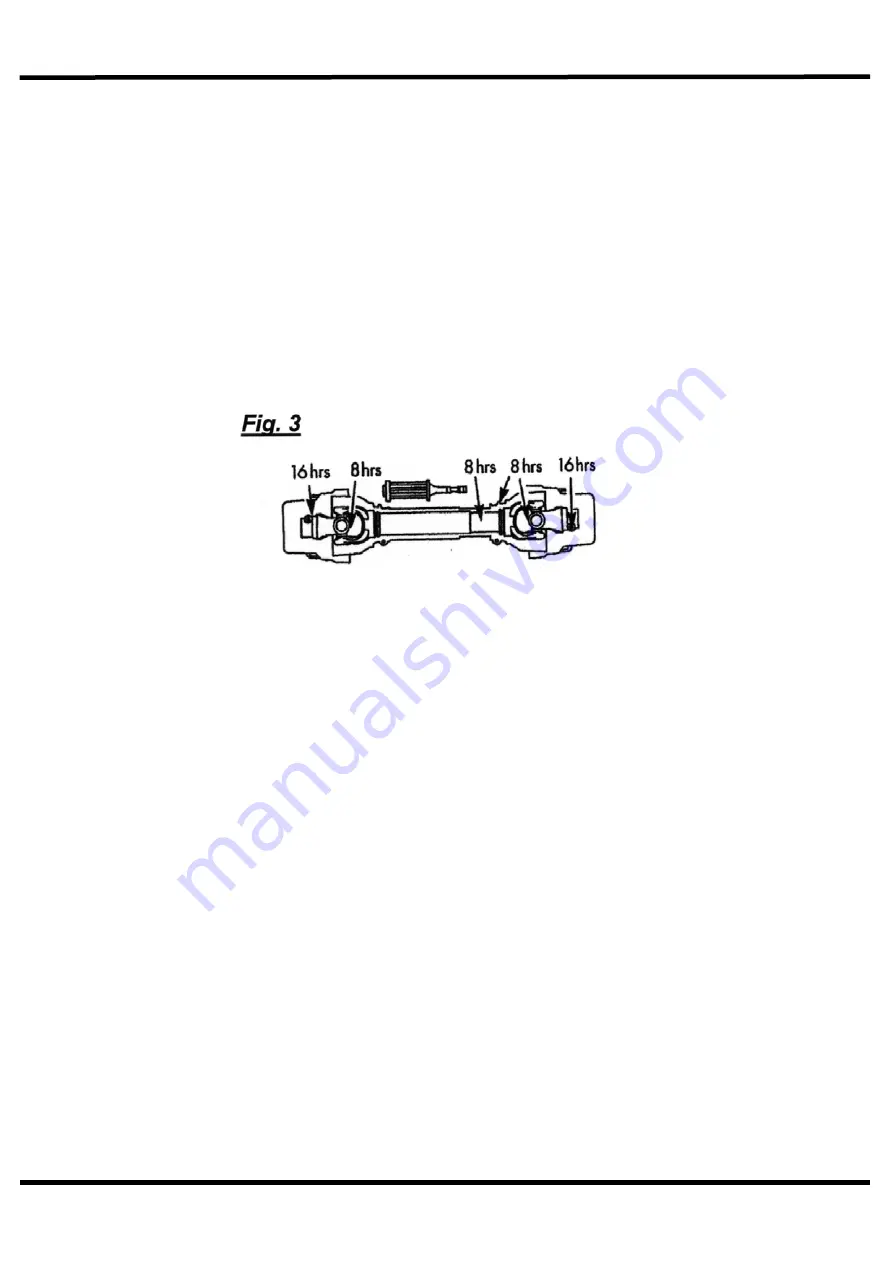
MULTICUT 160/200
17
Daily/Every 8 hours
Grease all grease points, on PTO.
Check condition of blades and blade bushes and ensure all retaining bolts are
fully tight.
Check gearbox oil, replenish with ‘EP90’ gear oil as necessary to the correct
level line on the dipstick provided with each gearbox.
Dismantle and clean PTO sliding surfaces and re-grease. Grease universal
joints (Fig. 3).
Every 20 hours
Grease PTO inner tube and push pins (Fig. 3)
Regularly
Check there is no wrapping of string, plastic, grass or other debris between
rotor boss and blades.
Inspect gearbox seals for leaks.
Regularly check the rotor boss retaining castle nut for tightness (part
no.5771409). First remove the split pin, select the correct size socket in 3/4”
drive and fully tighten the nut.
When replacing the split pin, do not slacken the nut to align the hole, always
tighten.
Failure to regularly check this nut will result in serious wear to hub, which is
expensive to repair.
It is most important that all gearbox and blade bolts are regularly checked to be
very tight.
When the machine is new there will be a ‘bedding in’ period
where very frequent checking is important.