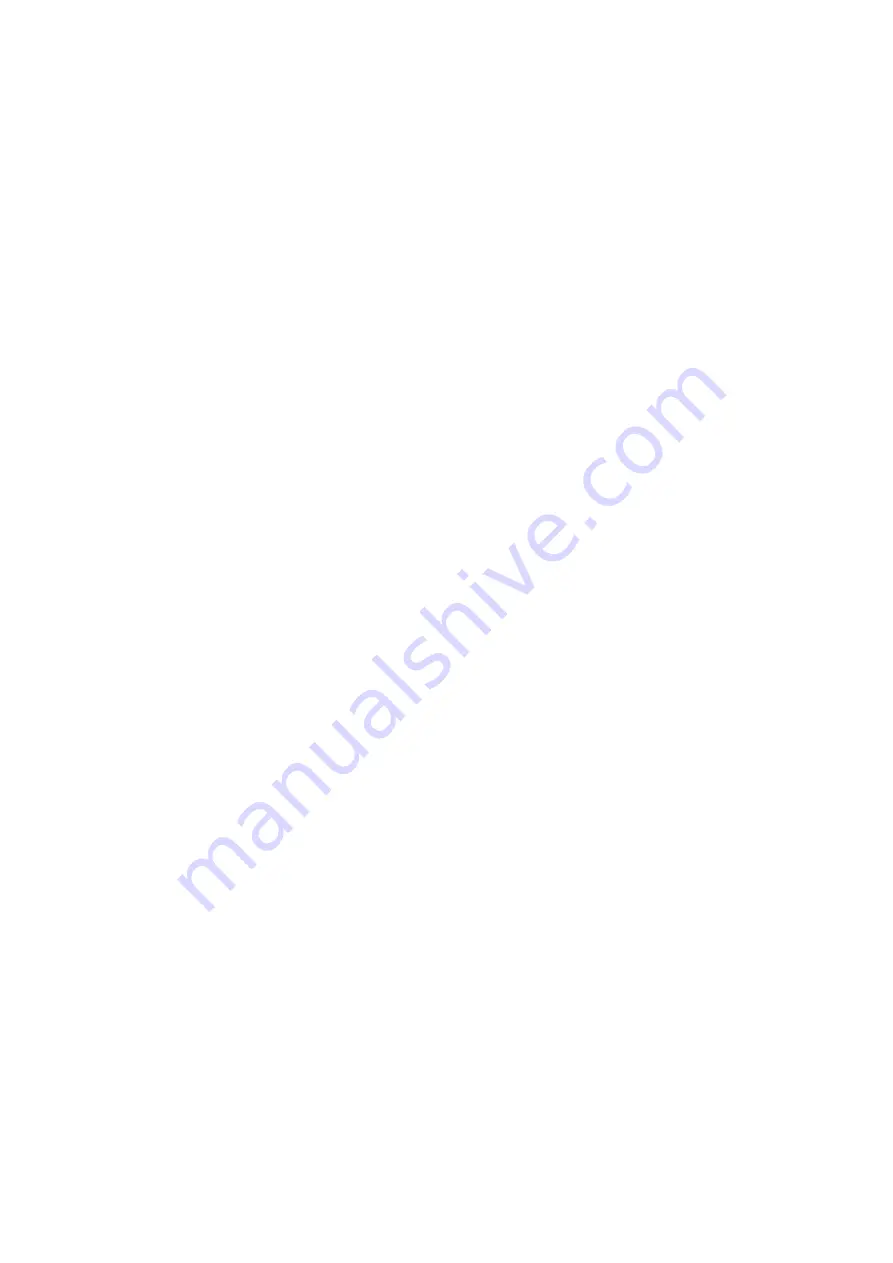
40
The purpose is to test the diagnosis of digital-to-analog converters fault or code flow fault
,
Code flow
may omit the process to update analog signals.
Solution
:
If a fault persists, need to replace controller.
20
)
“ENCODER ERROR”
Cause
:
In the following conditions caused a fault signal
:
Motor input frequency higher than 40 HZ,
encoder signal feedback is higher than 40 HZ in 10 milliseconds . The fault directs at rthe
multi-function encoder.
。
Solution
:
A) Check the electric and mechanical encoder functional, wire was huddled up
B) Check the encoder machinery installation, the internal encoder slide will cause fault alarm.
C) Bearing the electromagnetic noise encoder can also cause alarm, this kind of situation will need to
replace encoder.
D
)
If still have fault after change the encoder may be the problem of controller.
21
)
“TILLER ERROR” Handle switch fault
Cause
:
soft /hard switch input and handle switch input signal don't match.
Solution
:
Check the connection of AMP saab type of CNA#7end and imput voltage of CNA#6 end
(
AMP seal type connection
,
check CNA#29 end and CNA#1 end
)。
If the input of the state is correct
,
that may is the internal controller fault
,
need to replace the controller
。
22
)
“WATCHDOG” watchdog fault
Cause
:
This is a safety detection, implement the diagnosis between nternal main micrcontroller in logic
card and micrcontroller
。
Solution
:
Alarm maybe caused by CANBUS fault
,
it hinders the communication between main mircocontroller and
mircocontroller
,
if not ,need to replace .
23
)
“HARDWARE FAULT” Hardware fault
Cause
:
micro controller can't shut off the of permission end traction function or the permission end of
main contactor end and electric braking .
Solution
:
The logic of the card controller fault, replace the controller.
24
)
“NO CAN MESSAGE N5”
Cause
:
Not receive from the information from micro controller
Solution
:
This alarm may be due to CANBUS fault, it hinders communicationt between the main
microcontroller and the microcontroller. If not,may be controller internal fault, need to change.
。
25
)
“WRONG SETPOINT”
Reason
:
Security detection
,
setting wrong hydraumatic function tested by main microcontroller.