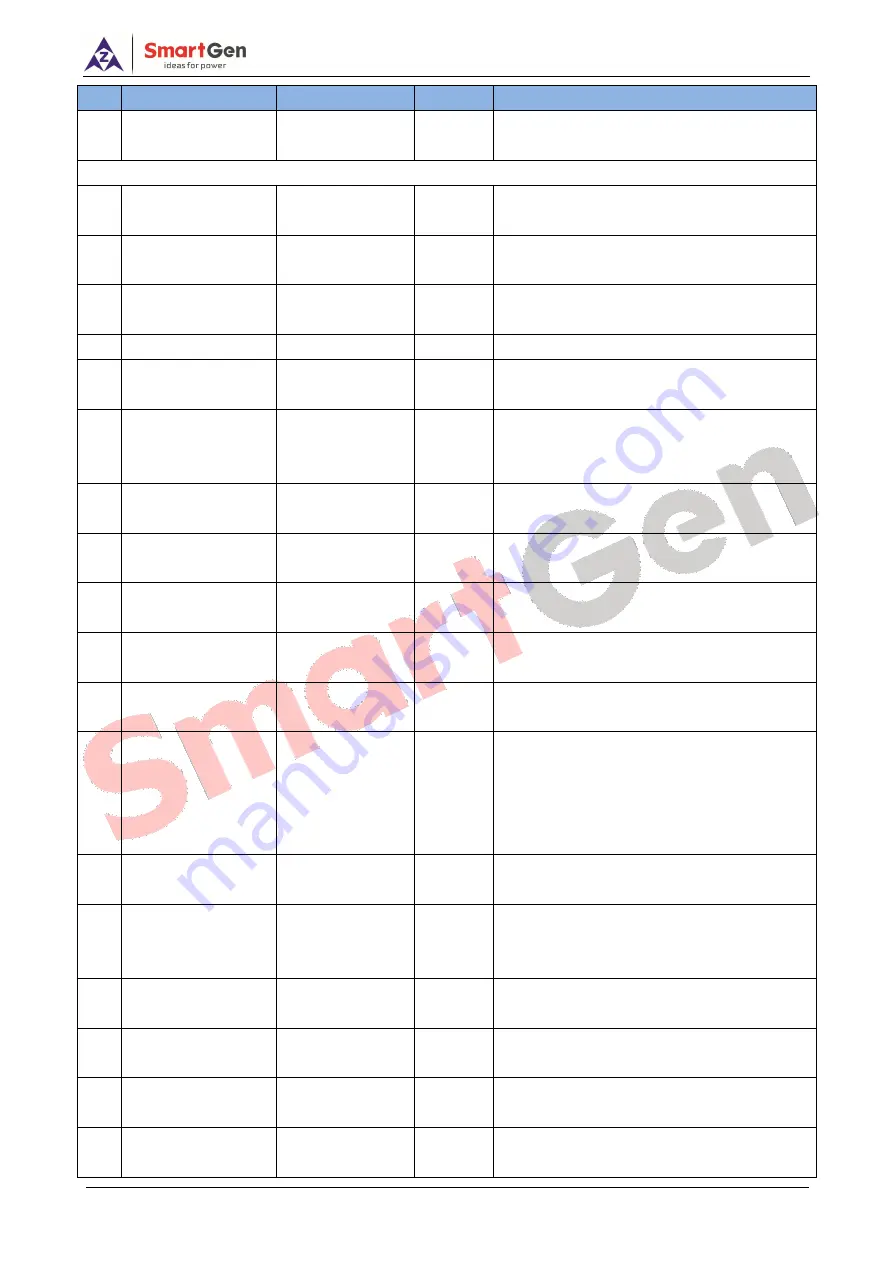
HGM9520N Genset Paralleled Controller User Manual Page 58 of 111
No.
Items
Parameters
Defaults
Description
5: Mains Close/Open Button (C)
6: Gen Close/Open Button (O)
Timer Setting
1.
Start Delay
(0~3600)s
5
Time from mains abnormal or remote start
signal is active to genset is starting.
2.
Stop Delay
(0~3600)s
30
Time from mains normal or remote start
signal is inactive to genset is stopping.
3.
Preheat Delay
(0~3600)s
0
Time for pre-powering the heat plug before
starter is powered up.
4.
Cranking Time
(3~60)s
8
Time for starter power on each time.
5.
Crank Rest Time
(3~60)s
10
The waiting time before second power up
when engine start fails.
6.
Safety On Delay
(0~3600)s
10
Alarms for low oil pressure, high
temperature, under speed, under frequency
/voltage, charge fail are inactive.
7.
Start Idle Time
(0~3600)s
10
Running time for genset idling speed when
the genset is starting.
8.
Warming Up Time
(0~3600)s
30
Warming up time between genset switch on
and high speed running.
9.
Cooling Time
(0~3600)s
60
Radiating time before genset stop, after it
unloads.
10.
Stop Idle Time
(0~3600)s
10
Running time for genset idling speed when
the genset is stopping.
11.
ETS Solenoid Hold
(0~3600)s
20
Time
for
the
stop
electromagnet
energization as the genset is stopping.
12.
Fail to Stop Delay
(0~3600)s
0
Time after “idle delay” is over before the
complete stop when “ETS Solenoid Hold” is
set “0”; time after “ETS Solenoid Hold” delay
is over before the complete stop when it is
set other than “0”.
13.
After Stop Time
(0~3600)s
0
Time between a complete stop and
standby.
14.
Gas Engine Timers (0~1)
0
0: Disable 1: Enable
When gas engine timer is enabled, fuel oil
output is used for controlling gas valve.
15.
Choke On Time
(0~60)s
0
Output time for gas thickening after the
engine starts.
16.
Gas On Delay
(0~60)s
0
After this period, gas valve control outputs
after the engine starts.
17.
Ignition Off Delay
(0~60)s
0
After this period, gas ignition control stops
outputting after the gas valve is closed.
18.
Smart Pre-heat
(0~1)
0
0: Disable 1: Enable
When it is enabled, the controller will stop