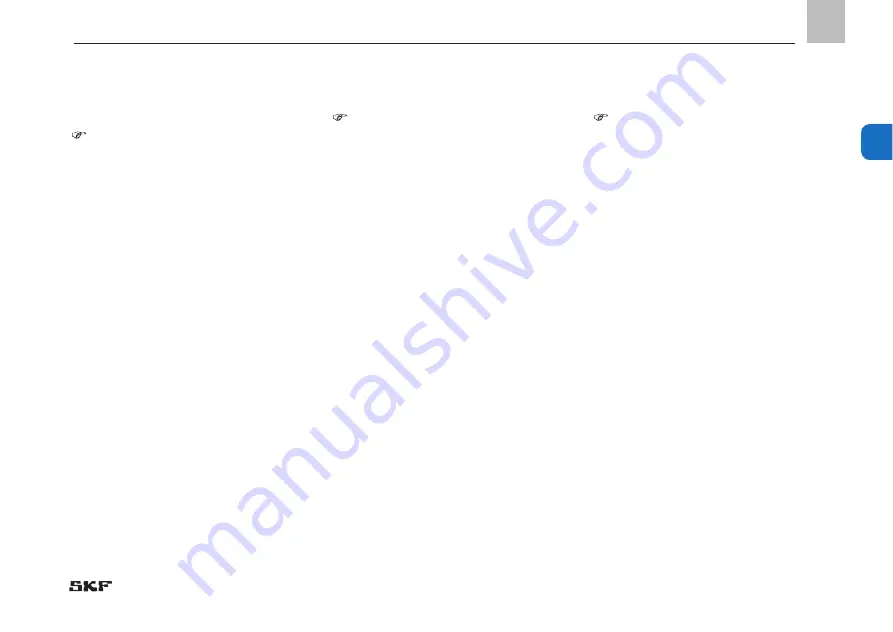
3
- 29 -
951-180-087-EN
Version 01
EN
3rd Overview, functional description
3.1
Pulse generator operation
See Figure 3
The lubricant flows from the inlet, through
duct
KR
, and into outlet chamber
D4
. Piston
K1
moves to the left. The control bolt with
balls
E1
locks piston
K2
. The lubricant in
outlet chamber
D1
is pressed through the
right-hand annular groove of
K2
to the
outlet. When piston
K1
reaches the end po-
sition on the left, the locking of piston
K2
is
terminated.
See Figure 4
The lubricant flows from the inlet, through
duct
KML
, and into outlet chamber
D2
. Pis-
ton
K2
moves to the right. The control bolt
with balls
E1
locks piston
K1
. The lubricant
in outlet chamber
D3
is pressed through the
right-hand annular groove of piston
K1
to
the outlet. When piston
K2
reaches the end
position on the right, the locking of piston
K1
is terminated. The lubricant flows from
the inlet, through duct
KL
, and into outlet
chamber
D1
. Piston
K1
moves to the right.
The control bolt with balls
E1
locks piston
K2
. The lubricant in outlet chamber
D4
is pressed through the left-hand annular
groove of
K2
to the outlet. When piston
K1
reaches the end position on the right, the
locking of piston
K2
is terminated.
See Figure 3 - K1 in right position
The lubricant flows from the inlet, through
duct
KMR
, and into outlet chamber
D3
.
Piston
K2
moves to the left. The control bolt
with balls
E1
locks piston
K1
. The lubricant
in outlet chamber
D2
is pressed through the
left-hand annular groove of
K1
to the outlet.
The sequence described above is repeated
as long as lubricant flows.
With each procedure as described above,
reed contact
S1
in the switch part is closed
and opened once by the ring magnet affixed
to piston
K1
.
The switching pulses are
generated at a rate proportional to the volu-
metric flow. They are fed to the connected
pulse evaluator and monitored by the built-
in timer.
A fault signal is issued if the switching period
is longer than the set monitoring time.