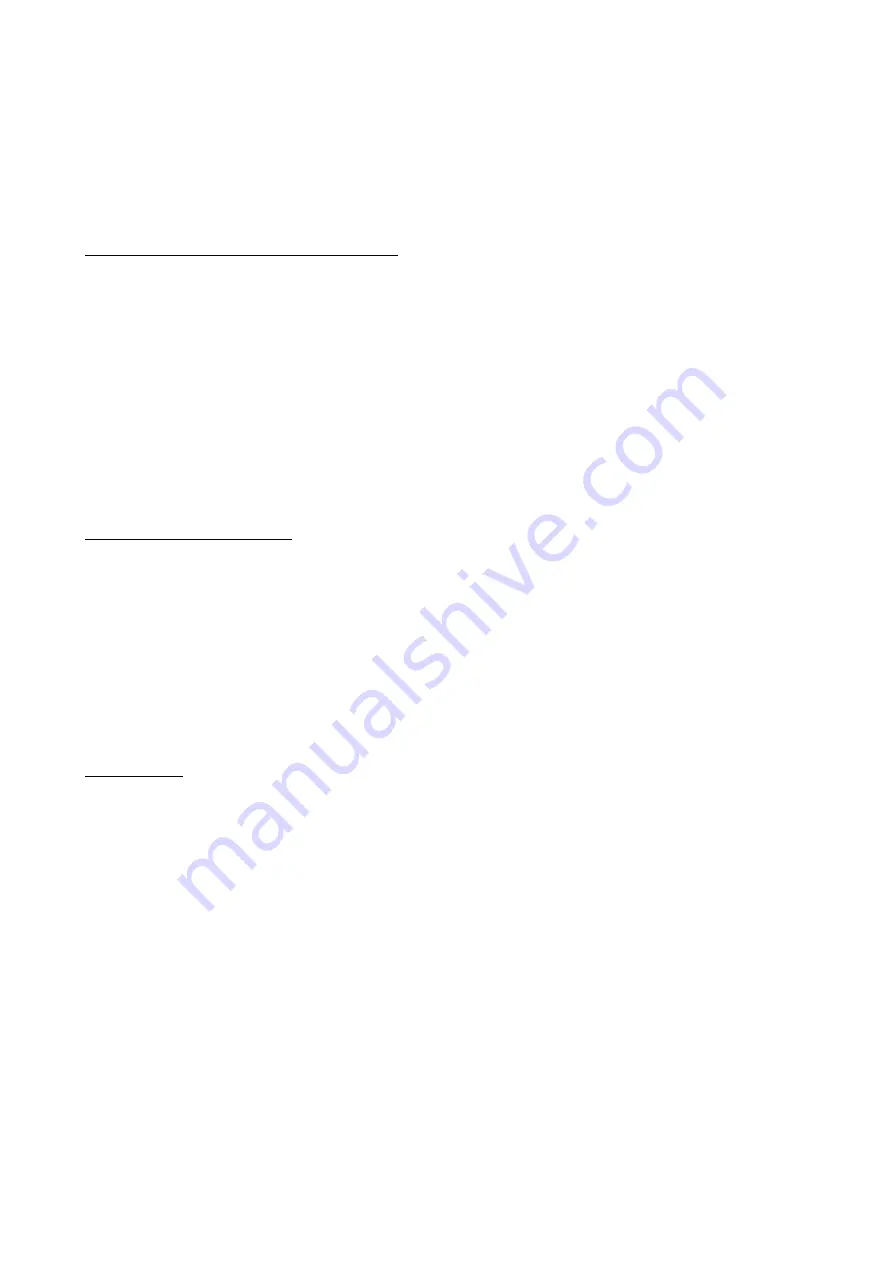
3. in case of a correct wiring but incorrect output voltage, replace the potentiometer
itself.
4. If the potentiometer output voltage is correct and the measured value in the display
is incorrect, and the proper terminals of the 23-way connectors are correctly wired
to their correspondent inputs in potentiometer circuit, replace the AC-M1.
Pump motor commands active on start:
●
Alarm code
: 50
●
Alarm level
: this is a reversible warning (while the error condition is active, all the
pump motor functions are inhibited).
●
Alarm cause
: a pump motor command is active when the system is turned on.
In case of such alarm, follow this procedure:
1. Before starting to operate, turn off any active command (both levers and switches);
2. Be sure that the lift and descending command switches are not active;
Seat switch open on start:
●
Alarm code
: 63
●
Alarm level
: this is a reversible warning (while the error condition is active, all the
pump motor functions are inhibited).
●
Alarm cause
: when the system is started, the seat switch is found open, or after the
main breaker has been closed, the seat switch remains open for at least
seat
switch delay
seconds.
In case of such alarm, verify if the seat switch is defective.
Wrong start:
●
Alarm code
: 64
●
Alarm level
: warning; the main breaker is opened and the pump and drive motors
are stopped.
●
Alarm cause
: when the system is started, the accelerator pedal is found pressed or
a forward/reverse switch is found active.
In case of such alarm, follow this procedure:
1. Verify whether a switch was active or the pedal pressed when you turned on the lift
truck.
2. Verify whether the start, forward or reverse switches are stuck close; in this case,
replace the faulty switches.
3. Verify if the pedal circuit voltage always exceeds 1/3 of its maximum range; in this
case, replace the pedal trimmer.
PRELIMINARY VERSION
44
Summary of Contents for AC-M1
Page 1: ...AC M1 AC M1 PRELIMINARY VERSION...
Page 9: ...Figure 1 AC M1 All the dimensions are in millimetres PRELIMINARY VERSION 9...
Page 13: ...Figure 2 Planarity specifications for the AC M1with aluminium baseplate PRELIMINARY VERSION 13...
Page 21: ...Figure 3 General electrical vehicle PRELIMINARY VERSION 21...
Page 32: ...Figure 5 Interconnection cable PRELIMINARY VERSION 32...
Page 36: ...Figure 9 Drawing of COMPACT display slot PRELIMINARY VERSION 36...