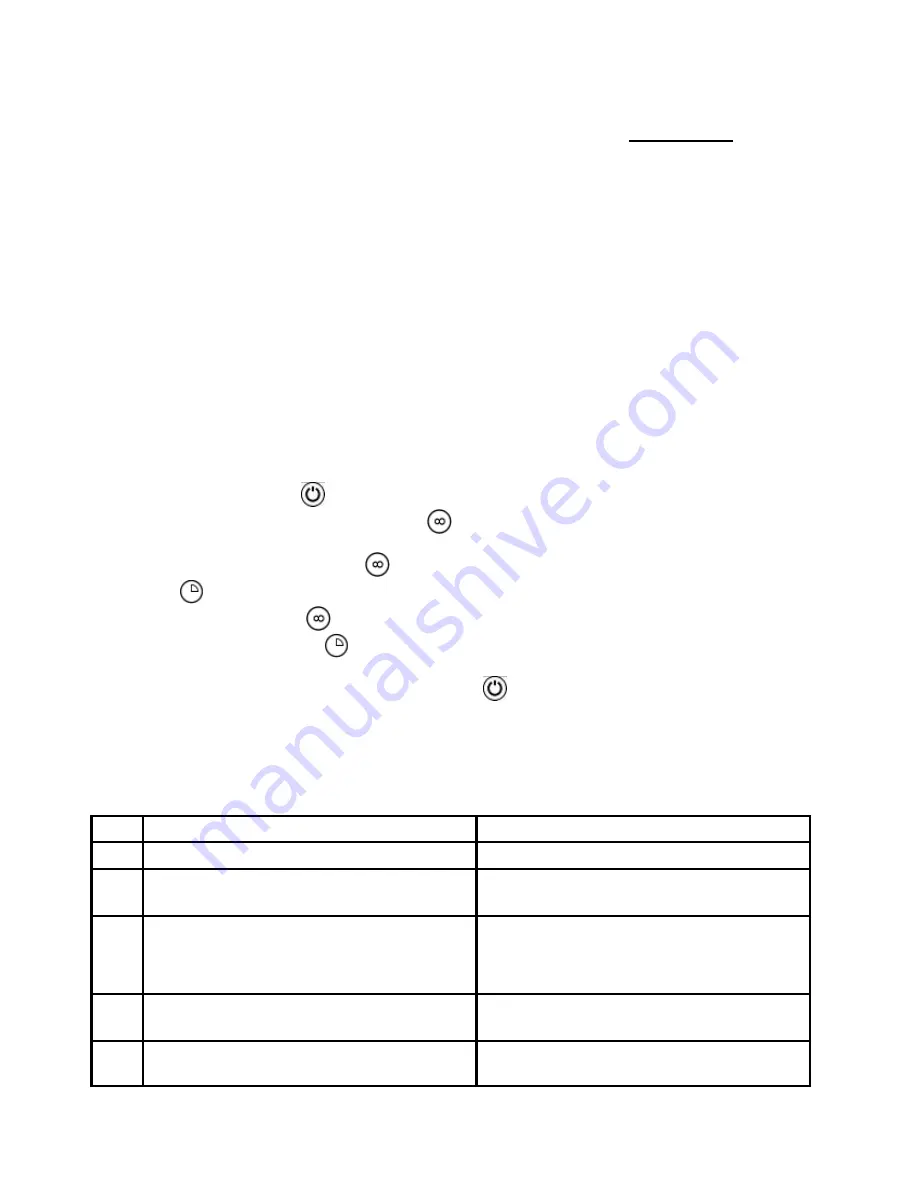
8
6
SETTINGS (only models CW400RSD - CW400R – CWC500R)
MACHINE CONFIGURATION PARAMETERS ( Intended for technical personnel, not for the user )
P0
RINSE CYCLE TIME, from 1 to 5 minutes, preset to 2
P1 BOILER
TEMPERATURE, from 60 to 95 °C, preset to 86 °C
P2
TANK TEMPERATURE, from 40 to 65 °C, preset to 55 °C
P3
RINSE DURATION from 10 to 40 sec., preset to 13 sec
During the rinse phase the drain pump is also activated (if installed), and is kept active for 4 seconds after
the end of the rinse phase
P4
BOILER STOP FUNCTION: 0 = not installed, 1 = installed
,
preset to 0
P5 MACHINE
TYPE:
5 = with three wash cycles without Break Tank/Air Trap for Hood
6 = with three wash cycles with Break Tank /Air Trap for Hood
P6 DRAIN OPTION
WITH OVERFLOW
: 0 = not installed. 1 = installed
,
preset to 1
The drain is activated
each time the load electrovalve is activated
.
Once the rinse phase has finished, the drain pump continues to function for 4 seconds
The drain cycle can be activated manually by the operator by keeping the drain button
pressed for 3 seconds. The drain cycle has a duration of 120 seconds, at the end of
which the machine automatically shuts off.
P9
WATER LOADING DURATION, from 1 to 10 minutes, preset to 10 minutes.
To access the factory menu the following procedure must be followed:
1) Shut the machine off with the
button
2) Within 6 seconds of machine shutdown press the
button 7 times
At the end of the 6 seconds, the message “ P0” will appear on the screen.
3) Select the parameter to modify with the
button
4) Press the
button to view the selected parameter on the display
5) Modify the parameter with the
button
6) Confirm the modification with the
button
7) Select, in the same way, other parameters to be modified and modify them as described above
8) After having set all of the machine’s parameters, press the
button to exit.
7
SCREEN DISPLAYED ANOMALIES
The machine is capable of signaling a series of malfunctions on the display.
If the problem persists after having turned the machine off and then on again, act as indicated below:
E1
Boiler sensor malfunction
Substitute
E2
Tank sensor malfunction
Substitute
E3
Water loading timeout ( the water loading duration
has exceeded the time set in P9 )
Electrovalve inspection – Verify that the water
faucet is open
E6
Draining anomaly. At the end of the draining phase
the CPU still detects water in the Tank. This may
be due to:
Drain pump malfunction
Drain tube blockage
Tank Pressostat malfunction
Drain cycle time ( P0 ) set too low
E7
30 minute Tank timeout
Inspect the Tank and boiler thermostats
Check for inverted sensors
E8
15 minute boiler timeout
Inspect the Tank and boiler thermostats
Check for inverted sensors
Summary of Contents for CWC500R
Page 5: ...4 ...