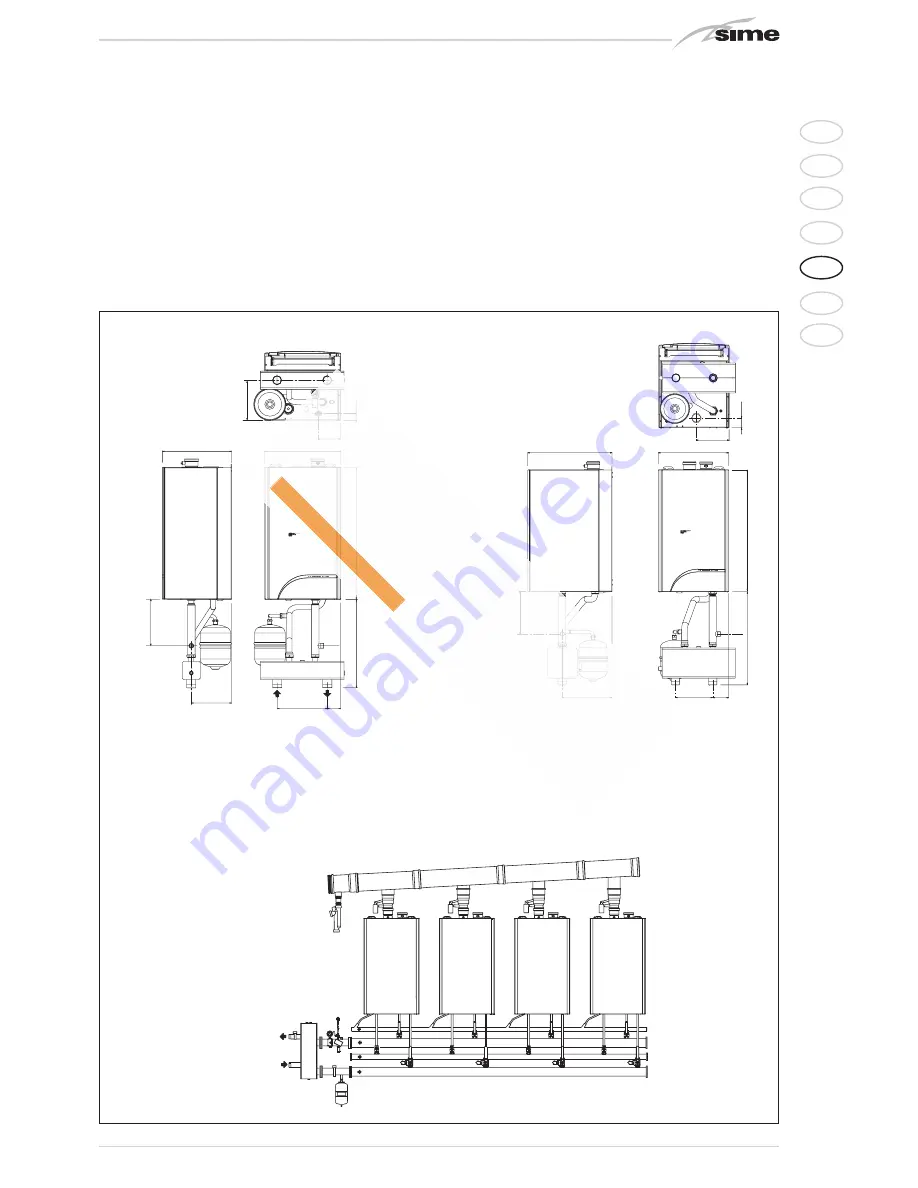
119
IT
ES
FR
BE
GB
RUS
RO
The boiler must be installed in a fixed loca-
tion and only by specialized and qualified
firms in compliance with all instructions
contained in this manual.
Furthermore, the installation must be in
accordance with current standards and
regulations.
2.1
BOILER ROOM
The boilers can be installed in boiler rooms
whose size and requirements meet current
regulations.
Furthermore, vents, with surface areas at
least 3.000 sq. cm or 5.000 sq. cm for
gas with density over 0.8, must be installed
in the outer walls for room ventilation.
2.2
INSTALLATION
For single installations, it is also possible to
order an optional compensator kit (code
8101520 for the version
“60 BFR”
and cod.
8101523 for the version
“100 BFR”
).
The kit can be fitted on accumulation boilers
with a capacity equivalent to or above 80
liters. For installation for single or sequen-
ce/cascade operations, refer to the exam-
ple in fig. 3.
With control unit code 8096301, supplied
by Sime upon request, a maximum of four
boilers can be controlled. The control unit
kit is supplied wit h assembl y and use
instructions.
2
INSTALLATION
45
146
R3
500
865
582
88
330
R
M
M2
M2
265
305
455
265
Fig. 3
WARNING:
- In both single and sequence/cascade installation, the heating system must be equipped with a
hydraulic separator and safety components.
- When replacing one or more boilers in existing plants, it is advisable to install a heat exchanger
to separate the boiler circuit from the secondary circuits. See the pressure curve for the boiler
supply shown in figure 14.
M
S3
R
G
Single installation
with kit optional
code 8101520
for "60 BFR"
Installation in sequence/cascade
R C.H.
return
M C.H.
flow
G Gas
connection
S3
Condensation outlet
355
30
1
M2
M2
265
115
M
R
865
663
70
R3
500
235
600
Single installation
with kit optional
code 8101523
for “100 BFR”
M
C.H. flow
R
C.H. return
M2 Tank flow
R3
Tank return