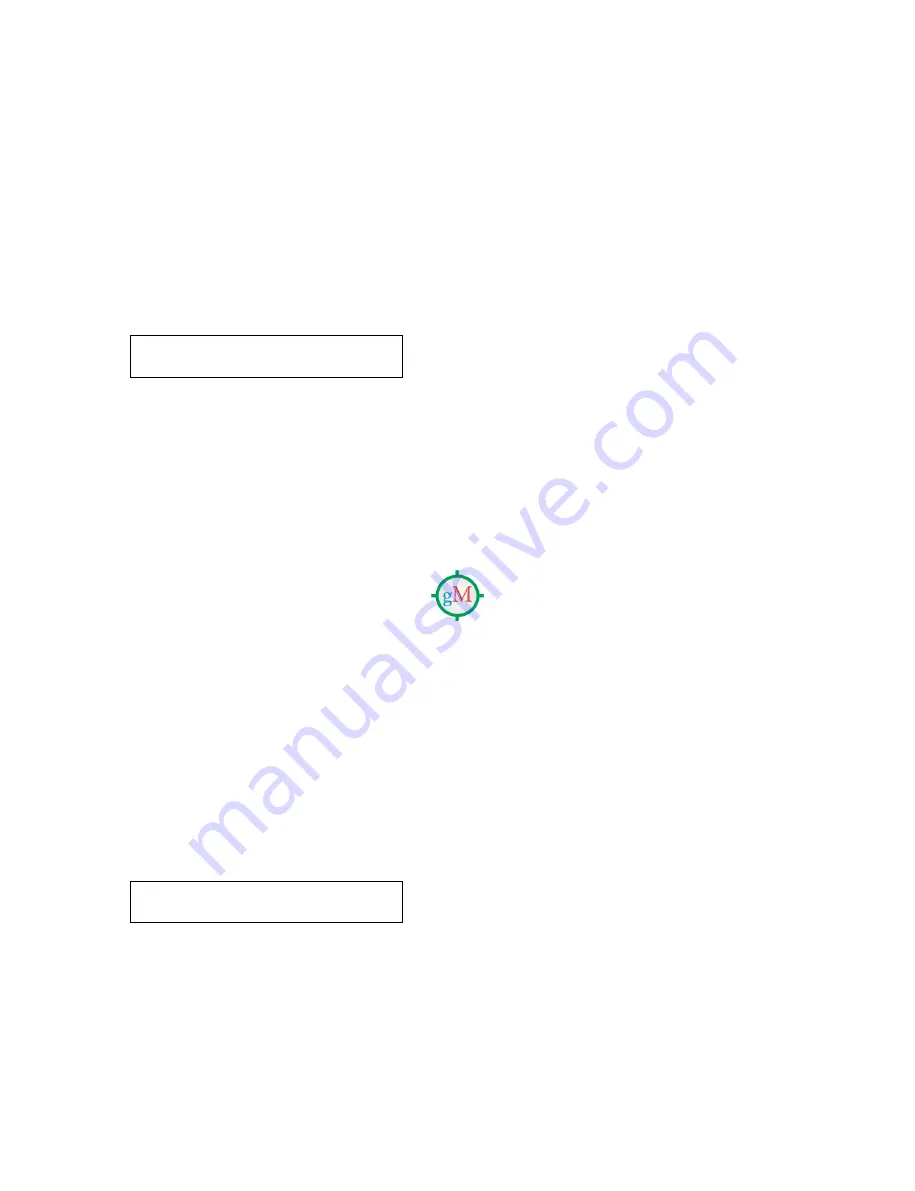
5-12
UP-D70/D70A (UC,CE)
5-5. RESET OF EACH KIND SETTING VALUE
All kind setting values are kept at EEPROM. If it is necessary, all kind setting values can be reset
to initial value.
1. Reset of EEPROM
Perform this reset when replacing EEPROM or MEC-11 board (has EEPROM).
How to Enter .......... After entering service mode, while [STOP] key is depressed, [
↑
] and [
↓
]
keys should be depressed in the ready condition of service mode
(following picture) in order.
READY
A4
QTY
1S
OR
LET
Content ................... following values are returned to the initial value.
user setting value : each value of COLOR ADJUST, GRAY ADJUST
printer condition : ribbon remaining, each error information, TOTAL
PRINT quantity, threshold value of sensor
setting value
: paper size, gamma selection, head voltage value,
luminance quantity of sensor
2. Reset when shipping product
User setting value, TOTAL PRINT, ribbon remaining quantity are changed.
How to Enter .......... After removing a ribbon cassette and a paper feed tray, while depressing
[PRINT], [STOP] and [MENU] keys simultaneously, POWER switch
should be turned on.
Content ................... Thermal head position should be set to 1. Following values (they are not
adjusted when shipping) are returned to initial value.
user setting value : each value of COLOR ADJUST and GRAY ADJUST
printer condition : ribbon remaining quantity, each error information,
TOTAL PRINT
3. TOTAL PRINT reset
Total printing quantity of thermal head is returned to 0. When replacing thermal head, this
reset should be performed.
How to Enter .......... Total printing quantity is indicated from TOTAL PRINT item in service
mode.
TOTAL = 10057
After that, [
↑
], [
↓
] and [PRINT QTY] keys should be depressed simultaneously.