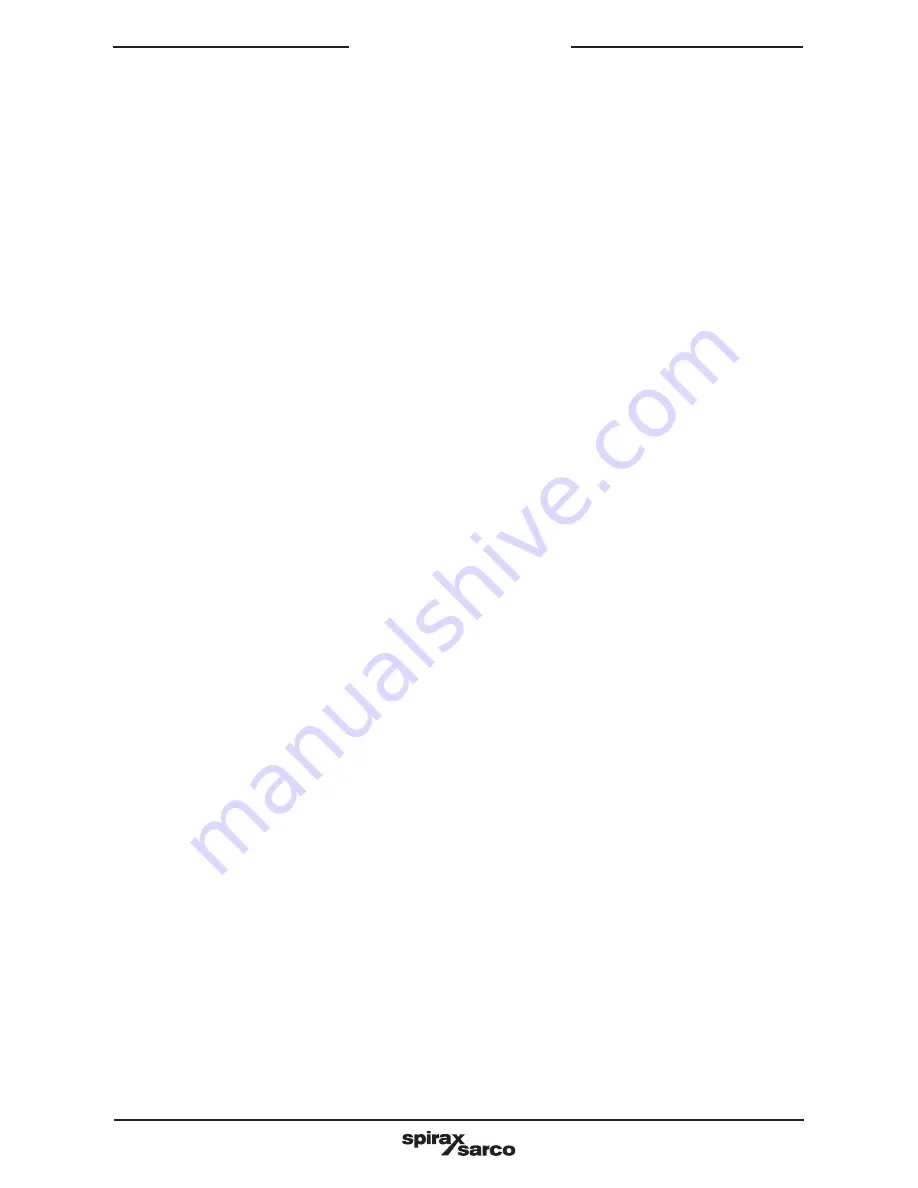
3.561.5275.201
8
See also separate Installation and Maintenance Instructions for the control valves. For details of
differential pressures associated with KE and LE valves refer to Technical Information Sheet TIS
1.312 for PN3000 series actuators and TIS 1.313 for PN4000 series actuators.
The actuators should be installed in such a position as to allow full access to both actuator and
valve for maintenance purposes. The preferred mounting position is with the actuator and valve
spindle in the vertical position above or below the horizontal pipework.
The actuator ambient limits are -20°C to +110°C. For low temperature conditions the air supply
must be dry. For high temperature conditions, insulate the control valve and pipework to protect
the actuator.
Warning
The actuator housing must only be pressurized on the opposite side of the diaphragm to the
springs. The housing vent cap must left be unrestricted.
3.1
Fitting Actuator to Valve
(Ref. to fig. 1, 2, 3 & 4)
1.
Locate valve in support fixture and secure in position. Remove the actuator mounting nut
from the valve.
2.
Remove the connector clamp brackets (20) from the actuator spindle by removing the 2
nuts and bolts (21). Remove the valve spindle adaptor (19).
3.
Assemble the valve spindle adaptor to the valve spindle ensuring the valve is on its seat.
Adjust the distance between the adaptor top face and the bonnet shoulder to the value
indicated in Fig. 3.
Secure in this position with the spindle locknut.
Do not tighten.
4.
Slacken actuator adaptor lock nut (18) & screw adaptor (17) up the actuator spindle as far
as possible.
Do not tighten locknut.
5.
Assemble air fitting to actuator housing and locate complete actuator onto the valve assembly.
6. For PN3000 series actuators only.
Apply the maximum air signal pressure (refer to actuator label) to the actuator and assemble
the mounting nut on to valve bonnet.
Tighten to within ~1 full turn of fully tight.
7. For PN3000 series actuators only.
Apply the minimum air signal pressure (refer to actuator label) to the actuator.
8. For PN4000 series actuators only.
Apply the maximum air signal pressure (refer to actuator label), to the actuator.
9.
Adjust the top adaptor until it locates with the spindle adaptor.
Do not tighten locknut
.
10.
Re-assemble the connector clamp brackets with the threaded holes of the bracket at the
same side as the travel indicator plate.
Secure with the 2 nuts and bolts. Torque to 2 nm.
11.
Open & close valve 3 times to allow all components to self align (this is why locknuts are left
untightened at this stage).
12.
Apply air signal to position valve @ ~ 50% lift position.
13.
Tighten both adaptor locknuts.
Caution:
take care not to turn actuator spindle as this may
cause damage to diaphragm.
14.
Tighten mounting nut to secure actuator to valve and torque to 50 nm.
15.
This completes the main assembly. However, to check the spindle alignment is perfect,
temporarily remove the connector clamp brackets & inflate the actuator to separate upper
& lower spindle adaptors.
If correctly aligned the connectors will meet each other in perfect alignment. If not, slacken
all tightened nuts & repeat assembly sequence.
Note than some lateral movement between the actuator yoke & the valve bonnet is provided
on more recent PN3000 & PN4000 actuators.
16.
Finally, check actuator signal range and stroke at open/closed positions by applying air
signal pressure to the actuator in line with actuator nameplate.
Check for smooth operation and adjust travel indicator on yoke if necessary.
Note:
Before mounting the connectors It may be necessary to adjust the position of the actuator
spindle adaptor. Follow the spring adjust procedure as described in Section 4.
3. Installation
Summary of Contents for PN 3000 Series
Page 19: ...3 561 5275 201 15 ...