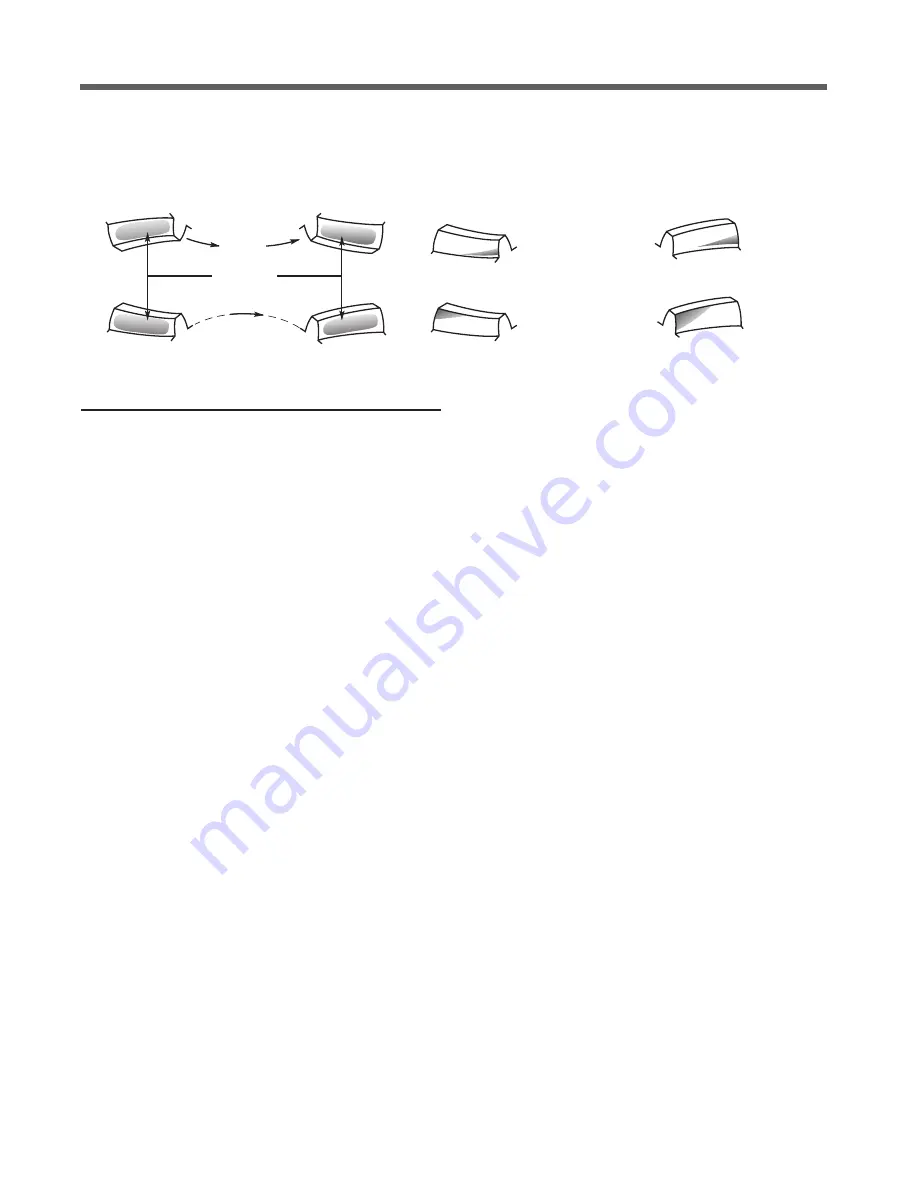
19
DIRECTION OF ROTATION
RING GEAR
ORIGINAL
PATTERN
AFTER
BREAK IN
*
*
*
*
CONVEX SIDE
ENTERING
CONCAVE SIDE
LEAVING
CONCAVE SIDE
CONVEX SIDE
OUT OF POSITION CONTACT
CAUSE: PINION TOO CLOSE TO
GEAR CENTER.
REMEDY: MOVE PINION OUT.
OUT OF POSITION CONTACT
CAUSE: PINION TOO FAR FROM
GEAR CENTER.
REMEDY: MOVE PINION IN.
CORRECT PINION AND RING GEAR TOOTH CONTACT PATTERNS
INCORRECT RING GEAR TOOTH CONTACT PATTERNS
Figure 17
Spiral Bevel Gear Tooth Pattern
field repair
The tooth contact pattern should again be checked to determine
if adjusting the backlash has produced any shift. If it has shifted,
move the pinion in the opposite direction the gear was moved
with respect to the cone center. If the gear mounting distance
is reduced, increase pinion setting distance, and vice versa, an
amount proportional to the number of teeth in the respective
members. For example: on a 10 to 1 gear set, if the ring gear
was moved .010" (.25mm) , the pinion should be moved 0.001"
(.025mm). This would be necessary only if the contact pattern
had visually shifted due to movement of the ring gear while
adjusting backlash.
When setting a used set of gears, follow the method outlined
above. However, depending upon the amount of wear, it may be
necessary to set the gears up with slightly greater backlash in
order to obtain proper contact. Proper tooth contact pattern
is the most important factor for correct installation.
Should a condition be encountered where correct contact cannot
be obtained as described in this manual, the Geareducer should be
returned to Marley in exchange for a factory reconditioned unit.
Installation and Lubrication
Refer to the Operation and Maintenance Instructions at the
beginning of this manual.