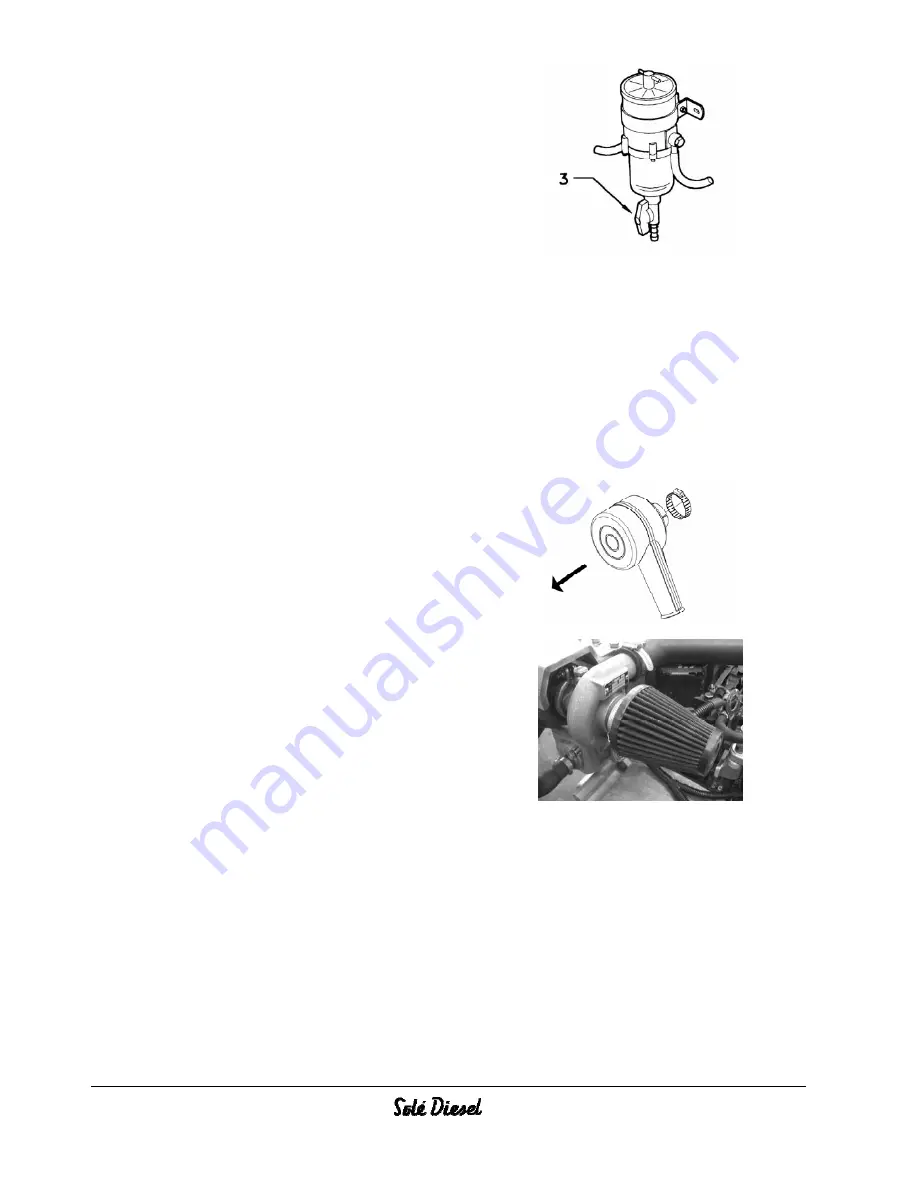
ENG - 29
03917700.ENG rev. 0
(8)
(9)
Fuel decanting filter drainage ( optional ):
Loosen the wing nut (3) (Fig. 7.6) located at the lower side of the
glass vessel and let go all the acrued water. Shut again off the
wing nut and check it does not drip.
Replace the fuel filter element (engine):
The fuel filter is bladded and cannot be cleaned. It must be
replaced at least once every 12 months.
To perform the filter change: Shut off the cock located at the tank
delivery. Unscrew cover filter with a chain spanner. Screw the new
filter to the cover with the hand and at the same time replace the
rubber seals. Carry out the operations at heading 5.1.1 bleeding
air from the fuel system.
Fig. 7.6
(10) Injector checking:
This operation shall be made by a SOLÉ DIESEL service. If a hand-pump is available, monitor the calibration of
injectors, by verifying that the pressures are those listed in paragraph 2.6 of this manual.
(11) Checking incandescent spark plugs:
Supply power to the glow plugs and make sure that they become incandescent, if not renew them.
(12) Change air filter (MINI-17/26/2933/44 models):
See the picture 7.7B. MINI-17/26/29/33/44 engines. Engine is
provided with an intake air filtering component. To perform such a
change, slacken off the central filter clamp, remove the old filter,
byre placing with a new one. The filter and element are an
integral unit.
Fig. 7.7B
Change the conical air filter .
See picture 7.7B. Only for MINI-55 engine. The engine is
equipped with an element air filter. For to clean the air filter, slack
the clamp, extract the filter and follow the instructions indicated
for the producer. After, mount again the filter, tightening the
clamp.
Change the filter following the manufacturer instructions.
Fig. 7.7B
MINI55 air filter, cleaning instructions (use part no. 17710013):
First pre-cleaning the filter. Tap the filter to dislodge any loose dirt, then gently brush with a soft bristle brush. Use the
spray cleaner liberally onto the filter media and left soak for 10 minutes. Large the filter can be rolled or soaked in a
shallow pan of air filter cleaner. Then, remove immediately and let soak for approximately 10 minutes. Rinse off the
cotton filter media with low-pressure tap water. Rising from the clean side to the dirty side. After rising, shake off all
excess water, and dry naturally. The use of other cleaning or drying methods will damage the filter and void the air filter
warranty. After filter is completely dry, oiling (using the spray or squeeze bottle) along each pleat, once only, holding
nozzle 3 seconds away from filter media.
Carefully apply oil on any visible white spots and let sit for 20 minutes. Wipe the gasket or sealing surface with a clean
cloth or paper towel to remove excess oil, prior to installation. DO NOT OVER-OIL AIR FILTER. Over-oiling may
interfere with the proper performance of the engine and/or certain engine components.
Summary of Contents for MINI 17
Page 2: ......
Page 12: ...ENG 10 03917700 ENG rev 0 MINI 29 TMC40 all types of TMC40 MINI 29 TTMC35A2 ...
Page 13: ...ENG 11 03917700 ENG rev 0 MINI 33 RONIM V MINI 33 TMC40 all versions MINI 33 TTMC35A2 ...
Page 14: ...ENG 12 03917700 ENG rev 0 MINI 44 SMIR3 MINI 44 TTMC35P MINI 44 TTMC35A2 ...
Page 39: ......