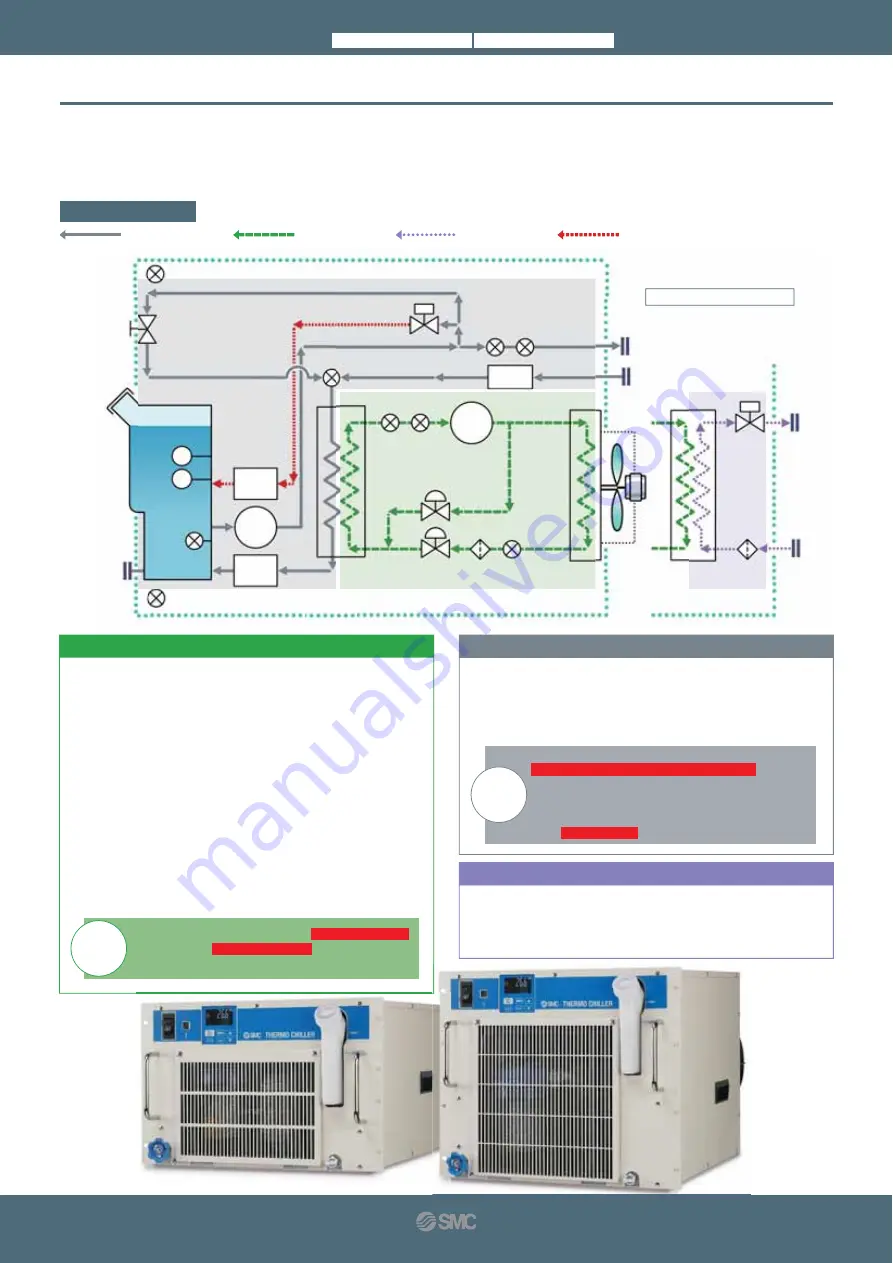
The precision temperature control method by expansion valve and temperature sensor, realized high temperature
stability of
±
0.1
°
C
.
¡
The compressor compresses the refrigerant gas, and discharges
the high temperature and high pressure refrigerant gas.
¡
In the case of air-cooled refrigeration, the high temperature and
high pressure refrigerant gas is cooled down by an air-cooled
condenser with the ventilation of the fan, and becomes a liquid. In
the case of water-cooled refrigeration, the refrigerant gas is cooled
by a water-cooled condenser with the facility water in the facility
water circuit, and becomes a liquid.
¡
The liquefied high pressure refrigerant gas expands and its
temperature lowers when it passes through expansion valve A and
vaporises by taking heat from the circulating fl uid in the evaporator.
¡
The vaporised refrigerant gas is sucked into the compressor and
compressed again.
¡
When heating the circulating fluid, the high pressure and high
temperature refrigerant gas is bypassed into the evaporator by
expansion valve B, to heat the circulating fl uid.
¡
The circulating fl uid discharged from the pump, is heated or cooled
by the user’s equipment and returns to the thermo-chiller.
¡
The circulating fluid is controlled to a set temperature by the
refrigeration circuit, to be discharged to the user’s equipment side
again by the thermo-chiller.
Refrigeration circuit
Circulating fl uid circuit
For water-cooled refrigeration HRR
첸
-W
¡
The water-regulating valve opens and closes to keep the refrigerant
gas pressure consistent. The facility water fl ow rate is controlled by
the water-regulating valve.
Facility water circuit
Circulating fluid circuit
Refrigeration circuit
Temperature sensor
Bypass valve
Tank
Level switch
Electric
conductivity
sensor
(Option)
Water-cooled
condenser
Drain port
Water leakage sensor
Particle
filter
Pump
DI filter
(Option)
Temperature sensor (For return)
Temperature
sensor
Temperature
sensor
(For discharge)
Solenoid valve for DI control
Pressure
sensor
Pressure
sensor
Pressure
sensor
Flow rate
sensor
Expansion
valve A
Expansion
valve B
Compressor
Strainer
Air-cooled
condenser
Circulating fluid outlet
Circulating fluid return port
Facility
water
outlet
Facility
water
inlet
Y-strainer for
facility water
HRR
첸
-A
HRR
첸
-W
Air-cooled Refrigeration
Water-cooled Refrigeration
Point
Point
Temperature stability:
±
0.1
°
C
Facility water circuit
Electric conductivity circuit
(For Option DM(Electric conductivity control))
Evaporator
Water-
regulating
valve
Fan
motor
Thermo-chiller/Rack Mount Type
Air-cooled Refrigeration
Water-cooled Refrigeration
HRR
Series
The combination of precise control of expansion valve A
for cooling, and expansion valve B for heating realised
high temperature stability.
Since the refrigeration circuit is controlled by the signal from
2 temperature sensors (for return and discharge)
, p r e c i s e
temperature control of the circulating fluid can be
performed. Therefore, there is no necessity of absorbing the
temperature difference in the circulating fl uid with a large
tank capacity, and realises high temperature stability even
with a
small-size tank
. Also, contributes to space-saving.
3
Summary of Contents for HRR Series
Page 30: ......