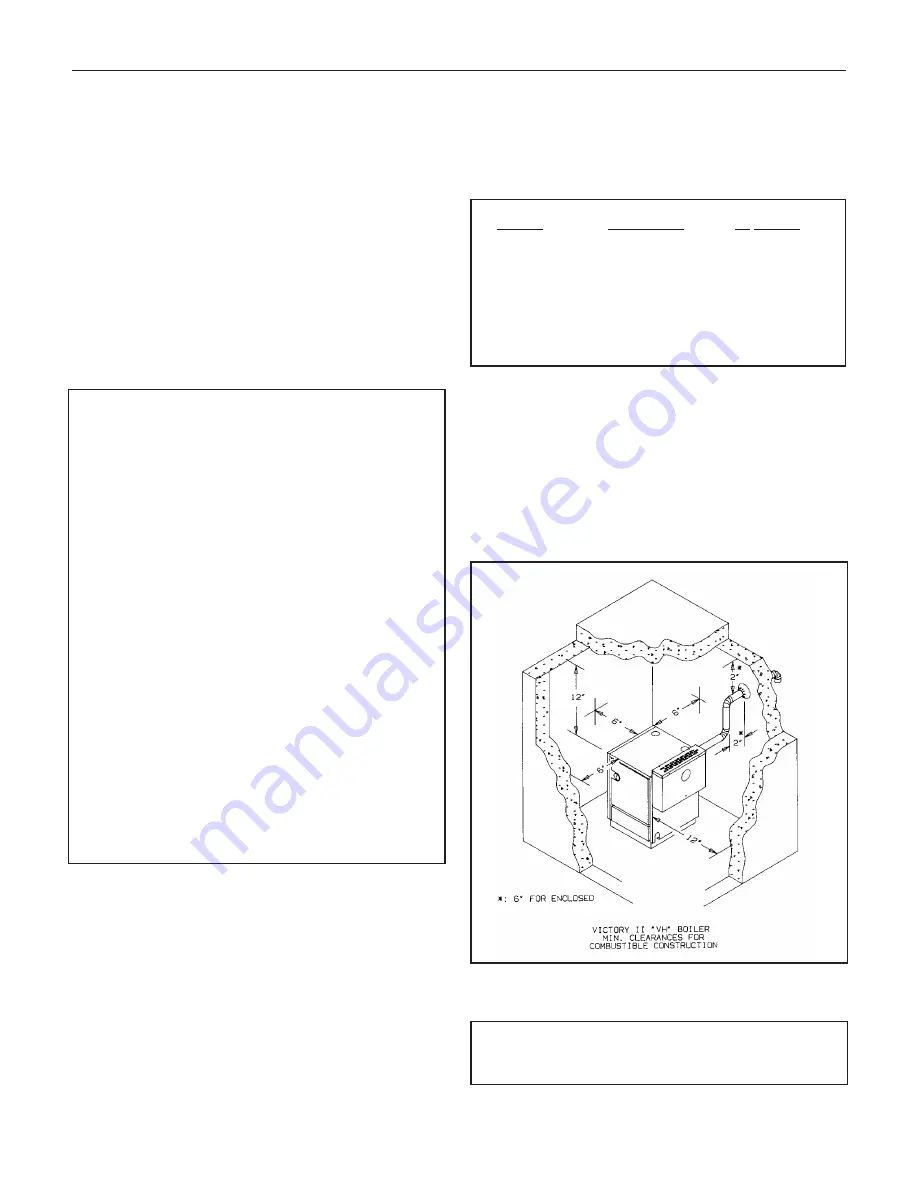
V
ICTORY
II
INSTALLATION REQUIREMENTS
The installation must conform to the requirements of the
authority having jurisdiction or, in the absence of such
requirements, to the National Fuel Gas Code , ANSI Z223.1-
latest edition.
This installation must also conform to the additional require-
ments in this Slant/Fin Instruction Book.
NATURAL GAS-FIRED BOILER LOCATION
Provide a level, solid foundation for the boiler. Location
should be as near as possible to chimney or outside wall so
that the flue pipe from boiler is shor t and direct. (See Appen-
dix A for vent terminal location restrictions.) The location
should also be such that the gas ignition system components
are protected from water (dripping, spraying, rain, etc.) during
appliance operation and service (circulator replacement, con-
densate trap, control replacement, etc.).
WARNING
LIQUEFIED PETROLEUM (L.P.) PROPANE GAS-FIRED
BOILER LOCATION
REQUIRES SPECIAL ATTENTION
Liquefied Petroleum (L.P.) propane gas is
heavier than air.
Therefore, propane boilers, piping, valves must NOT be
installed in locations where propane leaking from def ective
equipment and piping will "pool" in a basement or other
space below the leak.
A spark or flame from the boiler or other source ma y ignite
the accumulated propane gas causing an explosion or fire.
Provide a level, solid foundation for the boiler. Location
should be as near the chimney as possible so that the flue
pipe from boiler to chimney is short and direct.
The UNIFORM MECHANICAL CODE may be in effect in
your geographic area.
The following precautions are cited by the 1994 UNIFORM
MECHANICAL CODE, section 304.6:
"LPG Appliances.
Liquefied petroleum gas-burning
appliances shall not be installed in a pit, basement or
similar location where heavier-than-air-gas might collect.
Appliances so fueled shall not be installed in an abo ve-
grade under-floor space or basement unless such loca-
tion is provided with an approved means for removal of
unburned gas."
Consult Chapter 5 of the 1994 UNIFORM MECHANICAL
CODE for design criteria of the "approved" means for
removal of unburned gas.
BOILER FOUNDATION
A. Provide a solid, level foundation, capable of supporting
the weight of the boiler filled with w ater, and extending at
least 2" past the jacket on all sides. See dimensions of
boilers, page 2.
B. For installation on non-combustible floors only*.
C. If boiler is to be located o ver buried conduit containing
electric wires or telephone cables, consult local codes or
the National Board of Fire Underwr iters for specific
requirements.
* Installation on combustible flooring allowed only with proper Com-
bustible Floor Kit. Kit part number is printed on boiler rating plate.
In no case may the boiler be installed on car peting.
MINIMUM CLEARANCES FROM COMBUSTIBLE
CONSTRUCTIONS
A. Minimum clearances to the exterior surfaces of the boiler
shall be as follows:
MINIMUM ALCOVE AND CLOSET CLEARANCE
For Combustible
Recommended
Surface
Construction
for Service
Front
6"
18"
Rear
6"
18"
Left Side
6"
18"
Right Side
12"
24"
Top
12"
12"
Flue Connector:
Enclosed —
6"
6"
Unenclosed —
2"
6"
B. Provide accessibility clearance of 24" on sides requir ing
servicing and 18" on sides used for passage.
C. All minimum clearances shown above must be met. This
may result in increased values of some minimum clear-
ances in order to maintain the minim um clearances of
others.
D. Clearance from hot water pipes shall be 1 inch**.
** At points where hot water pipes emerge from a floor, wall or ceiling,
the clearance at the opening through the finished floor boards or w all
or ceiling boards may be not less than 1/2 inch. Each such opening
shall be covered with a plate of uncombustible material.
SAFETY
KEEP THE BOILER AREA CLEAR AND FREE FR OM
COMBUSTIBLE MATERIALS, GASOLINE AND OTHER
FLAMMABLE VAPORS AND LIQUIDS.
3
Figure 3.
Summary of Contents for victory II VH series
Page 8: ...VICTORY 8 Figure 7...
Page 9: ...VICTORY Figure 8 9...
Page 12: ...VICTORY 12 Figure 9...
Page 13: ...VICTORY Figure 10 13...
Page 16: ...VICTORY 16...
Page 17: ...VICTORY Figure 14 Figure 15 Piping Arrangement 17...