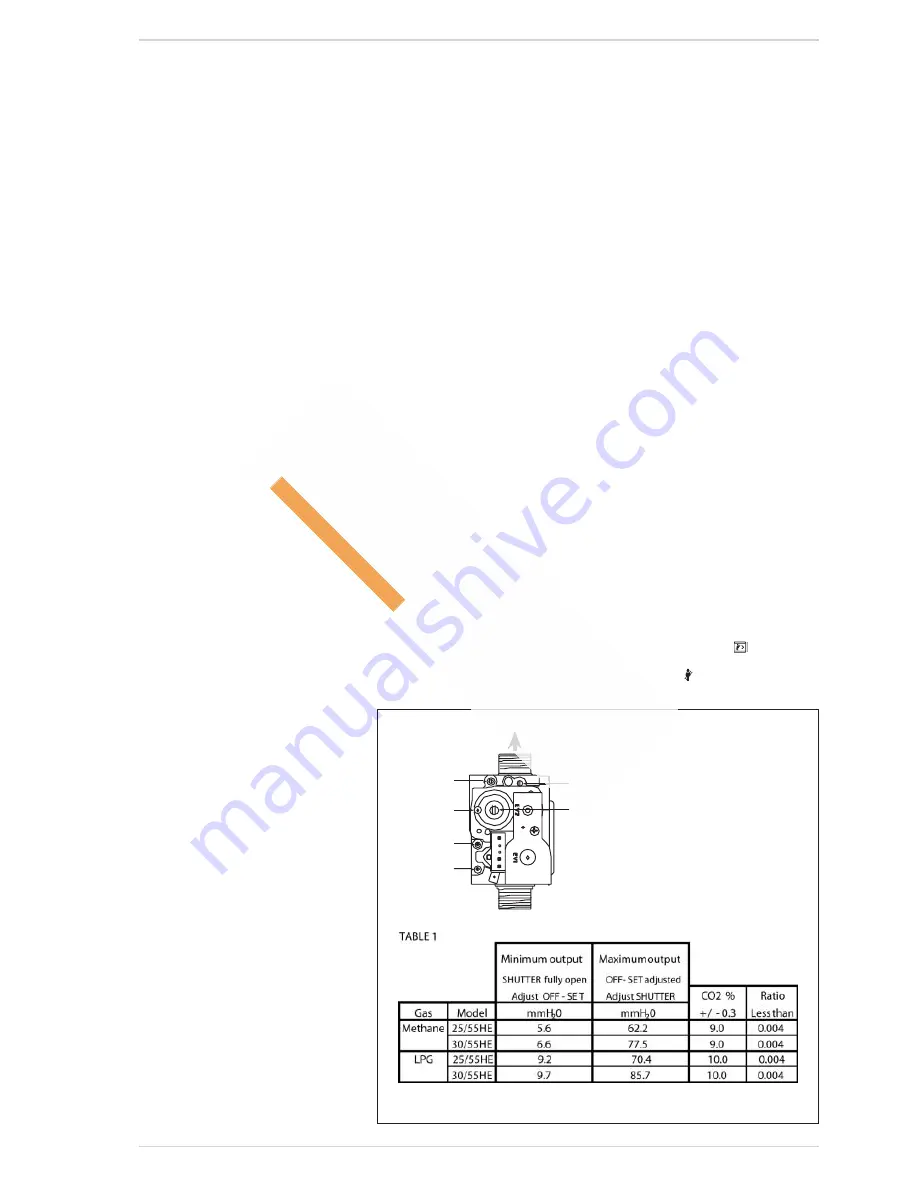
40
6
REPLACEMENT OF PARTS
6.1
EXPANSION VESSEL
– Turn off power supply
– Remove boiler cover, see 4.4.
– Isolate flow and return valves
– Drain boiler using fitted drain vent
– Disconnect expansion pipe
– Loosen top fixing screw and remove
lower expansion vessel locking nut.
– Remove vessel and transfer the fixing
bracket to the new vessel.
– Check new vessel for correct pressu-
re 1- 1.25 bar
– Refit in reverse order.
6.2
IGNITION ELECTRODE
– Turn off power supply
– Remove boiler cover see 4.4
– Remove sealed chamber cover
– Disconnect electrode from ignition
transformer
– Pull lead through grommet
– Remove electrode fixing screw
– Carefully remove electrode from bur-
ner
– Replace in reverse order.
6.3
IONISATION ELECTRODE
– Turn off power supply
– Remove boiler cover see 4.4
– Remove sealed chamber cover
– Disconnect electrode
– Remove electrode fixing screw
– Carefully remove electrode from bur-
ner
– Replace in reverse order
6.4
MAIN BURNER
– Turn off power supply
– Isolate gas supply
– Remove boiler cover
– Remove sealed chamber cover
– Disconnect gas connection at injector
– Disconnect air sensing tube
– Disconnect two plugs to fan
– Remove ignition electrode 6.3
– Disconnect ionisation electrode
– Remove 6 x 10mm nuts securing bur-
ner to heat exchanger
– Carefully lift out burner assembly
– Refit in reverse order
– Test for gas tightness.
6.5
FAN ASSEMBLY
– Remove burner assembly as descri-
bed in 6.4
– Remove 2 x 8mm bolts and loosen 2 x
8mm securing fan to burner assembly
– Remove restrictor plate and fit to
new fan
– Refit in reverse order
– Recommission boiler
– Test for gas soundness.
6.6
MAIN HEAT EXCHANGER
– Turn off power supply
– Isolate gas supply
– Isolate flow and return valves
– Drain boiler using drain vent
– Remove burner assembly as described
in 6.4
– Remove flue connection
– Disconnect flue sensor
– Disconnect limit stat
– Remove condensate drain connections
– Disconnect flow and return connections
– Remove two fixing brackets
– Lift out heat exchanger
– Refit in reverse order
– Recommission boiler
– Test for gas tightness.
6.7
FLUE SENSOR
– Turn off power supply
– Remove cover
– Remove sealed chamber cover
– Disconnect flue sensor
– Unscrew sensor
– Replace in reverse order.
6.8
100° SAFETY STAT
– Turn off power supply
– Remove cover
– Remove sealed chamber cover
– Disconnect 100° safety stat
– Remove fixing screws
– Refit in reverse order.
6.9
HEATING THERMISTOR
(SM SENSOR)
– Turn off power supply
– Remove cover
– Remove sealed chamber cover.
– Isolate flow and return valves
– Drain boiler using drain vent
– Disconnect thermistor
– Unscrew thermistor (catch any water
lost)
– Refit in reverse.
6.10
D.H.W. THERMISTOR
(SB) SENSOR
– Turn off power supply
– Remove cover see 4.4
– Isolate cold water supply valve
– Drain the cylinder
– Disconnect thermistor
– Unscrew thermistor (catch any water
lost)
– Refit in reverse.
6.11
GAS VALVE
– Turn off power supply
– Isolate gas supply
– Remove boiler cover see 4.4
– Disconnect wiring from gas valve
– Disconnect sensing tube
– Remove gas valve
– Refit in reverse order ensuring seals
are replaced as required
– Setting the gas valve procedure:
1. Open the downstream test point
(4 fig. 25) and connect a digital
manometer set on the mmH20
s c a l e . E n s u r e t h e m e t e r i s
zeroed.
2. Fully open the SHUTTER (5 fig.
25) -turn anti clockwise
3. Press and hold the
button for 10
s e c o n d s t o e n t e r “ c h i m n e y
sweep”
will appear flashing on
KEY
1
Upstream pressure intake
2
Intermediate pressure intake
3
Air signal inlet (VENT)
4
Downstream pressure intake
5
Capacity step
6
OFF-SET
1
2
3
4
5
6
Fig. 25