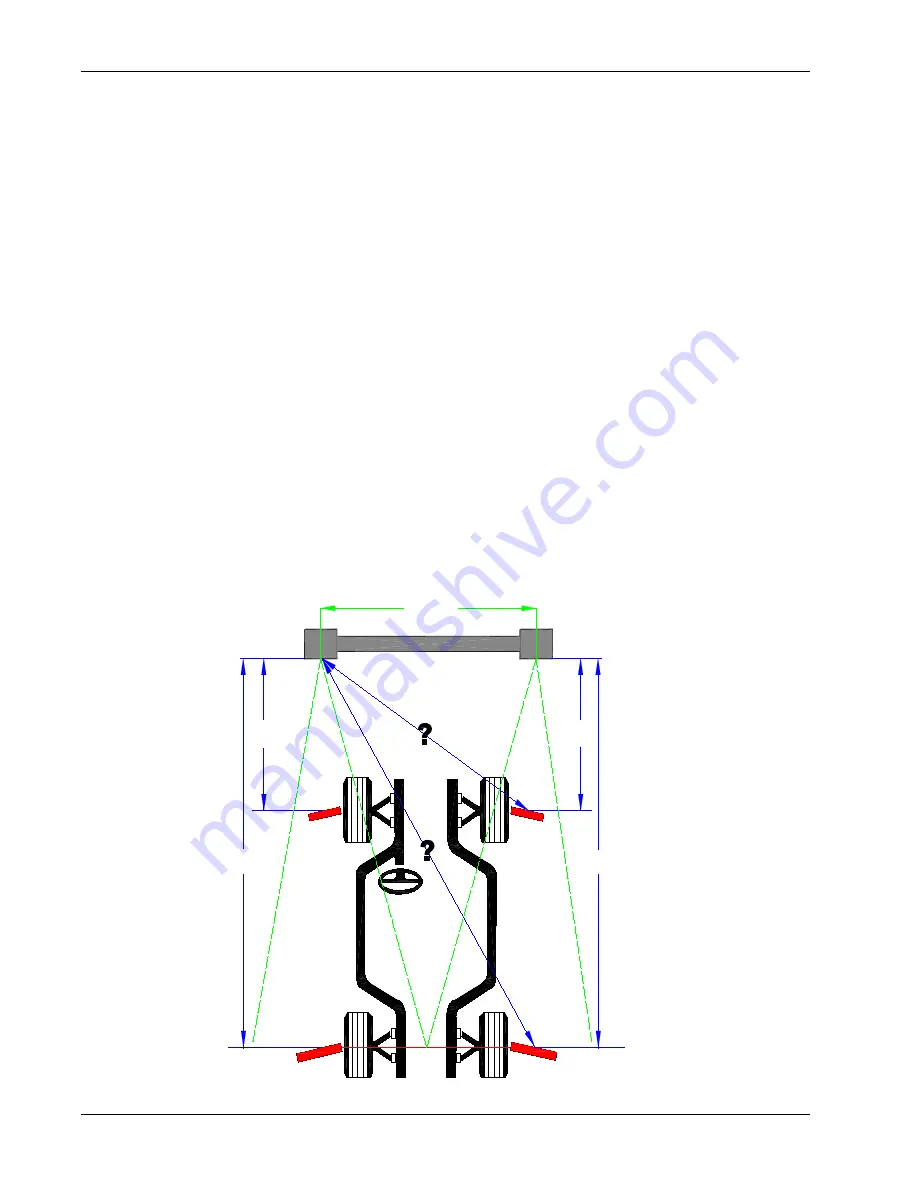
RCP
24
Theory of Operation
When the vehicle is rolled, the 3D software directly locates the spindles and now knows 4 distinct points in
space with respect to the cameras that are part of the vehicle. Since the vehicle is now off the rack turn-
tables, it is necessary to roll it to is start position to perform any corrections. The aligner uses the software
when rolling the vehicle as a check of the results of the compensation. As the operator moves the vehicle we
repeat the positioning sequence. When the vehicle returns to the turntables we have a new measurement of
spindle locations. The software then compares the results of the roll with those earlier; if they agree, the pro-
gram is satisfied and moves on; if they do not agree an error message appears called “Wheel Wobble” and
we are forced to repeat positioning until they agree. This is one of many examples of where the 3D Aligner
performs “quality checks” to insure the highest degree of accuracy possible.
SIDE-TO-SIDE DETERMINATION
The 3D Aligner gathers target images utilizing two cameras mounted on the ends of a beam. This beam is
positioned higher than the vehicle’s wheels to allow the cameras to see the rear targets (the front targets are
smaller, allowing easier viewing of the rear). Each camera can see a front and rear target on its side of the
vehicle, and thus determine their locations and orientations, and find the two spindles on that side. However,
each camera cannot see the targets on the other side of the vehicle. When determining alignment angles
such as thrust angle and setback, it is necessary to “connect” the vehicle sides, to know the relationship of the
left side to the right side. To do this, the 3D Aligner must know the positions of each camera with respect to
one another.
To get an idea of the type of analysis the 3D Aligner program must do. In the picture there is a vehicle with all
targets attached. The program can determine the distance from each camera to the front and rear targets on
its side of the vehicle as indicated by the check marks using perspective. What it cannot do directly is deter-
mine the distance from the camera to the front and rear targets on the other side (question marks). The way
to find the cross-distance is to know the distance between the 2 cameras called “RCP” on the figure. If RCP
is known it is straightforward mathematics to determine the cross-distance in question since two sides of a
right triangle are known – Pythagorean Theorum: a
2
+ b
2
= c
2
. But how does the program know the dimen-
sion RCP? We must tell it!
Summary of Contents for UHR Ultra
Page 1: ...Service Manual Ultra UHR Ultra and V3400 WHEEL ALIGNER May 2014 ...
Page 13: ...11 AC DC POWER DISTRIBUTION ...
Page 14: ...12 AC DC POWER DISTRIBUTION ...
Page 16: ...14 Theory of Operation Figure 2 Top Field of View Figure1 Side Field of View ...
Page 19: ...17 Theory of Operation Configuration using single pole wheel clamp ...
Page 46: ...44 NOTES ...
Page 67: ...65 Diagnostics ...
Page 68: ...66 NOTES ...
Page 83: ......
Page 84: ...05 07 2014 2014 Impreso en U S A 309 Exchange Avenue Conway AR 72032 TEEWA546P4 Rev C ...