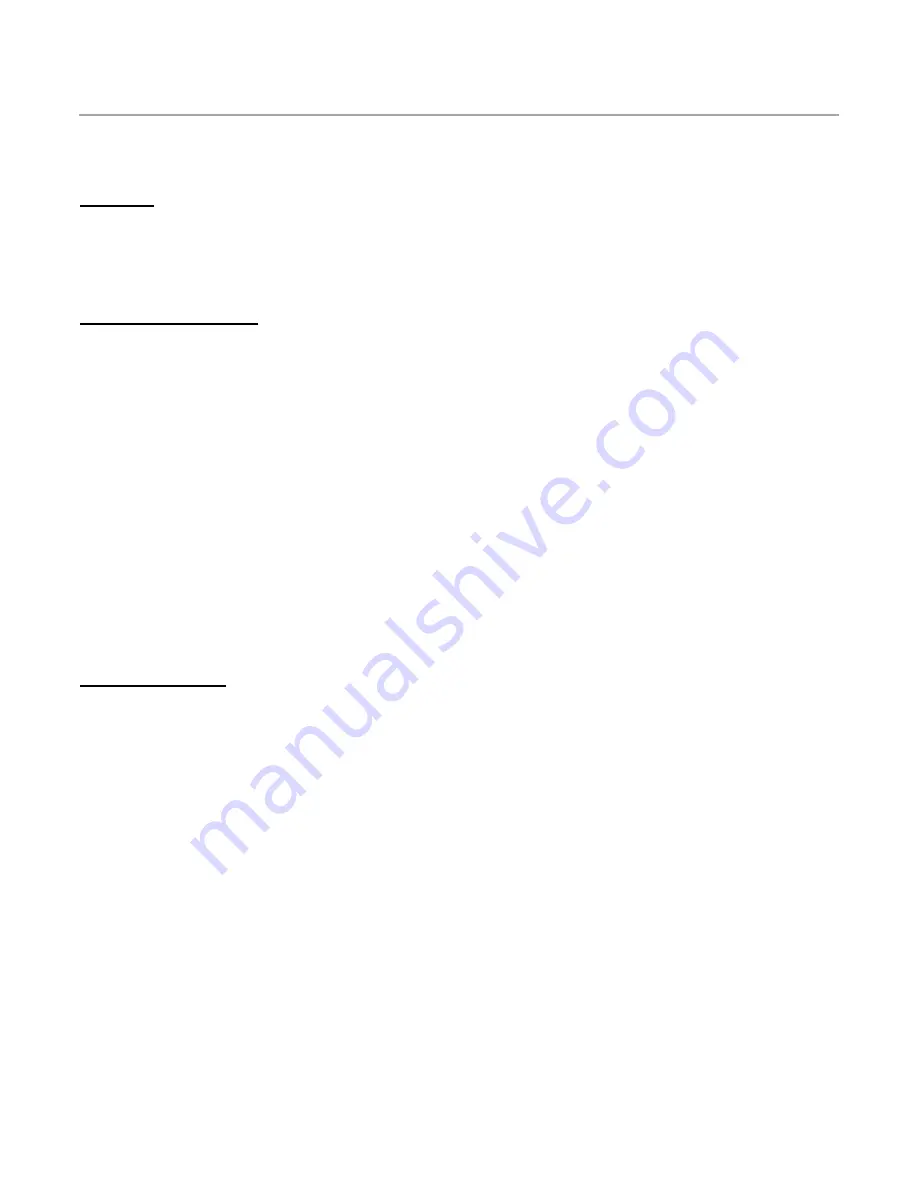
Safety Information
6
BEFORE OPERATING THIS UNIT, YOU MUST PAY SPECIAL ATTENTION TO
THE SAFETY NOTICES GIVEN BELOW.
ELECTRICAL
1. Electrical repairs must only be carried out by a qualified or suitably trained person.
2. We strongly advise that access to the interior of the unit be restricted to trained personnel only and that operating
the unit with the covers removed be avoided.
3. The unit must be correctly installed (See INSTALLATION )
SAFETY RULES FOR DRILLING
1. Caution. This drilling machine is intended for use only with drill bits the use of other accessories may be hazardous
make sure they are suitable and safe for use with your drill. Ensure that at all times the work area is well lit.
2. Correct drilling speeds. Factors, which determine the best speed to use in any drilling machine operation, are: Kind
of material being worked, size of the hole and type of drill or other cutter, and quality of cut desired. The smaller the
drill size, the greater the required R.P.M. In soft materials, the speed should be higher than for hard materials.
3. When drilling metal use clamps to hold the work. To avoid injury, the work should never be held with the bare hands.
4. The work must be clamped firmly while drilling. Any tilting, twisting or shifting results not only in a rough hole but also
increases the hazard, which could result in injury or drill breakage. For flat work lay the piece on a wooden base
and clamp it firmly down against the table to prevent it from turning If the piece is of irregular shape and cannot be
laid flat on the table, it should be securely blocked and clamped.
5. Remove key from chuck after adjustment.
6. Secure the base of the drill to the work bench or work table before using the drilling machine if the work is heavy or
large and likely to cause the drill to tip over, use additional supports as appropriate under and around the work.
8. Use only the chuck key provided by the manufacturer or a duplicate of it.
9. Always switch off the machine and isolate from the mains supply before opening the belt cover and changing
position of V belt or carrying out any adjustment or maintenance.
GENERAL SAFETY RULES
1. Keep all guards in place and in full working order.
2. Keep work area clean and tidy. Cluttered areas and benches invite accidents.
3. Do not use in damp or wet conditions, or expose the pillar drill to rain.
4. Keep children away. All visitors should be kept at a safe distance from the working area.
5. Do not force the tool or attachment to do a job for which it was not designed.
6. Use the right tool. It will do the job better and safer at the rate for which it was designed.
7. Wear proper clothing. No loose clothing, gloves, neckties, rings bracelets, or other jewellery as these may be caught
in moving parts. Non-slip footwear is also recommended. Wear protective hair covering to contain long hair.
8. Always use safety glasses.
9. Do not over reach. Keep proper footing and balance at all times.
10. Maintain tools. Keep tools sharp and clean for best and safest performance. Follow instructions for lubricating and
changing accessories.
11. Disconnect from the mains supply before servicing and when changing accessories such as drill bits.
12. Never stand on the drill press as serious injury could occur if the machine is tipped or if the cutting tool is
unintentionally contacted.
13. Check for damaged parts. Before using the drill press, a guard or other part that is damaged should be carefully
checked to determine that it will operate properly and perform its intended function, check for alignment of moving
parts, binding of moving parts, breakage of parts, mountings, or any other condition that may affect the machines
operation. A guard or any other part that is damaged should be immediately replaced.
14. Never leave drill running unattended. Turn the power off. Do not leave tool until the machine has came to a
complete stop.