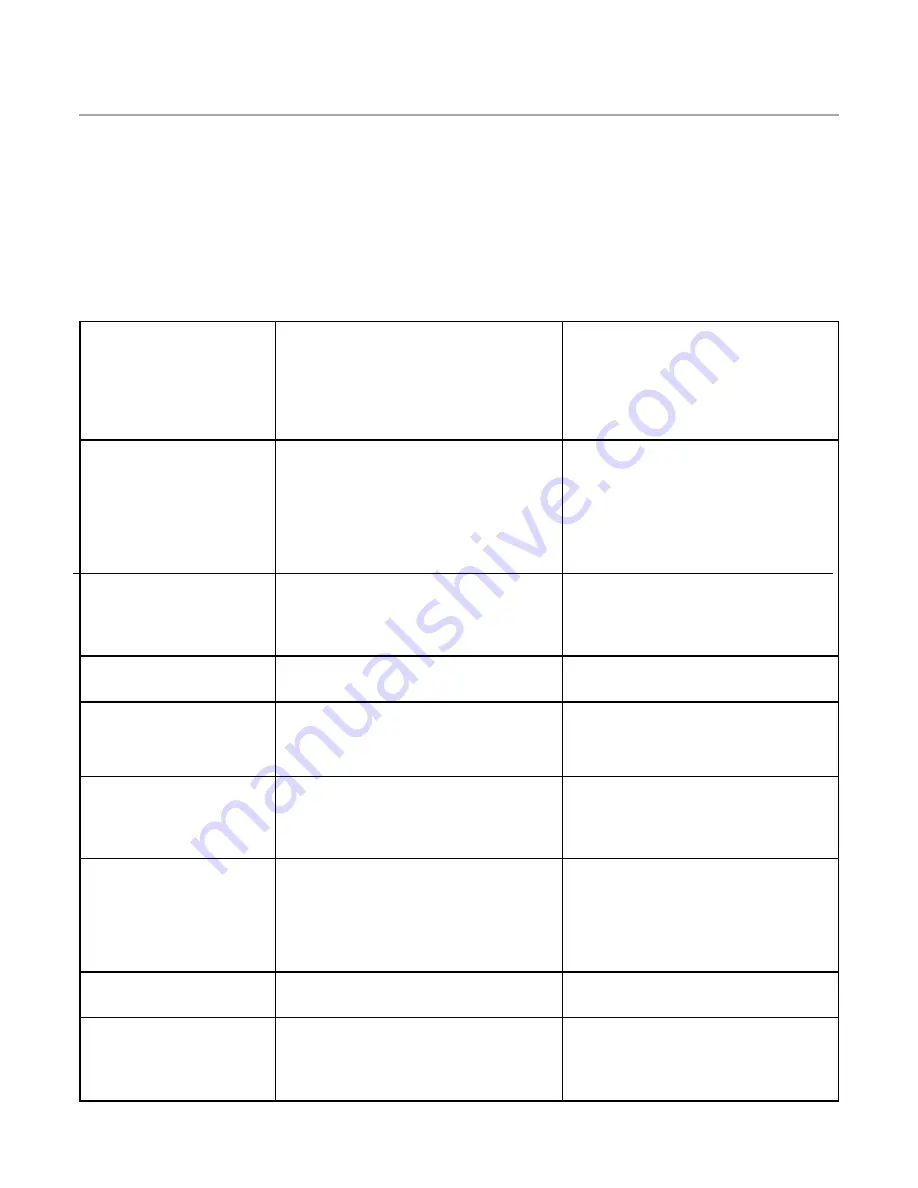
Maintenance
Lubrication
All of the BALL BEARINGS are packed with grease at the factory. They require no further lubrication.
Periodically lubricate the table elevation mechanism, the SPLINES (grooves) in the spindle, and the RACK
(teeth of the quill)
Mantenance
Frequently blow out any dust that may accumulate inside the motor.
A coat of automotive type paste wax applied to the table and column will help to keep th surfaces clean.
11
Noisy Operation
Incorrect belt tension
Adjust tension
Dry spindle
Lubricate spindle
Loose spindle
Checking tightness of retaining nut
on pulley, and tighten if necessary
Loose motor on pulley
Tighten setscrews in pulleys
Drill bit burns
Incorrect speed
Change speed
Chips not coming out of hole
Retract dril bit frequently to clear chips
Dull drill bit
Resharpen drill bit
Feeding too slow
Faster the speed
Not lubricated
Lubricate drill bit
Drill leads off...
Hard grain in wood or lengths of
Resharpen drill bit correctly
hole not round
cutting lips and/or angles not equal
Bent drill bit
Replace drill bit
Wood splinters on underside
No back up material under workpiece
Use back up material
Workpiece turn loose
Workpiece pinching dril bit or
SUpport workpiece or clamp it
from hand
excessive feed pressure
Improper belt tension
Adjust tension
Drill bit binds in workpiece
Workpiece pinching drill bit
Support workpiece or clamp it
or excessive feed pressure
Improper belt tension
Adjust tension
Excessive drill bit runout
Bent drill bit
Use a straight dril bit
or wobble
Worn spindle bearings
Replace bearings
Drill bit not properly installed in chuck
Install drill bit properly
Chuck not properly installed
Install chuck properly
Quill returns too slow or fast
Spring has improper tension
Adjust spring tension
Chuck will not stay attached Dirty, grease or oil on the tapered
Using a household detergent, clean the
to spindle, it falls off when
inside surface of chuck or on the
tapered surface of the chuck and
trying to install it
spindles tapered surface
spindle to remave all dirt, grease and
oil