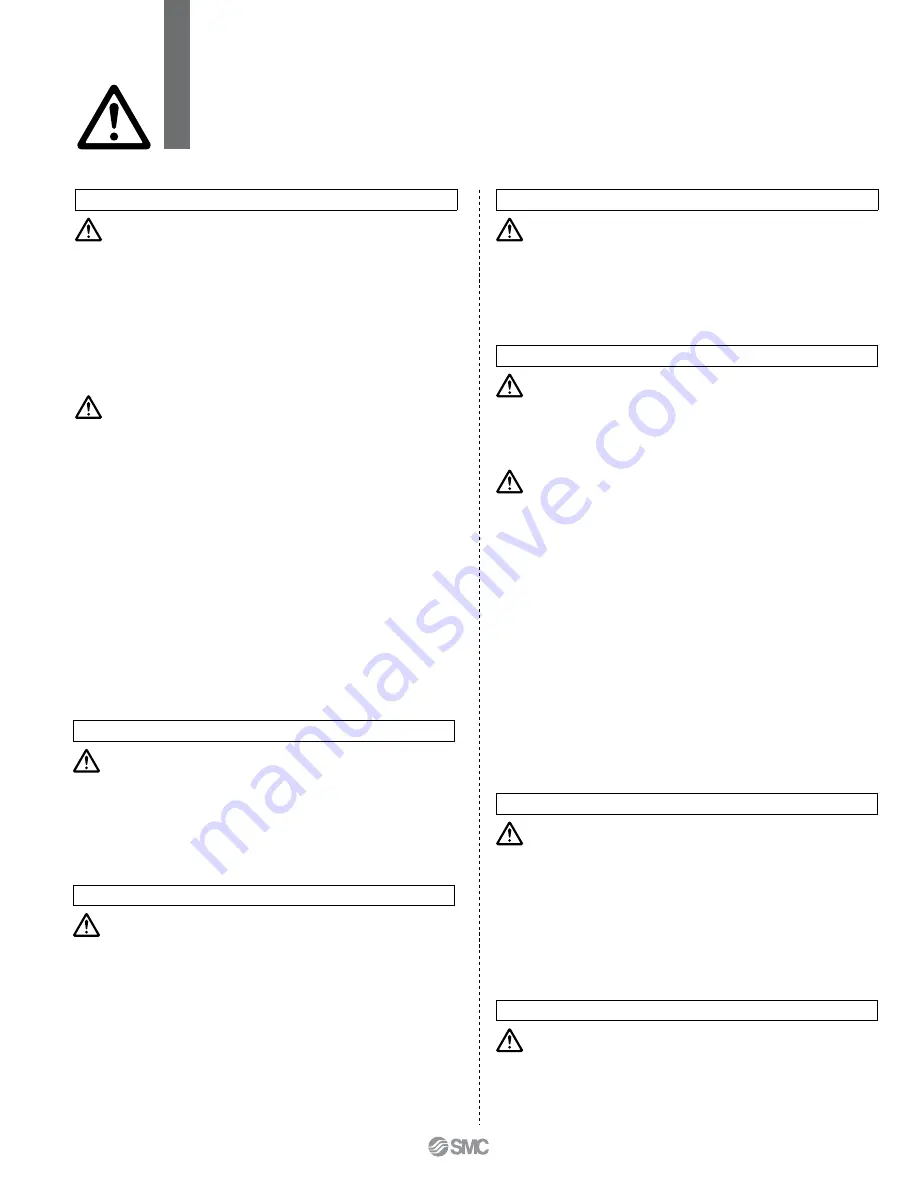
Design and Selection
Warning
Caution
Mounting and Adjustment
Caution
Wiring
Caution
Wiring
Caution
Operating Environment
Warning
Caution
Maintenance
Warning
Other
Caution
Trimmer Auto Switch
Specific Product Precautions
Be sure to read before handling. Refer to back cover for Safety Instructions. For Auto Switch Precautions, refer to “Handling
Precaution for SMC Products” and the Operation Manual on SMC website, http://www.smcworld.com
1. Check the specifications.
Read the specifications carefully and use this product appropriately. The
product may be damaged or malfunction if it is used outside the range of
specifications of current load, voltage, temperature or impact.
2. Cautions for use in an interlock circuit
When an auto switch is used for an interlock signal requiring high
reliability, devise a double interlock system to avoid trouble by providing a
mechanical protection function, or by also using another switch (sensor)
together with the trimmer auto switch. Also, perform periodic
maintenance and confirm proper operation.
1. Take precautions when multiple cylinders are used close
together.
When 2 or more cylinders with trimmer auto switches are used in close
proximity, maintain a minimum actuator interval of 40 mm or more.
(When the allowable interval is indicated for each cylinder series, use the
specified values.) Magnetic field interference may cause the trimmer auto
switches to malfunction.
2. Keep the wiring as short as possible.
Use a wire 3 m or shorter between the sensor and amplifier. If the sensor
cable length exceeds 3 m, the CE marking does not apply to the auto
switch. Although wire length of power supply/output cable should not
affect switch function, use a wire 100 m or shorter.
3. Take precautions for the internal voltage drop of the switch.
Auto switches may not operate properly depending on the connected
equipment.
4. Take measures for rotational stoppage of the piston rod.
Take measures for rotational stoppage of the piston rod when designing
by guide etc. Or use non-rotating type SMC products. The operation may
be unstable.
1. Do not drop or bump.
Do not drop, bump or apply excessive impacts (980 m/s2 or more for
sensor unit and 98 m/s2 or more for amplifier unit) while handling.
Although the trimmer auto switch body may not be damaged, the inside
of the trimmer auto switch could be damaged and cause a malfunction.
2. Refer to the Operation Manual for how to adjust/set.
1. Avoid repeatedly bending or stretching lead wires.
Broken lead wires will result from applying bending stress or stretching
forces to the lead wires.
2. Be sure to connect the connector for sensor to the amplifier
before power is applied.
3. Do not allow short circuit of loads.
Output is automatically stopped when the protection circuit is working, as
the output unit registers any excess current flow, if loads are short
circuited. Should this occur, shut off the power supply, remove the cause
of this excess current flow and switch on the power again. Take special
care to avoid reverse wiring between the power supply line (brown) and
the output line (black, white).
4. Avoid incorrect wiring.
If the connections are reversed (power supply line + and power supply
line –), the trimmer auto switches will be protected by a protection circuit.
However, if the power supply line (–) is connected to the black, white
wire, the trimmer auto switches will be damaged.
1. Never use in an atmosphere with explosive gases.
The structure of trimmer auto switches is not designed to prevent
explosion. Never use in an atmosphere with an explosive gas since this
may cause a serious explosion.
1. Do not use in an area where a magnetic field is generated.
Trimmer auto switches will malfunction or magnets inside actuators will
become demagnetized.
2. Do not use in an environment where the trimmer auto
switch will be continually exposed to water.
Although the sensor units of trimmer auto switches satisfy the IEC
standard IP67 structure, do not use trimmer auto switches in applications
where continually exposed to water splash or spray. Poor insulation or
swelling of the potting resin inside trimmer auto switches may cause a
malfunction. (Amplifier unit D-RNK and RPK: IP40)
3. Do not use in an environment with oil or chemicals.
Please consult with SMC if trimmer auto switches will be used in an
environment with coolant, cleaning solvent, various oils or chemicals. If
trimmer auto switches are used under these conditions for even a short
time, they may be adversely affected by improper insulation, malfunction
due to swelling of the potting resin, or hardening of the lead wires.
4. Take measures against freezing when operating at 41 ° F
(5°C ) or less.
1. Perform the following maintenance periodically in order to
prevent possible danger due to unexpected trimmer auto
switch malfunction.
1) Secure and tighten trimmer auto switch mounting screws.
If screws become loose or the mounting position is dislocated,
retighten them after readjusting the mounting position.
2) Confirm that there is no damage to lead wires.
To prevent faulty insulation, replace trimmer auto switches or repair
lead wires, etc., if damage is discovered.
1. Please consult with SMC concerning water resistance, elasticity of
lead wires, and usage at welding sites, etc.
8
Summary of Contents for D-M9K/D-7K/D-RK Series
Page 11: ......