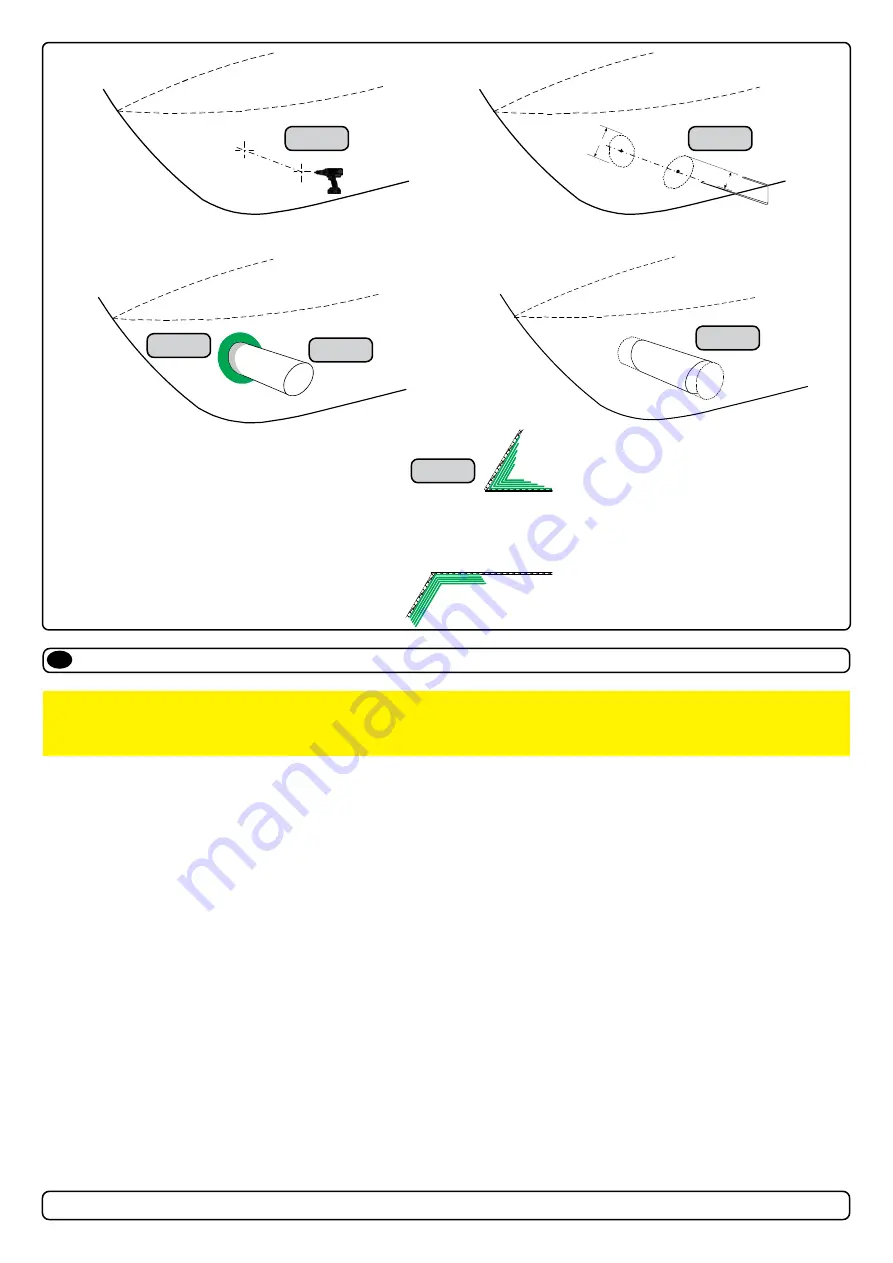
11
5611
12
2021
-
SE20 & SE25 & SE30 & SE40
MG_0005
R
D
1
2
3
4
6
5
8 x layers of fiberglass
and resin
8 x layers of fiberglass
and resin
MG_0006
R = D x 0,1
R = D x 0,1
D x
0,1
-0,1
5
D x
0,1
-0,
15
D
Layers of
fiberglass
and resin
Layers of
fiberglass
and resin
*Fiberglass
Hull
*Steel/
Aluminium
Hull
Hull
Hull
Hull
Tunnel
Tunnel
Tunnel
Welding
Layers of
fiberglass
and resin
Additional Layers of
fiberglass and resin
Additional Layers of
fiberglass and resin
Hull
1
3
4
2
Tunnel Installation
EN
1. Find the position in the boat considering the information earlier in this manual and the applicable measurements for the thruster model you are
installing. Mark the centre of the tunnel on both sides of the hull. Drill a hole horizontally at these marks.
2. Mark the circle for the tunnel opening (outside diameter of the tunnel) and cut the hole.
3. Grind off the gel coat to the “real fi breglass” area 12cm around the hole on both inside and outside the hull to cast the tunnel to the hull
(Fig. 3)
.
4. Insert the tunnel and mark its shape to fi t the hull.
(NB: if you are installing with a deflector/ spoiler, leave a part of the tunnel in the front and
underside of the tunnel that will cover the back face.)
5. Cut the tunnel ends to the desired shape and lightly sand its surface. Clean the area with acetone or similar where you are going to apply
fi breglass.
(NB: Do not cast or add fi breglass to the area were the thruster will be placed.)
6. Cast the tunnel to the inside of the hull, use at least eight layers of 300g fi breglass and resin, preferably alternating mat and rowing types of
fi breglass. To round the tunnel ends to a 10% radius make further layers inside to preserve the desired hull thickness.
(NB: Ensure gaps between the tunnel and the hull are completely fi lled with resin/ fi breglass. In areas where you can not access to make
layers of resin/ fi breglass, a resin/ fi breglass mixture must be used in that area.)
MC_0003
IMPORTANT
We recommend that a professional does the fi breglass, steel or aluminium fi tting of the tunnel. These instructions are only general
instructions and do not explain in any way the details of fi breglass work. Problems caused by faulty installation of the tunnel, are the
installers full responsibility.
MG_0002
R = 0,1 x D (10%)
D
1
2
3
Angled tunnel ends for
steel/ aluminium hulls
Cavitation
MG_0003
High water force
while underway
High water force
while underway
from wave contact
1
2
3
4
Tunnel Ends
EN
MC_0003
Rounded tunnel ends will maximise thrust and minimise noise and cavitation.
For best performance round the tunnel connection to the hull-side as much as possible. The minimum rounding has a radius of 10% of the diameter of
the tunnel.
Signifi cant advantages of a rounded tunnel over a sharp tunnel to hull connections are:
1. A rounded tunnel end will prevent the creation of turbulence/ cavitation created from a sharp tunnel end when water passes by the tunnel.
- The turbulence/ cavitation will block the outer area of the tunnel and thereby reduces the effective tunnel diameter and thrust.
- Turbulence/ cavitation on the propeller will lessen the thrusters performance and create excess noise.
2. For steel/ aluminium hulls angled tunnel ends also offer similar performance as a rounded connection.
3. A rounded tunnel end makes the thruster draw water from along the hull-side, creating a vacuum that will suck the boat sideways and thereby give
additional thrust.
- With a sharp tunnel end, the thruster will be unable to take water from along the hull-side, and you will not gain the desired vacuum and
additional thrust. This “free” extra thrust in optimal installations be 30 - 40% of the total thrust.
(NB: A Side-power thruster propeller does not produce cavitation at working speed. Therefore, any cavitation and cavitation noise in the tunnel will
be caused during improper tunnel installation.)