
M anual tuning
In this section we will use step response curves to illustrate some basic aspects of how the three
feedback parameters P, I, and D affect feedback performance.
Proportional: the figure below illustrates the effect of changing the proportional gain P. The
top graph shows the power being delivered to a heater by a PID feedback loop during four separate
tests, while the bottom graph shows the temperature of the heater during the same tests. Each test
is identical except for the value of P. At 1 minute, the setpoint is increased from 60 to 70°C. When
P = 1 W/°C (second curve from top), the feedback loop exhibits a perfect response; that is, the
temperature rapidly increases to 70°C with a slight overshoot that serves to minimize the settling
time. If P is increased to 2 W/°C, the temperature responds more quickly but then overshoots the
setpoint by an excessive amount, causing the system to oscillate.
Summary of Contents for CTC100
Page 1: ...Version 2 1 May 14 2019 User Manual CTC100 Cryogenic Temperature Controller...
Page 6: ......
Page 8: ......
Page 12: ......
Page 25: ...Operation 13 CTC100 Programmable Temperature Controller...
Page 85: ...Operation 73 CTC100 Programmable Temperature Controller To disable cascade cont select it...
Page 128: ......
Page 129: ...Remote Programming 117 CTC100 Programmable Temperature Controller...
Page 130: ......
Page 142: ......
Page 150: ......
Page 176: ......