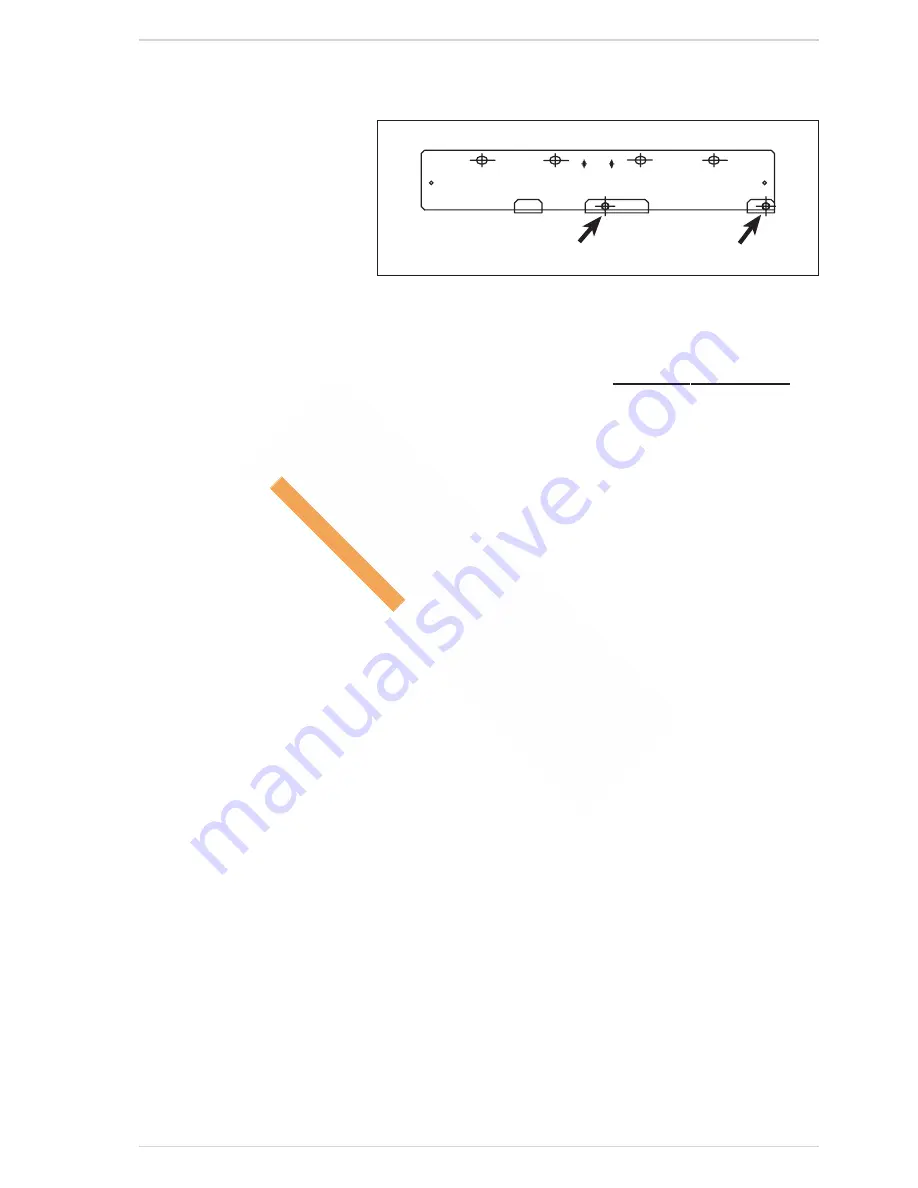
10
Where no specific instructions are given,
the installation should be in accordance
with the relevant recommendations in the
current editions of the following British
St andards and Codes of Practice: BS
5440-1, BS 5440-2, BS 5449, BS 5482
(propane installations), BS 5546, BS 6700,
BS 6798, BS 6891, Institute of Gas Engi-
neer document IGE/UP-7, BS 7074 (expan-
sion vessel), and to other relevant British
Standards or code of Practice as neces-
sary. It is a
Statutory Requirement
that
the installation conforms to the appropria-
te Building Regulations either The Building
Regulations, The Building Regulations (Sco-
tland), Building Regulations (Northern Ire-
land), the Water Fitting Regulations or
Water Byelaws in Scotland, and the cur-
rent I.E.E Wiring Regulations. When hand-
ling, due consideration should be given to
the appliance weight. If the appliance is not
to be installed immediately it should be sto-
red in a clean dry place.
2.1
VENTILATION REQUIREMENTS
Detailled recommendations for air supply
are given in BS5440:2. The following notes
are for general guidance:
– It is not necessary to have a purpose
provided air vent in the room or com-
par tment in which the appliance is
installed. However, suitable clearances
for maintenance and servicing should
be provided, see fig. 1.
2.1.1
Anti-freeze function
The boilers are equipped with anti-freeze
function which activates the pump and the
burner when the temperature of the water
contained inside the appliance drops to
below 6°C. The anti-freeze function is ensu-
red, however, only if:
- the boiler is correctly connected to the
gas and electricity supply circuits;
- the boiler is turned on;
- the boiler ignition is not locked out;
- the essential components of the boiler
are all in working order.
In these conditions the boiler is protected
against frost down to an environmental
temperature of -5°C.
ATTENTION: In the case of installation in a
place where the temperature drops below
0°C, the connection pipes must be protected.
2.2
BOILER SUPPORT BRACKET
Ensure that the wall on which the boiler is to
be mounted is capable of supporting the
weight of the boiler when filled (123 kg -
25/55 and 125 kg - 30/55)
- Position the bracket ensuring that the boi-
ler is fitted with sufficient clearance to
allow for the fitting of the valve connec-
tions.
- Fix the bracket level and with fixings capa-
ble of supporting the weight.
- Hang the boiler and then tighten the
screws indicated in fig 4.
2.3
HOW TO FIT C.H. AND D.H.W.
FITTINGS AND GAS COCK
(fig. 5)
– C.H. CONNECTIONS (R & M)
Fit the two isolation valves (10) using the
gasket supplied (6). Fit the C.H. filling
loop between the C.H and D.H.W. cir-
cuits, ensuring the correct position and
orientation of the isolation valves.
– D.H.W. CONNECTION (E & U)
Fit the supplied; pressure reducing valve
(17), check valve (16), and expansion
relief valve assembly (14) with its associ-
ated tundish (15), ensure that on com-
pletion of the installation that the tun
dish is visible to the user, in the D.H.W.
supply to the appliance, the flow from
this assembly should be connected to
the cold water inlet (E) via the flow regu-
lator housing supplied. Ensure flow regu-
lator (11) and gasket (1) supplied, are fit-
ted in the flow regulator housing.
See fig. 5 and fig. 6 for installation
details. It is important that no isolating
valve is fitted between the expansion
relief valve and the inlet to the D.H.W.
tank. Any additional D.H.W. drain down
tap fitted should be positioned as low as
possible to ensure that at least 80% of
t he D.H.W. t ank’s capacity can be
drained.
If installed in a Hard Water area, then a
suitable device should be fitted to treat
the mains supply to the appliance (Con-
tact your Water Distribution Company
for advice on suitable devices). Fit the
quarter bend (2) to the hot water outlet
(U) using the gasket supplied (1).
– GAS CONNECTION (C)
Fit the gas cock (12) to the gas connec-
tion (R) using the gasket supplied (6).
2.4
WATER SYSTEMS - GENERAL
This appliance is designed for connection to
sealed central heating water systems.
Check that the mains water flow is sufficient
to produce the required DHW flow rate but
does not exceed 4 bar pressure.
A expansion relief valve is incorporated
within the valve kit. Inlet safety kit and all
safety devices must be installed.
For balanced pressures in premises
For balanced pressure to the whole pre-
mises an additional pressure reducing
valve should be installed at the inlet to the
premises set at 3.5 BAR.
The maximum water supply pressures to
the pressure reducing must be no more
than 16 BAR.
2.4.1
Treatment of Water
Circulating Systems
– All recirculatory systems will be subject
to corrosion unless an appropriate
water treatment is applied. This means
that the efficiency of the system will
deteriorate as corrosion sludge accu-
mulates within the system, risking dam-
age to pump and valves, boiler noise and
circulation problems.
– For optimum performance after installa-
tion this boiler and its associated central
heating sys t em mus t be flushed in
accordance with the guidelines given in
BS 7593 “Treatment of water in domes-
tic hot water central heating systems”.
– Sime Ltd recommend only the use of
FERNOX products for the flushing and
final treatment of the system water.
This is particularly important in hard
water areas. Artificially softened water
must not be used to fill the heating sys-
tem.
Failure to flush and add inhibitor to the
system may invalidate the appliance
warranty.
– It is important to check the inhibitor con-
centration af ter installation, system
modification and at every service in
accordance with the manufacturer’s
instructions.
(Test kits are available from inhibitor
stockists).
2.4.2
Requirements for
sealed water systems
The heating system design should be based
on the following information:
a) The available pump head is given in fig.
2
INSTALLATION
Fig. 4