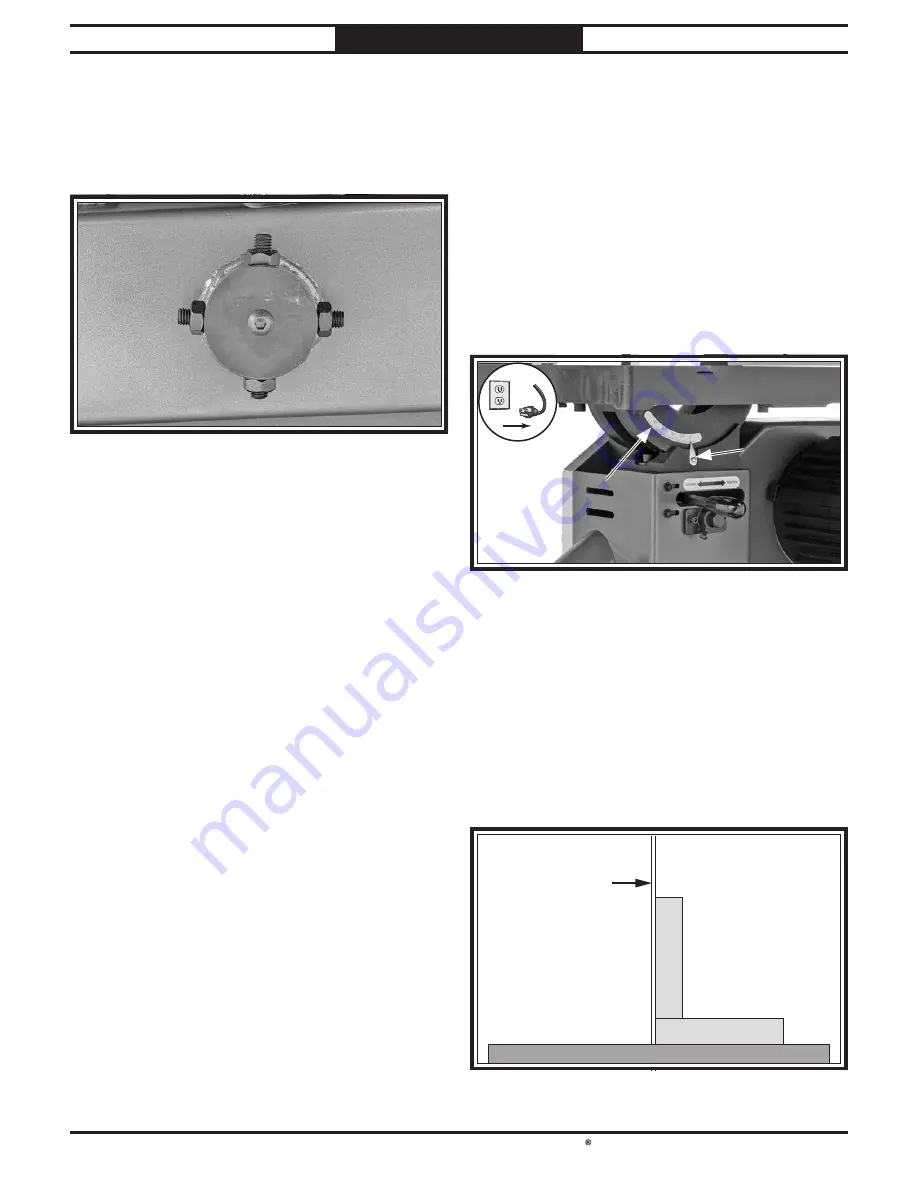
-66-
For Machines Mfd. Since 7/21
South Bend Tools
Model SB1123
S E R V I C E
To adjust lower wheel shaft position:
1.
DISCONNECT MACHINE FROM POWER!
2.
Loosen jam nuts on lower wheel adjustment
hub (see Figure
108).
3.
Loosen one tilt adjustment set screw, then
tighten opposing set screw approximately an
equal amount.
4.
Check wheels with coplanarity gauge, and
repeat Step 3 as needed until lower wheel is
parallel and coplanar with upper wheel.
5.
Tighten jam nuts to lock tilt adjustment set
screws in position.
6.
Perform previous Checking Wheel
Alignment procedure, beginning on Page
63, and adjust wheels as necessary to make
them parallel and coplanar.
7.
When wheels are parallel and coplanar,
remove blade, re-install table, and then re-
install blade.
Calibrating Table Tilt
Scale Pointer
The table tilt scale pointer (see Figure
109
)
was calibrated at the factory. However, after
prolonged use the pointer may shift, requiring
adjustment.
Note:
The table tilt scale functions as a basic
guide only. For high-precision cuts, use a
protractor or bevel gauge to set the angle of table
tilt.
To calibrate table tilt scale pointer:
1.
DISCONNECT MACHINE FROM POWER!
2.
Place one edge of square on table and other
edge of square against blade side, as shown
in Figure 110.
Blade
Table
Square
Figure 110. Adjusting table perpendicular to blade
Adjusting table perpendicular to blade
(side to side).
(side to side).
Tools Needed
Qty
Machinist's Square ................................................1
Phillips Head Screwdriver #2 ...............................1
Figure 108. Lower wheel adjustment controls.
Lower wheel adjustment controls.
Side
Side
Tilt
Tilt
Bottom Tilt
Bottom Tilt
Side
Side
Tilt
Tilt
Adjustment
Adjustment
Hub
Hub
Top Tilt
Top Tilt
Figure 109. Location of table tilt scale and pointer.
Location of table tilt scale and pointer.
Table Tilt
Table Tilt
Scale
Scale
Pointer
Pointer
!