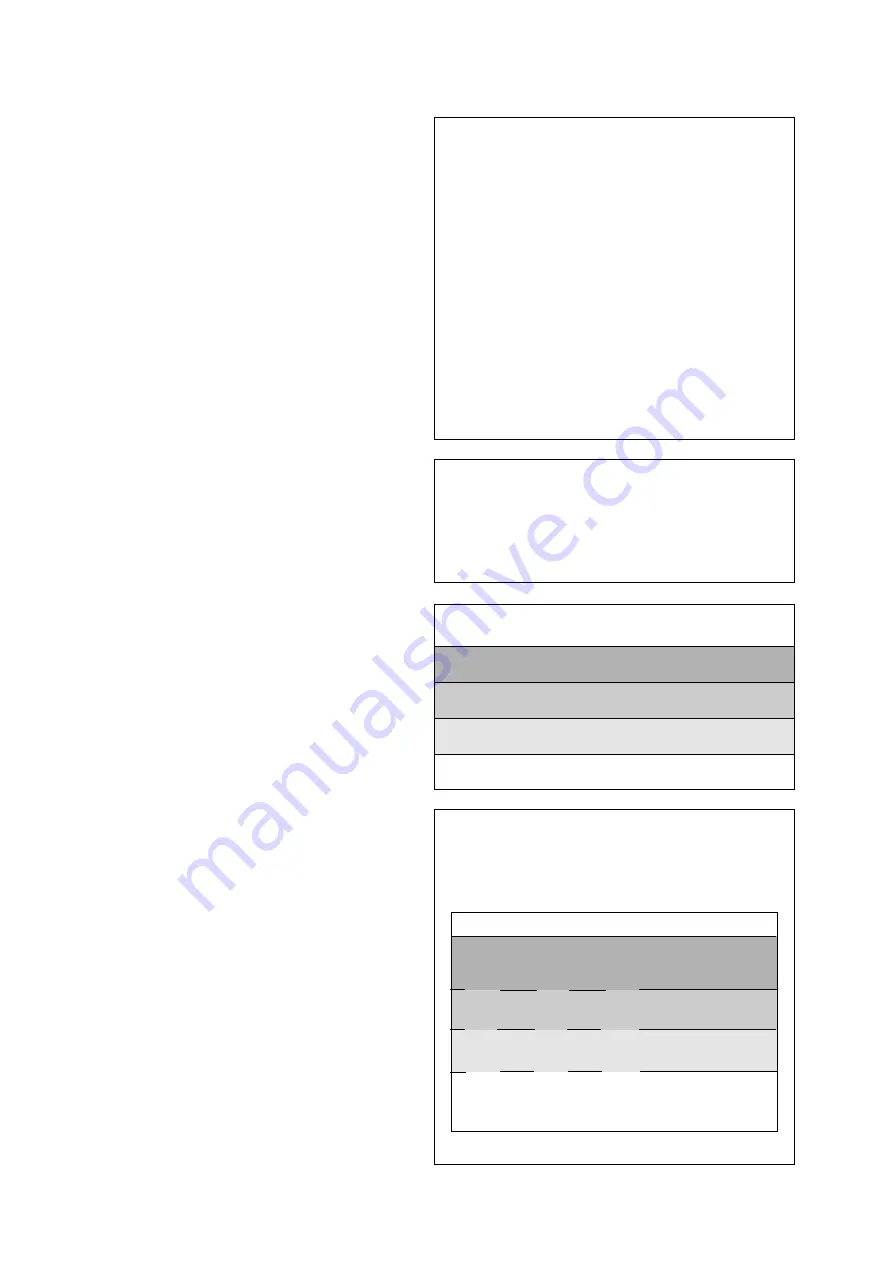
8
Technical data are subject to change without notice.
ISO 9001 certified. © Copyright SPM 1996-9. 71519.Z
SPM Instrument AB
• Box 4 • S-645 21 Strängnäs • Sweden
Tel +46 152 22500 • Fax +46 152 15075 • [email protected] • www.spminstrument.se
Recording of Readings
The SPM follow-up form provides space for readings
in all three directions at up to four different points,
which should adequately cover most industrial ma-
chines. Experience will soon show which of the points
and directions provide the most useful information
for diagnosing a specific problem on any particular
piece of plant.
In the case of a furnace extract fan (example oppo-
site), three measuring points should be sufficient. With
this type of machine, the usual problem is out of
balance caused by soot on the impeller blades. That
makes the vibrations measured in the horizontal di-
rection at point 3 most significant. General directives
for maintenance (6) should be based on the readings
at that point.
A graph (11) is the best way to show clearly all signifi-
cant changes of the vibration level. To keep the form
simple, draw only the graph for the most significant
direction (7), normally that giving the highest read-
ings.
In the example, the extra space (17) was used for a
second graph for the important point 3, in order to
show the axial vibration trend as well.
There are no general rules about how often vibration
should be measured. The intervals between readings
- a day, a week, perhaps a whole month - depend
wholly on the individual machine, its work, its impor-
tance for the plant and on the rate of change in its
vibration level. Obviously an exhaust fan with a soot
problem will need more frequent surveillance than a
fresh air fan, but only practical experience can help to
determine the optimal number of checks per month.
If the form is to be used for machines class I, V or VI,
fill in the relevant vibration levels under (16). Note
that the condition bands (12-15) only apply if the
machine is classed correctly.
Preparation
1
Record chart number
2
Machine designation, number and
location
3
Machine class
4
Machine sketch with numbered
measuring points
5
Vibration class and levels (cross out
figures which do not apply)
6
Directives for maintenance
7
Number of measuring point and
direction plotted on chart
8
H = horizontal, V = vertical, A = axial
Measurements
9
Date of measurement
10
Measured value in three directions
11
Plotted value of main direction
Machine Condition
12
dark red
–
bad condition
13
pale red
–
just tolerable
14
pale green
–
acceptable
15
dark green
–
good condition
Chart Modification
16
Other machine classes and their
respective vibration levels:
bad
tolerable
acceptable
good
I
V
VI
0.43
2,80
4.33
0.28
1.77
2.80
0.18
1.10
1.77
0.11
0.71
1.10
0.07
0.43
0.71
0.04
0.28
0.43
0.03
0.18
0.28
0.02
0.11
0.18
0.01
0.07
0.11