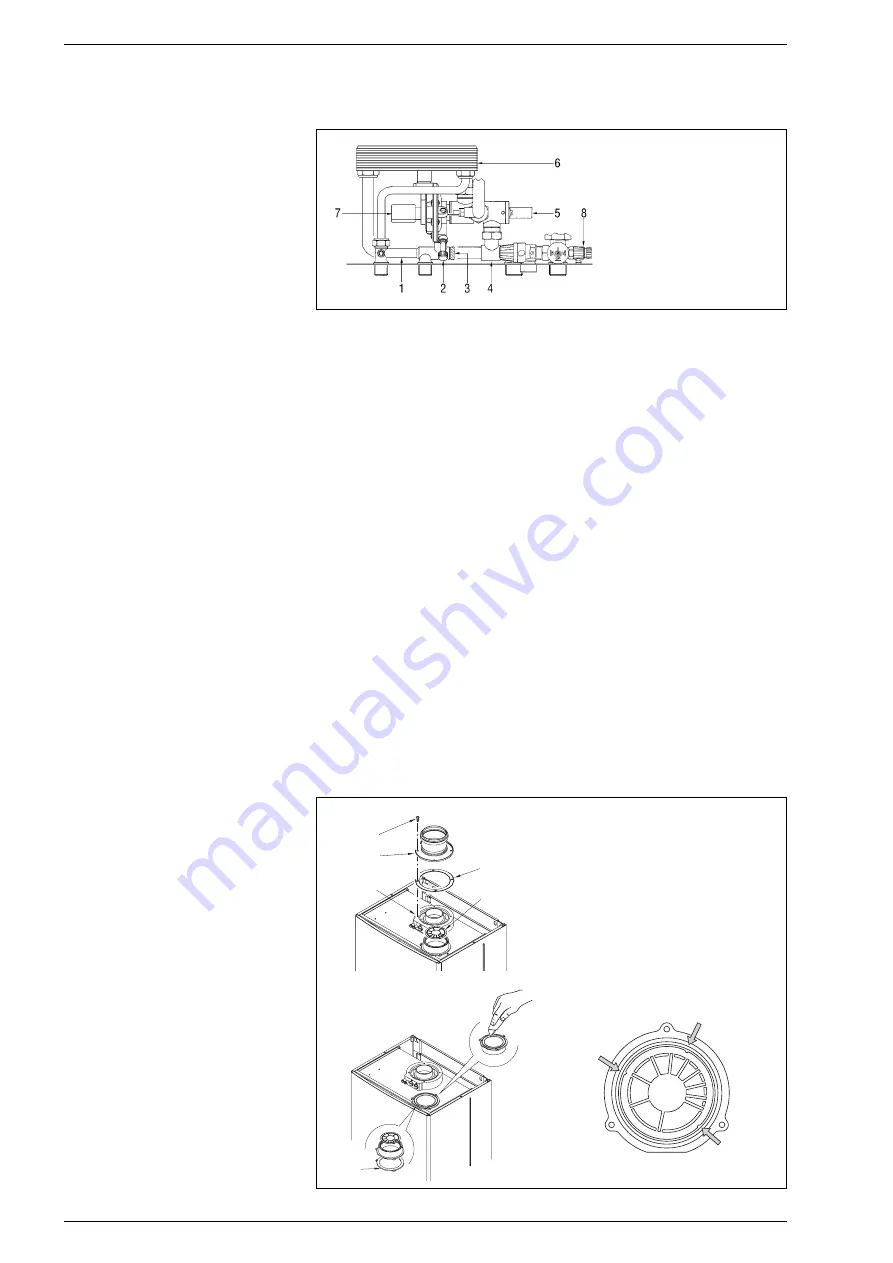
The gas pipes, from the gas meter to the
boiler, must be sized taking into account
both flow capacity in volumes (consump-
tion) in m
3
/h and the density of the gas in
question.
The section of the pipes of the plant must
be such as to guarantee a sufficient gas
supply to cover the maximum need, limiting
pressure loss between the meter and any
appliance requiring more than:
– 1.0 mbar for second family gases (natural
gas)
– 2.0 mbar for third-family gases (butane or
propane).
An adhesive plate is attached inside the
mantle, on which the technical data iden-
tifying the type of gas for which the boiler is
adapted are given.
2.2.1
Gas pipe filter
The gas valve has a filter fitted at the input;
however, this will not block all the impurities
contained in the gas and in the supply pipes.
To avoid faulty functioning of the valve, or in
certain cases even a loss of its safety func-
tion, a suitable filter should be fitted on the
gas pipe.
2.4
TO FILL THE PLANT
The boiler and the plant are filled in two dif-
ferent ways:
A) Using the loading lever of the pressure
control valve (2 fig. 6). Loading pressure,
when the plant is cold, must be between
1-1.2 bar
as indicated on the water
gauge.
B) By means of the load button on the remo-
te control panel. When plant pressure
descends below the intervention thre-
shold of 0.6 bar, the low water level ano-
maly icon “” will appear on the remote
control panel display, together with the
message
“ALL 02”
. Fill the plant by pres-
sing on the remote control button
(RIEMP)
for a maximum cumulative time
of five minutes. During loading the icon
will flash. When pressure has returned
to normal (1 bar) the icon will disappear,
loading is deactivated and the timer that
records the cumulative time is reset. If an
overall time of five minutes is insufficient
to recover plant pressure, loading will be
deactivated and the timer can be reset
only after switching off the electricity sup-
ply to the boiler.
2.5
TO EMPTY THE PLANT
This operation is carried out by means of
the discharge (8 fig. 6).
Before this operation, switch off the boiler.
2.6
CHIMNEYS AND FLUES
The chimney or flue for the release of com-
bustion products into the atmosphere
must comply with the prescriptions of Stan-
dard UNI-CIG 7129/92.
It must in particular comply with the speci-
fic prescriptions of Standards UNI-CIG
10640 for boilers with natural draught in
collective chimneys (type B) and UNI 10641
for boilers with forced draught (type C).
2.6.1
Ducting
of existing chimneys
For the re-use or the ducting of existing chim-
neys, ducts declared by the manufacturer of
the same as suitable for the purpose must
be used, and they must be installed and used
according to the indications of constructor
itself and the prescriptions of Standard UNI
10845.
2.7
FUMES DISCHARGE AND AIR
ASPIRATION
OPEN.zip
built-in boilers must be provided
with suitable fumes discharge and air aspira-
tion ducts, according to the type of installa-
tion. The ducts are an essential part of the
boiler, but are supplied separately to allow for
greater plant flexibility.
2.7.1
Forced discharge (Type B22-52)
During installation, the provisions pursuant
to Standards and certain practical advice
should be followed:
– Insulate the discharge duct and provide
for a condensation collection system at
the base of the vertical duct.
– If the duct must pass through flammable
walls, insulate the stretch of the fumes
discharge duct concerned with a fiber-
glass covering 30 mm thick, density 50
kg/m
3
.
A special kit - cod. 8089904 - is available for
this type of discharge. Fit the discharge flan-
ge supplied in the kit as indicated in fig. 7.
To use the air intake vent provided, the fol-
lowing operations must be carried out (fig.
7):
57
Fig. 6
KEY
1
Sanitary water input/
output manifold
2
Plant filling
3
Sanitary water filter
4
Manifold by-pass
5
Thermo actuator
6
Sanitary water exchanger
7
Micro switches
8
Boiler discharge
a
b
5
Fig. 7
1
2
3
4
6
KEY
1 Foam washer ø 125/95
2 Fixing screws
3 Fumes discharge flange
4 Aspiration diaphragm
5 Air intake washer
6 Manifold with intakes
IMPORTANT: The three seats on
the diaphragm allow for the air
vent to be fitted in only one posi-
tion (with the sector numbers
facing inwards).
Summary of Contents for Open.zip 25 BF TS
Page 1: ...GB Open zip 25 30 BF TS IT ES CERTIFICAZIONE DEL SISTEMA DI QUALITA AZIENDALE...
Page 28: ...26...
Page 52: ...50...
Page 54: ...52...
Page 79: ......