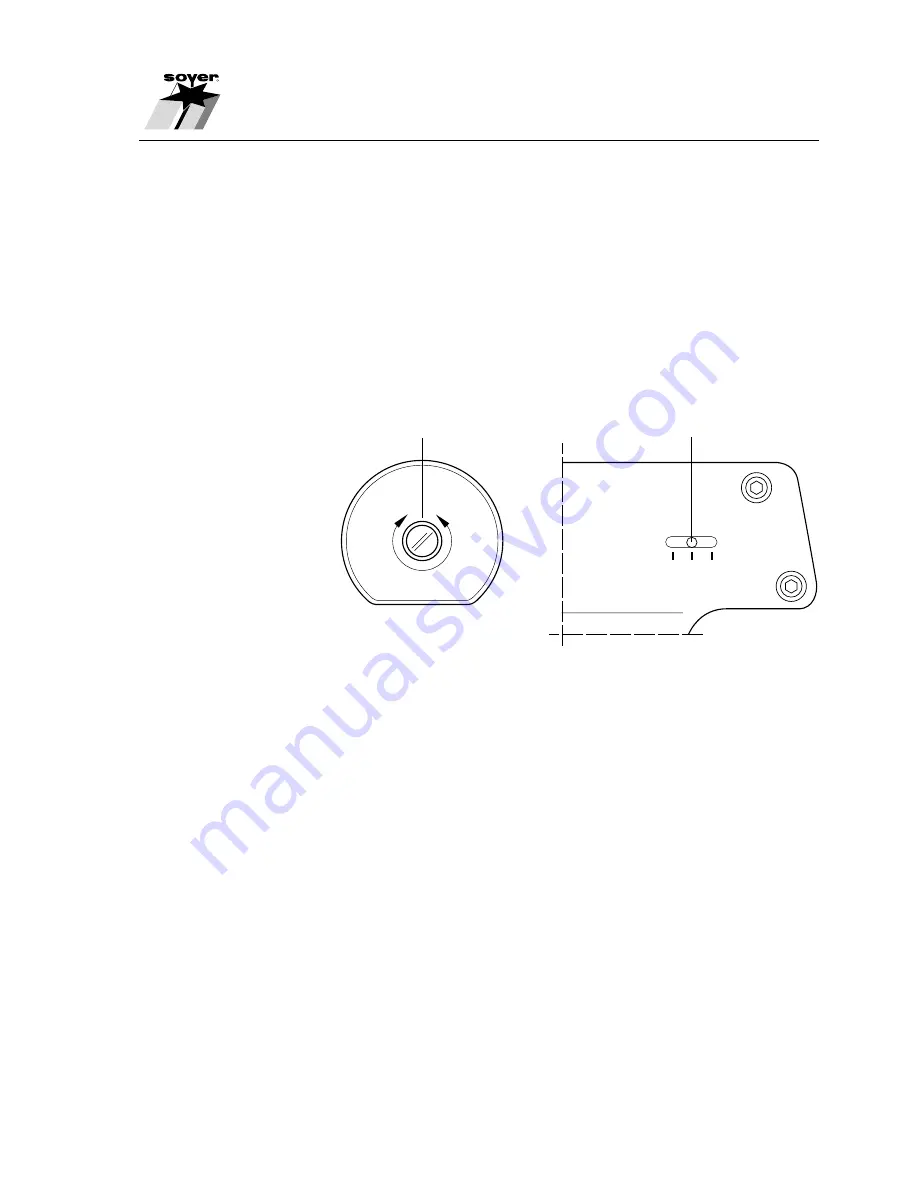
A-3
R
1.3
Adjustment of spring pressure
(does not apply to stud welding pistol PS-3)
When using the stud welding pistol PS-3, adjust the lift instead of the spring
pressure. In this case please leave out chapter 1.3 and refer to chapter 1.4 of
Appendix A "Adjustment of stud welding pistols - Capacitor Discharge".
The pressure with which the stud is pressed against the workpiece during the
welding process is called spring pressure.
The following illustration shows how to adjust the spring pressure of stud
welding pistol PS-1 which is equipped with a spring pressure indicator. Stud
welding pistol PS-3K is provided with a similar spring pressure indicator. For
stud welding pistols PS-0K and PS-1K, there is no spring pressure indicator.
1 Adjusting screw
2 Spring pressure indicator
For all stud welding pistols described here, the spring pressure is adjusted by
means of the adjusting screw (1). The adjusted pressure is indicated at the
spring pressure scale (2). Adjust spring pressure as follows:
• Turn adjusting screw (1) to the left until stop
Indicator position 1
=
low pressure
• Turn adjusting screw (1) 3.5 turns to the right
Indicator position 2
=
medium pressure
• Turn adjusting screw (1) to the right until stop
Indicator position 3
=
high pressure
The spring pressure to be adjusted depends on the material of both welding
stud and workpiece.
Before starting the work, carry out some experimental weldings and test them
to find out the optimum adjustment.
Samples have to be taken during production to ensure constantly good weld-
ing results (see DVS Guideline 0905, Part 2, "Quality assurance of stud welding
joints").
Appendix A/PS-3 - Adjustment of stud welding pistols - Capacitor Discharge
SZ.0041.E
3 2 1
Spring pressure
2
1
Summary of Contents for BMS-10N
Page 1: ...Operating Instructions Stud Welder BMS 10N BMS 10NV R ...
Page 5: ......
Page 6: ...R ...
Page 7: ...R ...
Page 58: ...13 48 Spare parts R ...
Page 68: ...A 10 R Appendix A PS 3 Spare parts Capacitor Discharge ...