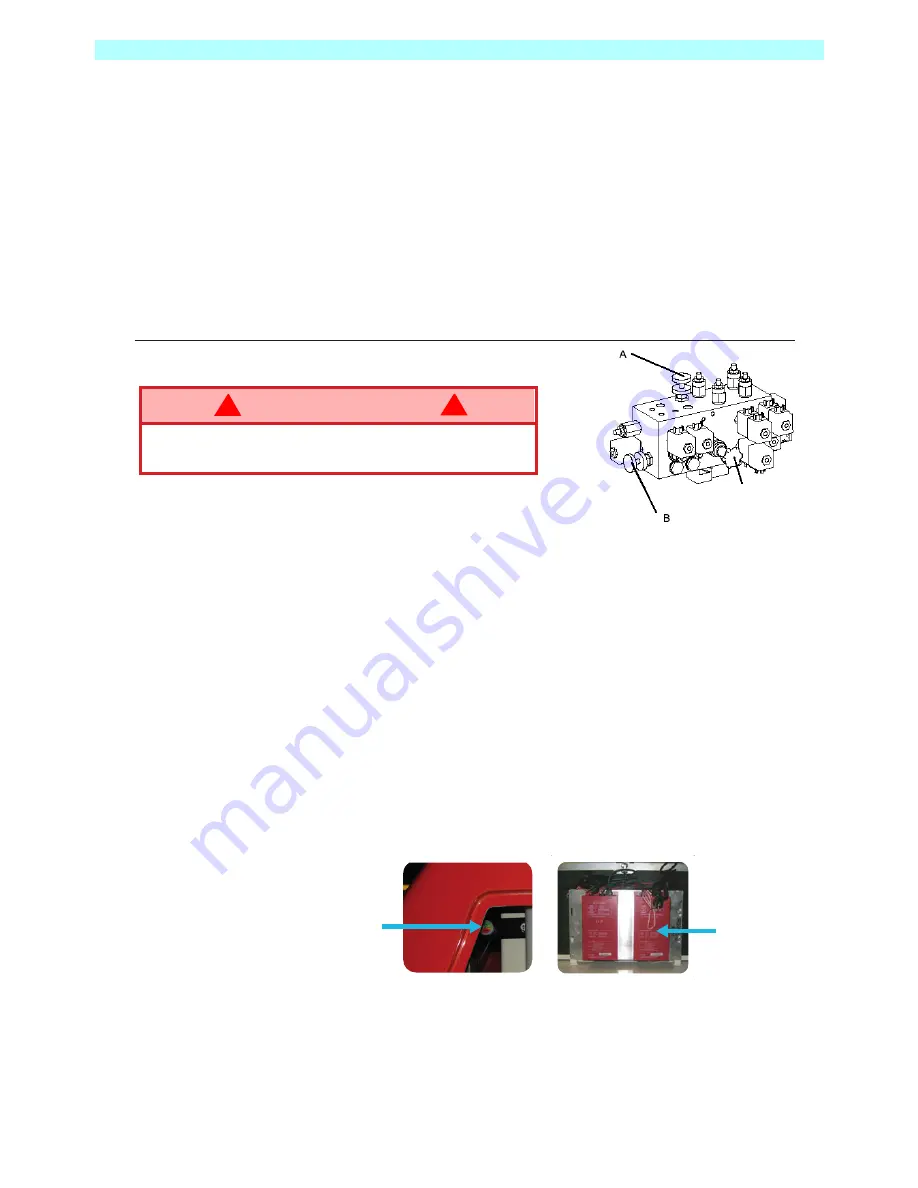
2.
Operation & Specifications
2 - 15
Proceed as follows:- (Refer to the valve block drawing Figure 6.)
1. Fully lower the jib boom and the mast sections. Rotate the mast into the stowed position.
2. Turn the Upper Control Box Keyswitch to the OFF position and remove the key.
3. Remove the rear GRP cover from the chassis and locate the hydraulic control valve block.
4. The hand valve marked ‘A’ should be turned fully clockwise to close. The hand valve marked ‘B’
should be turned fully anti-clockwise to open.
5. Operate the red handpump a number of times to develop sufficient pressure to ‘separate’ the
internal brake disks. These brakes are integral with the hydraulic drive motors.
NOTE:
The machine can now be safely towed or winched.
6. On completion of towing/winching, reverse the position of the rotary hand valves ‘A’ and ‘B’. The
handpump becomes inoperative when the valves are returned to their normal position.
Figure 6: Valve Block-Towing Valve
s
!
!
RISK OF SERIOUS INJURY
. Releasing the brakes will cause the
machine to move uncontrollably on a slope. Damaging momentum can
be developed due to the large mass of a slow moving machine
W A R N I N G
2.6 AFTER USE & STORAGE
AFTER USE EACH DAY
1. Ensure that the platform (masts and jib) are fully lowered.
2. Park the machine on firm and level ground, never on a grass surface.
3. Turn the key switch to the OFF position and remove.
4. Put the batteries on charge.
BATTERY CHARGING
Before charging check that:-
1. The correct mains voltage and current is available to the charger.
The MB machine is fitted with a high output charging assembly. this consists of two 24V 30A 900W
Chargers. The chargers can be linked together if the supply voltage and current are high enough
to meet the power demand. If the power supply is not good enough, a single charger can be used.
If this option is taken, it is important that charger ‘A’ is used, as it is the one linked to the remote
display for battery charge level.
2. Check that the extension cord(s) is in good condition and is no longer than 8M (26fT). 1.5mm
Sq (12 AWG) or larger cable is required. Ensure that the plug(s) is of the correct rating and is
compatible with the electrical installation into which it will be plugged.
3. The charger(s) will turn on automatically after going through a self test sequence. the remote LED
on the control Panel will indicate the status of charging.
Handpump
‘A’
LED Remote
Charge Indicator.
Summary of Contents for MB20J
Page 1: ...JANUARY 2018 01 00054 MB20 01 00071 MB26...
Page 2: ......
Page 4: ......
Page 6: ...NOTES...
Page 30: ...2 Operation Specifications 2 20 NOTES...
Page 31: ......