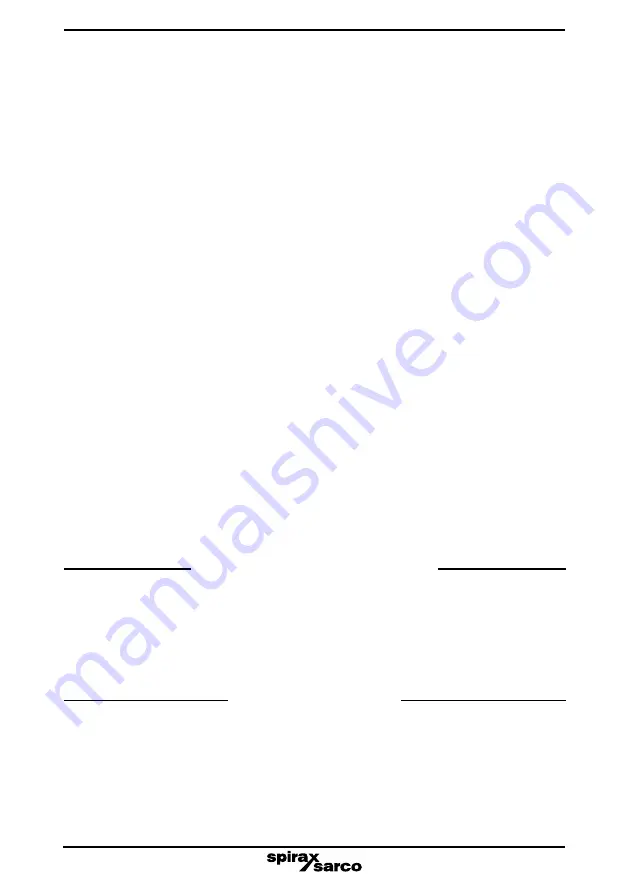
IM-P145-02
ST Issue 2
9
4. Commissioning
After installation or maintenance ensure that the system is fully functioning. Carry out tests on
any alarms or protective devices.
5. Operation
The float trap is a continuous discharge trap, removing condensate the instant it forms. On
start-up, the thermostatic air vent allows air to bypass the main valve preventing the system air
binding. Hot condensate will close the air vent tightly, but as soon as it enters the main chamber
of the trap, the float rises and the lever mechanism attached to it opens the main valve - keeping
the system drained of condensate at all times. When all condensate has been removed, the float
drops and closes the main valve. Float traps are renowned for their high start-up load handling
capability, clean tight shut-off and resistance to waterhammer and vibration.
On applications that suffer from steam locking an SLR unit should be fitted see Section 3.11.
3.9
Bypasses are not recommended because they can be left open and can cause the trap
to malfunction or allow steam wastage (and possible pressurisation of the condensate
return system).
3.10
If the trap is to be welded into the line this should be done using the electric arc method.
If this method is used the internals need not be removed. If any other welding method
is employed it may cause distortion of the trap body or damage to the internals
3.11
Float traps should be fitted as close as possible to the outlet of the plant to be drained,
otherwise the trap can steam lock. Steam locking occurs when the pipe between the
condensate outlet and the steam trap fills with steam preventing the condensate from
reaching the trap. This can lead to system waterlogging which will affect plant efficiency.
It is very similar to the air locking experienced in water systems.
The most common application where steam locking is a risk, is on rotating cylinders and
other applications where condensate is removed via a dip tube or syphon pipe. Steam
locking can easily be prevented by fitting the trap with a combined thermostatic air vent
and steam lock release valve (SLR).
The SLR valve is opened by turning the spindle anticlockwise. The standard factory setting
is a
½
turn open which equates to an approximate steam 'bypass' of 22 kg/h @ 10 bar.
Site adjustment of the SLR can be achieved by turning anticlockwise to increase the
bypass flow and clockwise to reduce the flow.
Note:
The SLR should not be used to provide 'blowthrough' steam loads which are
usually high and may reduce the working life of the trap. If blowthrough steam is required
consult Spirax Sarco for further details.
3.12
If a float trap is to be situated in an exposed position, it should be either lagged or drained
by a separate, small thermostatic trap.
3.13
Ensure adequate space is left to remove the body from the cover for maintenance.
Minimum withdrawal distance distance for the FTS14 is 135 mm (5.6") for DN15 (
½
") and
DN20 (
¾
") and 145 mm for the DN25 (1").
Summary of Contents for FTS14
Page 2: ...IM P145 02 ST Issue 2 2 ...
Page 12: ...IM P145 02 ST Issue 2 12 ...