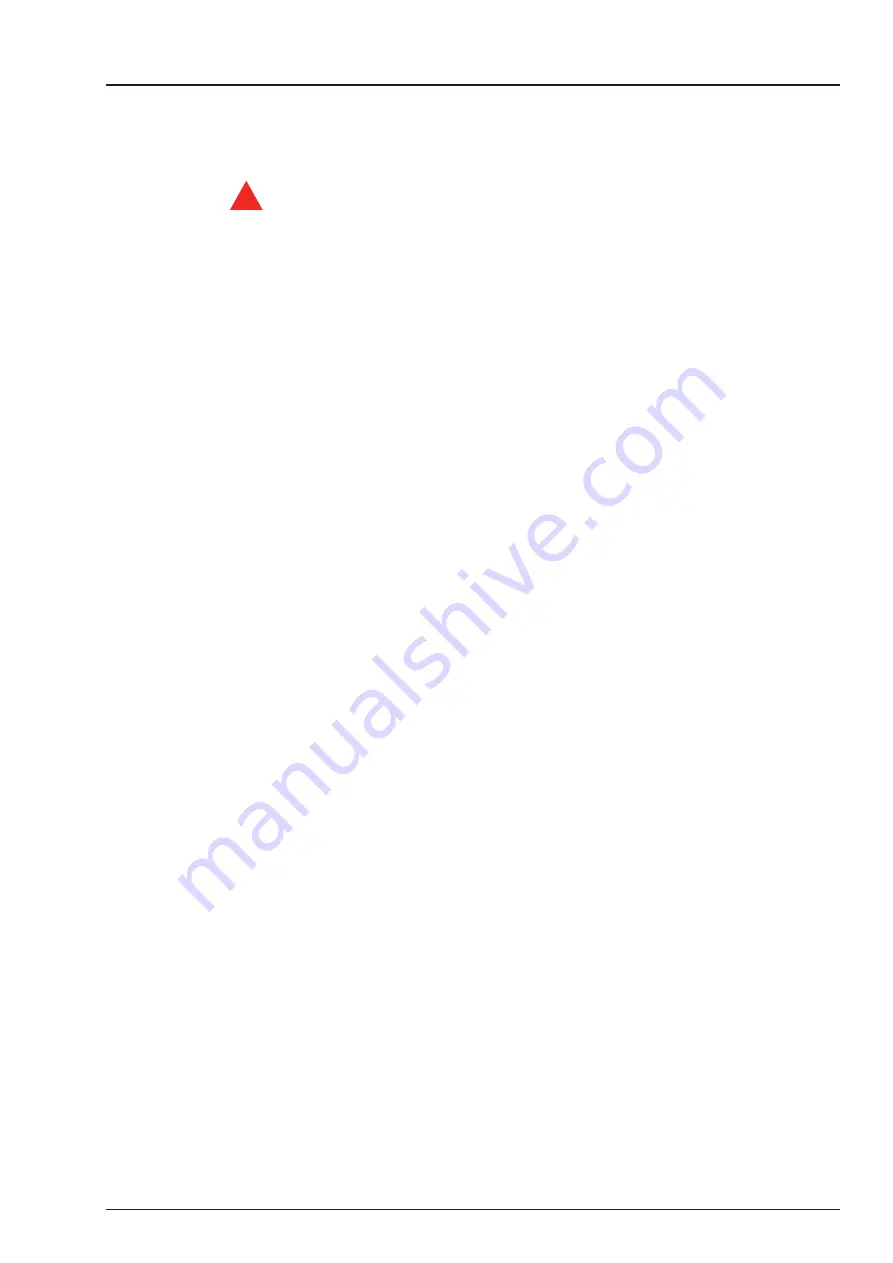
PUSH PRO -0120843
11
System Function Inspection
Refer to “Controls and Indicators” on page 6 for the
locations of various controls and indicators.
!
Warning
STAND CLEAR of the work platform while
performing the following checks.
Before operating the machine, survey the work
area for surface hazards such as holes, drop-offs,
bumps and debris.
Check in ALL directions, including above the
work platform, for obstructions and electrical
conductors.
1. Move the machine, if necessary, to an
unobstructed area to allow for full elevation.
2. Pull the Lower Control Emergency Stop Switch to
the ON position.
3. Turn the Upper Control Emergency Stop Switch
clockwise to the ON position.
4. Visually inspect the scissors structure, lift cylinder,
and hoses for cracked welds and structural
damage, loose hardware, hydraulic leaks, loose
wire connections, and erratic operation. Check
for missing or loose parts.
5. Press and hold the ground operation button
inward. Test each machine function from the
lower control station (refer to Figure 2).
6. Test the emergency lowering system for proper
operation.
7. Push the Lower Control Emergency Stop Button
to check for proper operation. All machine
functions should be disabled. Pull the Lower
Control Emergency Stop Button outward to
resume.
8. Enter the platform and close the gate.
9. Check that the route is clear of obstacles
(persons, obstructions, debris), is level, and is
capable of supporting the wheel loads.
10. Test each machine function from the upper control
station by engaging the interlock and operating
the function controls (refer to Figure 3).
11. Push the Upper Control Emergency Stop Button
to check for proper operation. All upper control
machine functions should be disabled. Turn the
Upper Control Emergency Stop Button clockwise
to resume.
12. Check to ensure that the Auto Brake system
works correctly by raising the machine slightly
from the lower controls. Check that the brake is
engaged against the rear castor wheels. Check
to make sure the machine will not move when
elevated.
System Function Inspection
Summary of Contents for S3006P
Page 2: ......
Page 7: ...PUSH PRO 0120843 5...