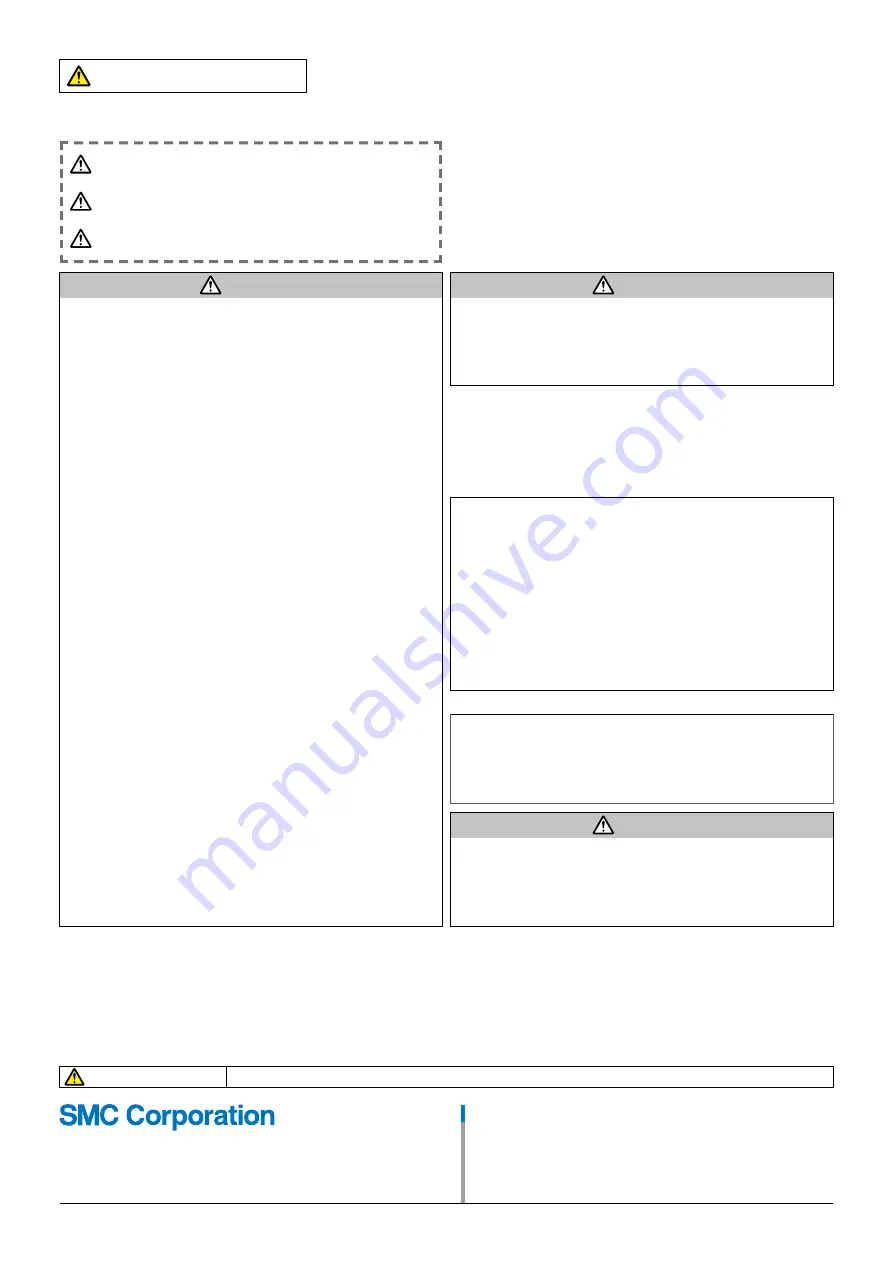
Akihabara UDX 15F,
4-14-1, Sotokanda, Chiyoda-ku, Tokyo 101-0021, JAPAN
Phone: 03-5207-8249 Fax: 03-5298-5362
https://www.smcworld.com
© 2022 SMC Corporation All Rights Reserved
Specifications are subject to change without prior notice
and any obligation on the part of the manufacturer.
D-G
Safety Instructions
Be sure to read the “Handling Precautions for SMC Products” (M-E03-3) and “Operation Manual” before use.
Caution
SMC products are not intended for use as instruments for legal
metrology.
Measurement instruments that SMC manufactures or sells have not been
qualified by type approval tests relevant to the metrology (measurement) laws
of each country. Therefore, SMC products cannot be used for business or
certification ordained by the metrology (measurement) laws of each country.
Compliance Requirements
∗
1) ISO 4414: Pneumatic fluid power – General rules relating to systems.
ISO 4413: Hydraulic fluid power – General rules relating to systems.
IEC 60204-1: Safety of machinery – Electrical equipment of machines.
(Part 1: General requirements)
ISO 10218-1: Manipulating industrial robots – Safety.
etc.
Caution
indicates a hazard with a low level of risk which,
if not avoided, could result in minor or moderate injury.
Caution:
Warning
indicates a hazard with a medium level of risk which,
if not avoided, could result in death or serious injury.
Warning:
Danger :
Danger
indicates a hazard with a high level of risk which,
if not avoided, will result in death or serious injury.
Warning
Caution
1. The compatibility of the product is the responsibility of the
person who designs the equipment or decides its
specifications.
Since the product specified here is used under various operating conditions,
its compatibility with specific equipment must be decided by the person who
designs the equipment or decides its specifications based on necessary
analysis and test results. The expected performance and safety assurance
of the equipment will be the responsibility of the person who has determined
its compatibility with the product. This person should also continuously
review all specifications of the product referring to its latest catalog
information, with a view to giving due consideration to any possibility of
equipment failure when configuring the equipment.
2. Only personnel with appropriate training should operate
machinery and equipment.
The product specified here may become unsafe if handled incorrectly. The
assembly, operation and maintenance of machines or equipment including
our products must be performed by an operator who is appropriately trained
and experienced.
3. Do not service or attempt to remove product and machinery/
equipment until safety is confirmed.
1. The inspection and maintenance of machinery/equipment should only be
performed after measures to prevent falling or runaway of the driven
objects have been confirmed.
2. When the product is to be removed, confirm that the safety measures as
mentioned above are implemented and the power from any appropriate
source is cut, and read and understand the specific product precautions
of all relevant products carefully.
3. Before machinery/equipment is restarted, take measures to prevent
unexpected operation and malfunction.
4. Contact SMC beforehand and take special consideration of
safety measures if the product is to be used in any of the
following conditions.
1. Conditions and environments outside of the given specifications, or use
outdoors or in a place exposed to direct sunlight.
2. Installation on equipment in conjunction with atomic energy, railways, air
navigation, space, shipping, vehicles, military, medical treatment,
combustion and recreation, or equipment in contact with food and
beverages, emergency stop circuits, clutch and brake circuits in press
applications, safety equipment or other applications unsuitable for the
standard specifications described in the product catalog.
3. An application which could have negative effects on people, property, or
animals requiring special safety analysis.
4. Use in an interlock circuit, which requires the provision of double interlock
for possible failure by using a mechanical protective function, and
periodical checks to confirm proper operation.
1. The product is provided for use in manufacturing industries.
The product herein described is basically provided for peaceful use in
manufacturing industries.
If considering using the product in other industries, consult SMC beforehand
and exchange specifications or a contract if necessary.
If anything is unclear, contact your nearest sales branch.
Limited warranty and Disclaimer/
Compliance Requirements
The product used is subject to the following “Limited warranty and Disclaimer” and
“Compliance Requirements”.
Read and accept them before using the product.
Limited warranty and Disclaimer
1. The warranty period of the product is 1 year in service or 1.5 years after
the product is delivered, whichever is first.
∗
2)
Also, the product may have specified durability, running distance or
replacement parts. Please consult your nearest sales branch.
2. For any failure or damage reported within the warranty period which is clearly our
responsibility, a replacement product or necessary parts will be provided.
This limited warranty applies only to our product independently, and not to any
other damage incurred due to the failure of the product.
3. Prior to using SMC products, please read and understand the warranty terms
and disclaimers noted in the specified catalog for the particular products.
∗
2) Vacuum pads are excluded from this 1 year warranty.
A vacuum pad is a consumable part, so it is warranted for a year after it is delivered.
Also, even within the warranty period, the wear of a product due to the use of the vacuum pad
or failure due to the deterioration of rubber material are not covered by the limited warranty.
1. The use of SMC products with production equipment for the manufacture of
weapons of mass destruction (WMD) or any other weapon is strictly prohibited.
2. The exports of SMC products or technology from one country to another are
governed by the relevant security laws and regulations of the countries involved
in the transaction. Prior to the shipment of a SMC product to another country,
assure that all local rules governing that export are known and followed.
These safety instructions are intended to prevent hazardous situations and/or
equipment damage. These instructions indicate the level of potential hazard with
the labels of
“Caution,” “Warning” or “Danger.” They are all important notes for
safety and must be followed in addition to International Standards (ISO/IEC)
∗
1)
,
and other safety regulations.
Safety Instructions