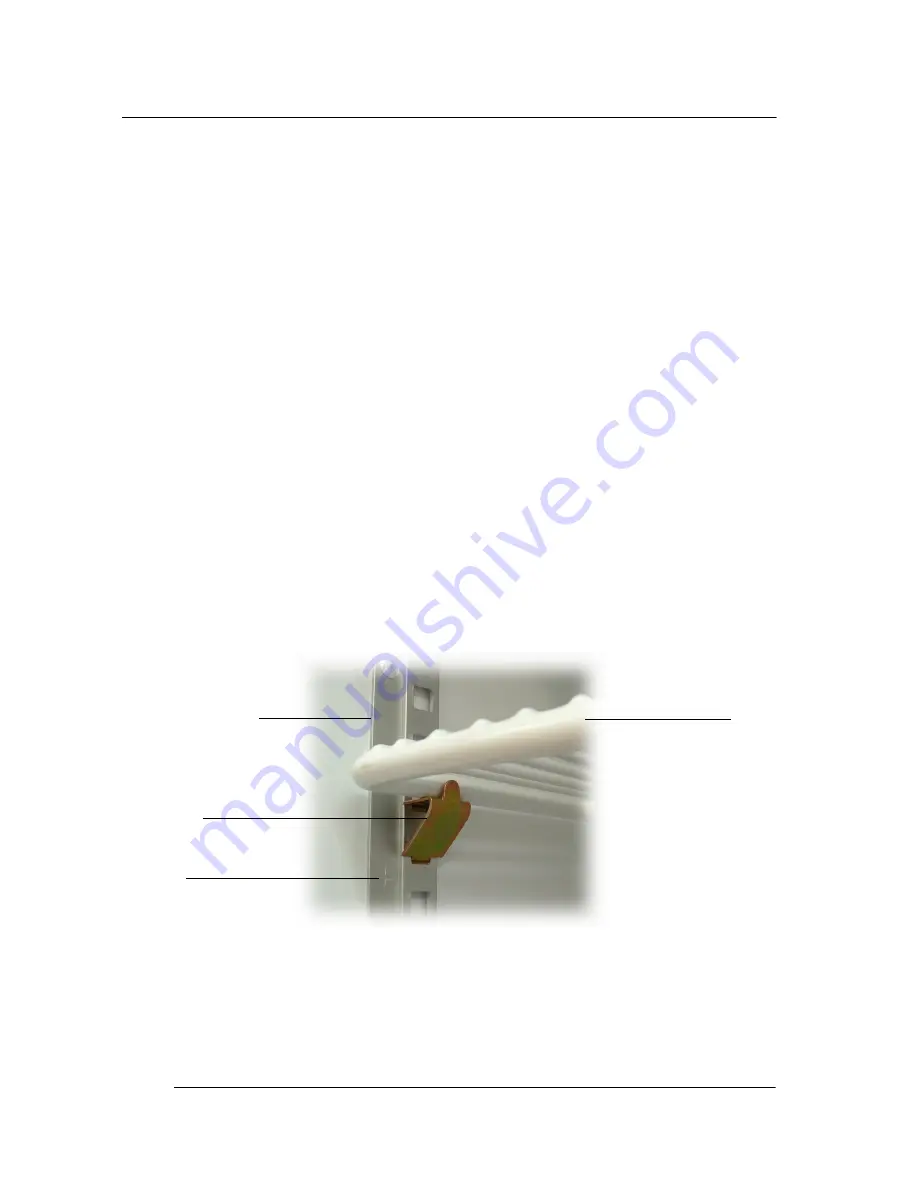
10
SK650-2
SKOPE Gen2: Single Door Chiller
2.3 Loading
The shelves may be positioned at different heights to suit various
products. Each shelf is held in place with four shelf clips. Always
ensure that the shelf clips are securely engaged in each of the four
shelf support strips. The support strips are marked with a ‘+’ for easy
location of the shelf clips (see Figure 1 below).
When loading the shelves with product:
• ensure to allow air space around all packages etc, for even
cooling and efficient operation.
• leave an airspace of at least 75mm (3") above packages etc. on
the top shelf.
• do not allow products to overhang the front of the shelf as this
could prevent the door from shutting or cause glass breakage.
OPERATION
2
Figure 1: Shelf Clip
Shelf Support Strip
Shelf Clip
‘+’ Mark
Shelf
Summary of Contents for SK650-2
Page 2: ......
Page 47: ...47 SK650 2 SKOPE Gen2 Single Door Chiller Notes SERVICE INSTRUCTIONS 4 ...
Page 48: ...48 SK650 2 SKOPE Gen2 Single Door Chiller 5 1 Model SK650 2 Type V60BA WIRING DIAGRAMS 5 ...
Page 50: ...50 SK650 2 SKOPE Gen2 Single Door Chiller 5 2 Model SK650 2 Type V60BB WIRING DIAGRAM 5 ...