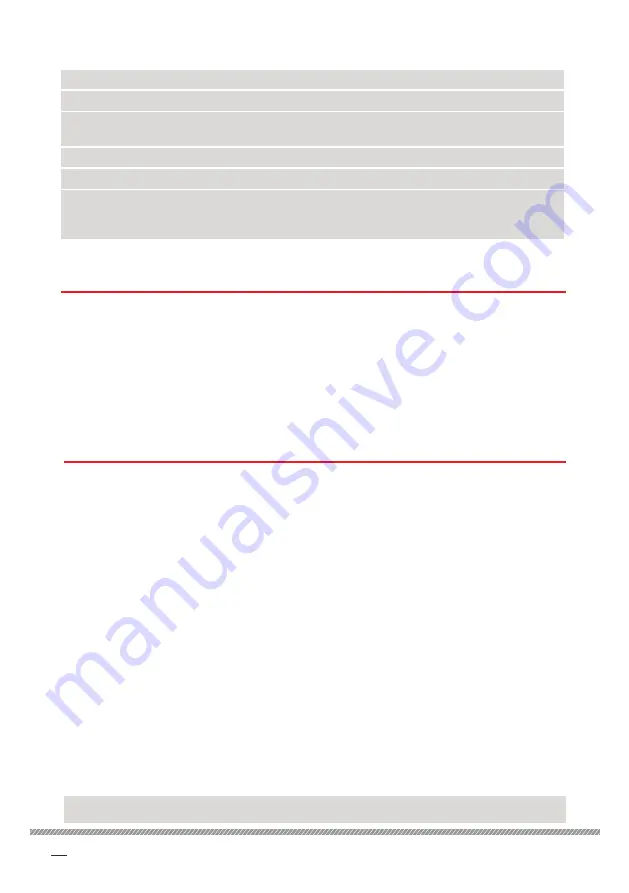
12
Commissioning
5.
For an intial start, adjust the following presets:
3.3 Operating the drive
1.
Note the armature voltage rating given on the motor rating plate.
2.
Apply mains power to the unit.
The ON lamp will light.
3.
Close the RUN contact.
4.
Gradually increase the external setpoint to start the motor rotating. If the direction is
wrong, TURN OFF THE POWER, WAIT FOR THE MOTOR TO STOP TURNING and swap over
the cables connected to the A1+ and A2- terminals.
5.
MAX SPEED
: Increase the external setpoint further to ramp up to full speed. Fine adjust
using the MAX SPEED preset to achieve the armature voltage stated on the motor rating
plate.
6.
Reduce the external setpoint to ramp the drive to zero. The motor will stop rotating.
7.
MIN SPEED
: Adjust MIN SPEED to provide a speed preset.
8.
RAMP UP/RAMP DOWN
: Run the motor up and down while adjusting the RAMP UP and
RAMP DOWN potentiometers.
9.
STABILITY
: Adjust the STAB potentiometer to improve response. Clockwise rotation
gives a faster response. (Excessive rotation in either direction may lead to instability,
depending on load.)
10.
IR COMP
: Speed droop on heavy loads may occur where armature voltage feedback is
used. Compensate for this by clockwise adjustment of the IR comp preset. Excessive
rotation may lead to instability.
The drive is now commissioned for use in Armature Voltage feedback.
MIN SPEED
Fully anti-clockwise
UP RAMP
Fully anti-clockwise
DOWN
RAMP
Fully anti-clockwise
STABILITY
Mid-way
IR COMP
Fully anti-clockwise
MAX
CURRENT
Set MAX CURRENT from your motor rating plate. Rotating clockwise gives
0-100% of the drive current rating as set by switches S1/S2, e.g. if S1/S2 are
set to limit the current to 8 A, 50% rotation will give a 4 A current limit.
6.
If a tachogenerator is fitted, disconnect the tacho wire from terminal T9 and insulate.
3.2 Pre-operation motor check list
With no power applied,
complete the following check list:
• Check for the correct insulation between all motor windings and earth (disconnect all
drive cables before testing).
• Check inside the motor connection box for foreign objects, damaged terminals etc.
• Check that motor brushes are in good condition, correctly seated and free to move in
brush boxes.
• Check for the correct action of brush springs.
• Check that motor vents are free of any obstruction or protective covers.
Summary of Contents for 1600i
Page 6: ......