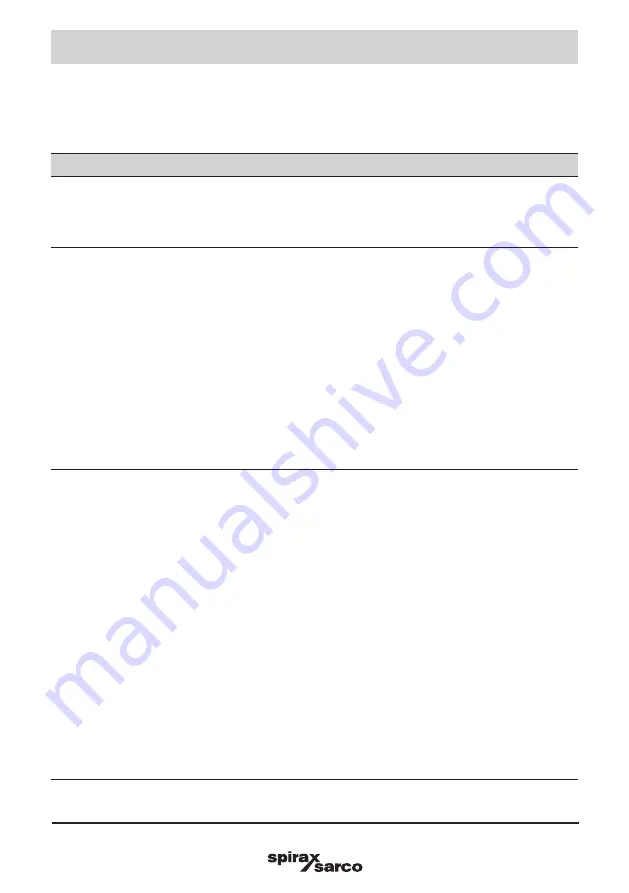
IM-P157-38
CMGT Issue 4
41
Steam/Water Mixing Stations (MkII valves - 2002 onwards) Safety and Operation
Before investigating further it is always advisable to check the following:-
Ensure that the steam and water supplies are turned on and have running condition pressures in excess of
3.0 bar g (43.5 psi g) for cold water, for hosedown stations. The pressure gauges show whether the expected
supply pressures are reaching the mixing valve.
Symptom
Cause and corrective action
Gland leaking
When the mixing valve has been in operation for a short time it is possible that
the gland packing (
14
) may leak very slightly. The gland nut should then be
tightened. Continual leakage may cause the knob to seize.
Note:
Check gland tightness after a few days operational service.
Valve delivers cold
water only
Hot water supply
Disconnect the downstream pipework or hose from the valve outlet, and check
if the hot water flows. Before operating the valve, ensure adequate safety
procedures are in place to prevent injury from the hot discharge. Operate valve
slowly. If hot water is now flowing the downstream pipework is causing too much
resistance. Please refer to Table 1, page 6 and alter pipework to suit.
Incoming steam supply line - is steam reaching the mixing valve?
Check the pressure on the gauge prior to the ball valve. If this is zero or lower
than expected, check that all supply isolating valves are fully open; check
strainers are not blocked, (including steam/water mixing valve strainer); ensure
that the inlet check valve is installed with direction of flow arrow in the right
direction. Ensure that the check valve cone is free to move.
Fixed loading spring
Check that the correct fixed loading spring (
11
) is fitted. Replace with the lower
rated spring if necessary.
Hot water outlet
temperature too low
Fixed loading spring
Check that the correct fixed loading spring (
11
) is fitted. Replace with
low
the
lower rated spring if necessary.
Bypass valve setting
Turn the temperature adjustment knob (
12
) to the right as far as possible, it may
be necessary to remove the knob retaining screw (
10
), so that the knob can be
moved the other side of an internal stop in the valve body. Measure the
temperature, if correct remove the temperature adjustment knob (
12
) and
replace in a position 45° anticlockwise from its previous position. If the
temperature is not correct remove the bypass screw (
9
) insert a screwdriver
and turn the bypass valve (
8
) clockwise. Measure the temperature, if incorrect
continue to turn the bypass valve clockwise, if incorrect refit screw (
9
). If the
temperature is still too low and the bypass valve has been turned fully clockwise,
then the cold water supply should be reduced by the installation of an LRV
water reducing valve.
Condensate problem
Incoming steam pipework must be free of condensate, which would pass slowly
through the steam inlet valve and the mixed water would take longer to heat
up. This may not appear to be a problem if the valve has been commissioned
with a waterlogged steam line, however condensate can cause waterhammer,
and the steam line should be properly drained using a steam trap. The incoming
steam line should always be taken off the top of the steam main.
7. Fault finding