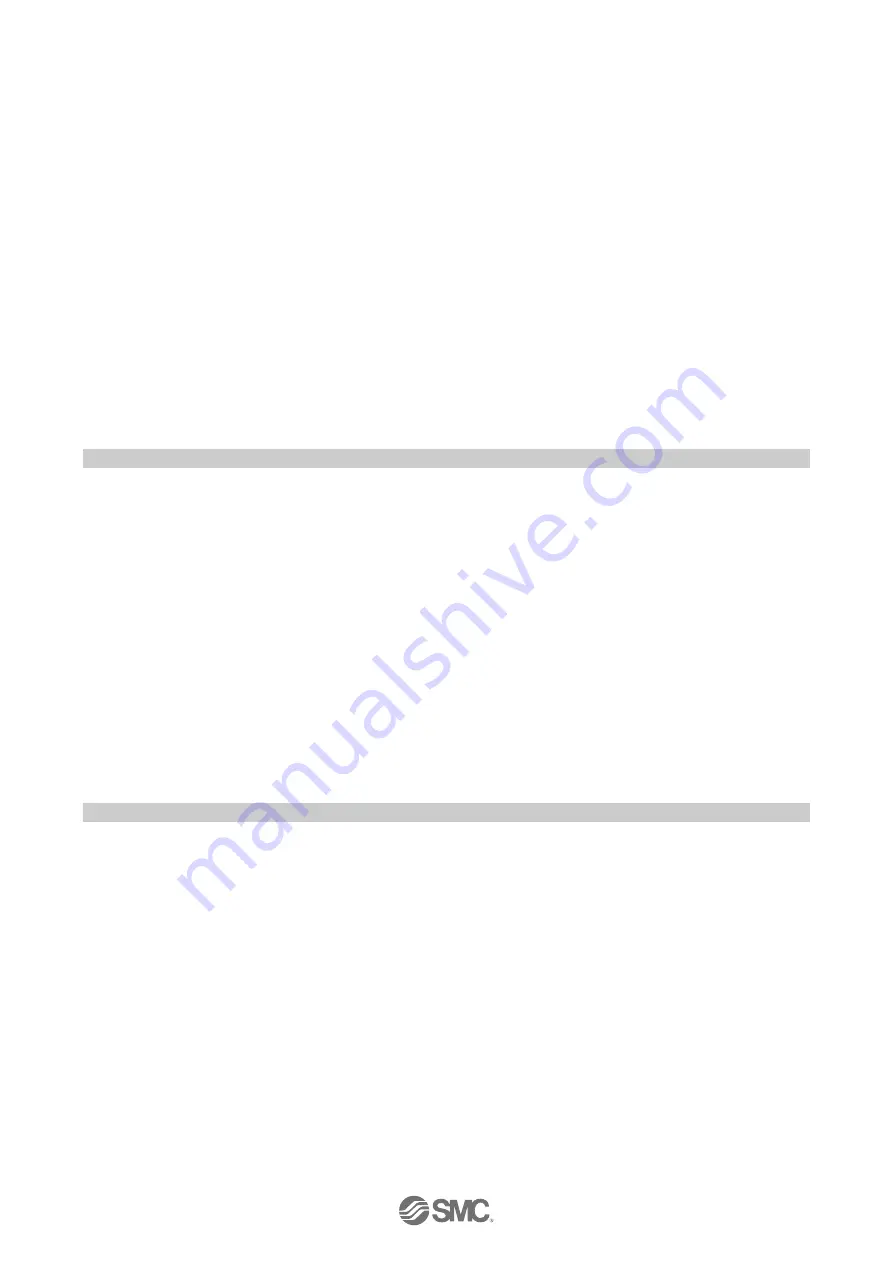
-6-
No.D-
※
S-OMU0002-A
(9) Install a rotation stopper to the actuator piston rod.
Use a guide or select an SMC product with a rotation stopping function.
The accuracy may decrease without a rotation stopper.
With some cylinders, the magnet may rotate even when the piston rod does not rotate. The magnet
inside some cylinders with guide may rotate. Contact SMC for details.
(10)
If the power is turned on while the magnet (target of detection) is out of the measurement
range, the analogue output indicates the lower limit value and switch output indicates logic
level low.
(Analogue current is 4[mA], analogue voltage is 0[V], switch output is ON for NPN output,
OFF for PNP output)
Analogue output and switch output will operate correctly by operating the cylinder at full stroke more
than once.
(11) Accuracy may decrease under the following operating conditions.
When warm up time is inadequate (10 to 15 minutes), play due to mechanical reason or floating joint
exists, or magnetic effect such as disturbance or magnetic substance (iron, screws) is present in the
operating environment.
It is recommended to use non-magnetic materials for surrounding parts.
Mounting and Adjustment
Caution
(1) Do not drop or apply impact.
Applying an excessive impact (more than 300 m/s
2
) may damage the product and cause malfunction.
(2) Observe the proper tightening torque for mounting.
If the screws are tightened in excessive of the specified torque range (0.2 to 0.4 Nm), it may damage the
cylinder/actuator, mounting screws, mounting brackets, and sensor etc.
Tightening below the specified tightening torque will allow the position sensor to move out of position.
(3) Do not carry an actuator by the position sensor lead wire.
This may cause a broken lead wires or damage to the auto switch internal elements.
(4) Use only the screws installed in the position sensor body for mounting the position sensor.
If other screws are used, the position sensor may be damaged.
(5) Check and adjust the actual product operation during installation.
The auto switch may not operate in the correct actuator mounting position due to the installation
environment.
Also check and adjust the auto switch operation when used in intermediate stroke positions, according to
the operating environment.
Wiring
Caution
(1) Check the insulation of the wiring.
Check that there is no faulty wiring insulation (short circuits, faulty ground connections, improper
insulation between terminals, etc.), as this may damage the auto switch due to over current.
(2) Do not route the auto switch wiring in the same place as power cables or high voltage cables.
Otherwise auto switch malfunction may result due to noise and inrush current.
(3) Avoid repeatedly bending or stretching the lead wire.
Broken lead wires will result if bending stresses or tensile forces are applied to the lead wires.
Stress and tensile forces applied to the connection between the lead wire and the product increases the
possibility of disconnection.
Secure the lead wire to reduce any movement in the area where the lead wire connects with the position
sensor.
(4) Be sure to shut off the user’s power supply before wiring.
Otherwise electric shock, malfunction or damage to the position sensor can result.
(5) Do not allow short-circuit of loads.
There is a risk of damage of position sensor.
(6) Wire correctly.
Incorrect wiring may cause malfunction or damage to the position sensor.