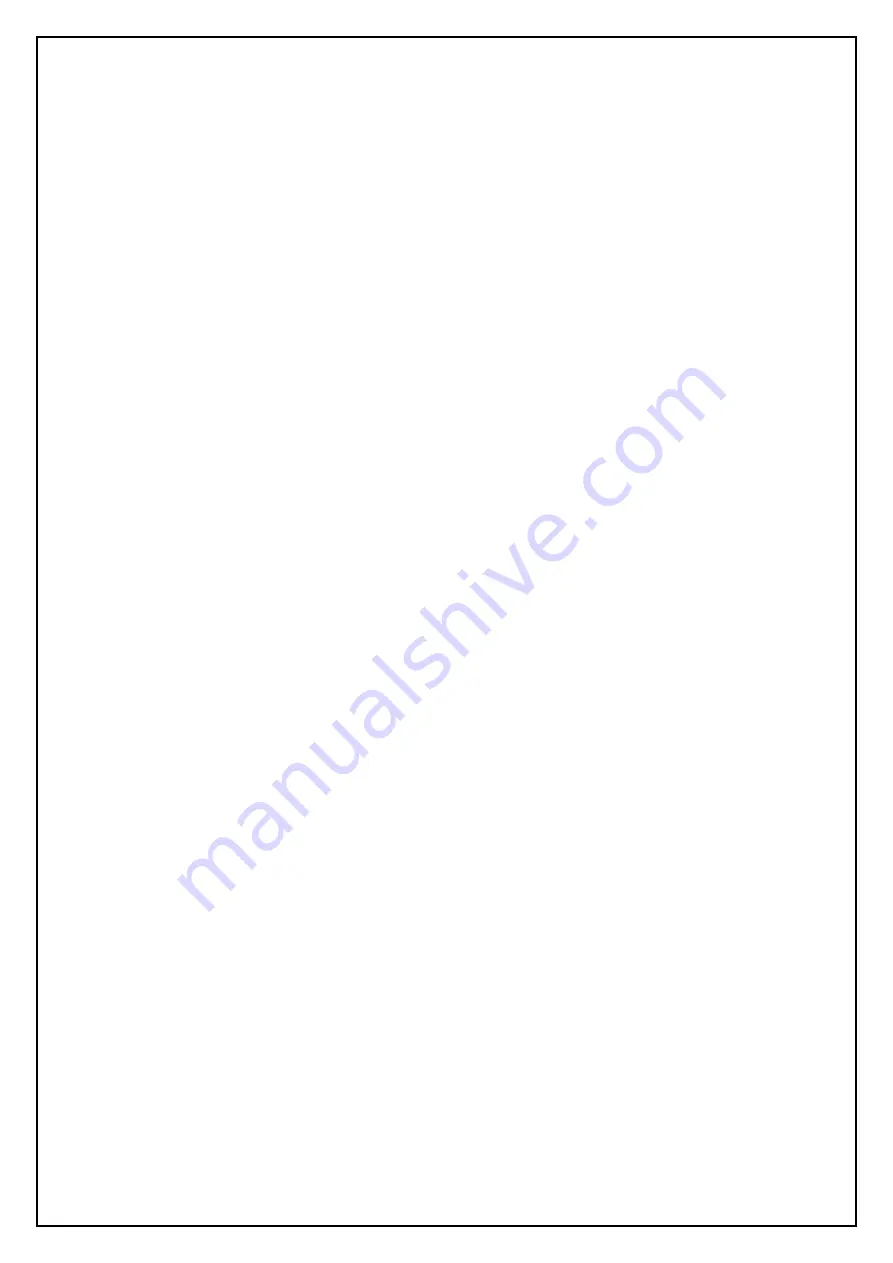
4) A deceleration circuit or shock absorber may be required.
When a driven object is operated at high speed or the load is heavy, a cylinder’s cushion will not be
sufficient to absorb the impact. Install a deceleration circuit to reduce the speed before cushioning, or
install an eternal shock absorber to relieve the impact.
In this case, the rigidity of the machinery should also be examined.
5) Consider a possible drop in circuit pressure due to a power outage, etc.
When a cylinder is used in a clamping mechanism, there is a danger of workpieces dropping if there is a
decrease in clamping force due to a drop in circuit pressure caused by a power outage, etc. Therefore,
safety equipment should be installed to prevent damage to machinery and human injury. Suspension
mechanisms and lifting devices also require consideration for drop prevention.
6) Consider a possible loss of power source.
Measures should be taken to protect against bodily injury and equipment damage in the event that there
is a loss of power to equipment conrtolled by pneumatics, electricity, or hydraulics.
7) Consider emergency stops.
Design so that human injury and/or damage to machinery and euqipment will not be caused when
machinery is stopped by a safety device under abnormal conditions, a power outage or a manual
emergency stop.
8) Consider the action when operation is restarted after an emergency stop or abnormal stop.
Design the machinery so that human injury or equipment damage will not occur upon restart of operation.
When the cylinder has to be reset at the starting position, install manual safely equipment.
9) Design the system not to allow external force over max. output of the cylinder.
Excessive external force may break the cylinder and lead to human injury and equipment damage.
10) Consider the force output by the cylinder to check the adequacy of mounting base in
rigidity.
If the mounting base is not rigid enough, the human injury and equipment damage may be caused.
11) Do not operate multiple cylinders simultaneously.
An air is compressive fluid and difficult to control in its speed. The change in supply pressure, load,
temperature, lubrication and deviation and change over the time of performance of the cylinder could
affect the speed. Therefore, the simultaneous operation of the cylinders are possible for short period by
adjusting with a speed controller, but these factors may easily break the simultaneous operation. If it
breaks, an excessive force is given to the piston rod due to difference in the positions. The force
becomes a lateral load and causes eccentric wear of the packing, wear of the bushing and damage
between the cylinder tube and piston. For this reason, the design to depend on the simultaneous
operation of the cylinders should be avoided. If it is compelled, use a rigid and high accurate guide to
compensate the force outputted by each cylinder.
12) About intermediate stop
In the case of a 3 position closed center valve, it is difficult to make a piston stop at the required position
as acurately and precisely as with hydraulic pressure, due to compressibility of air.
-
8
-
Furthermore, since valves and cylinders, etc. are not guaranteed for zero air leakage, it may not be
possible to hold a stopped position for an extended period of time. Please contact SMC in the case it is
necessary to hold stopped position for extended period.