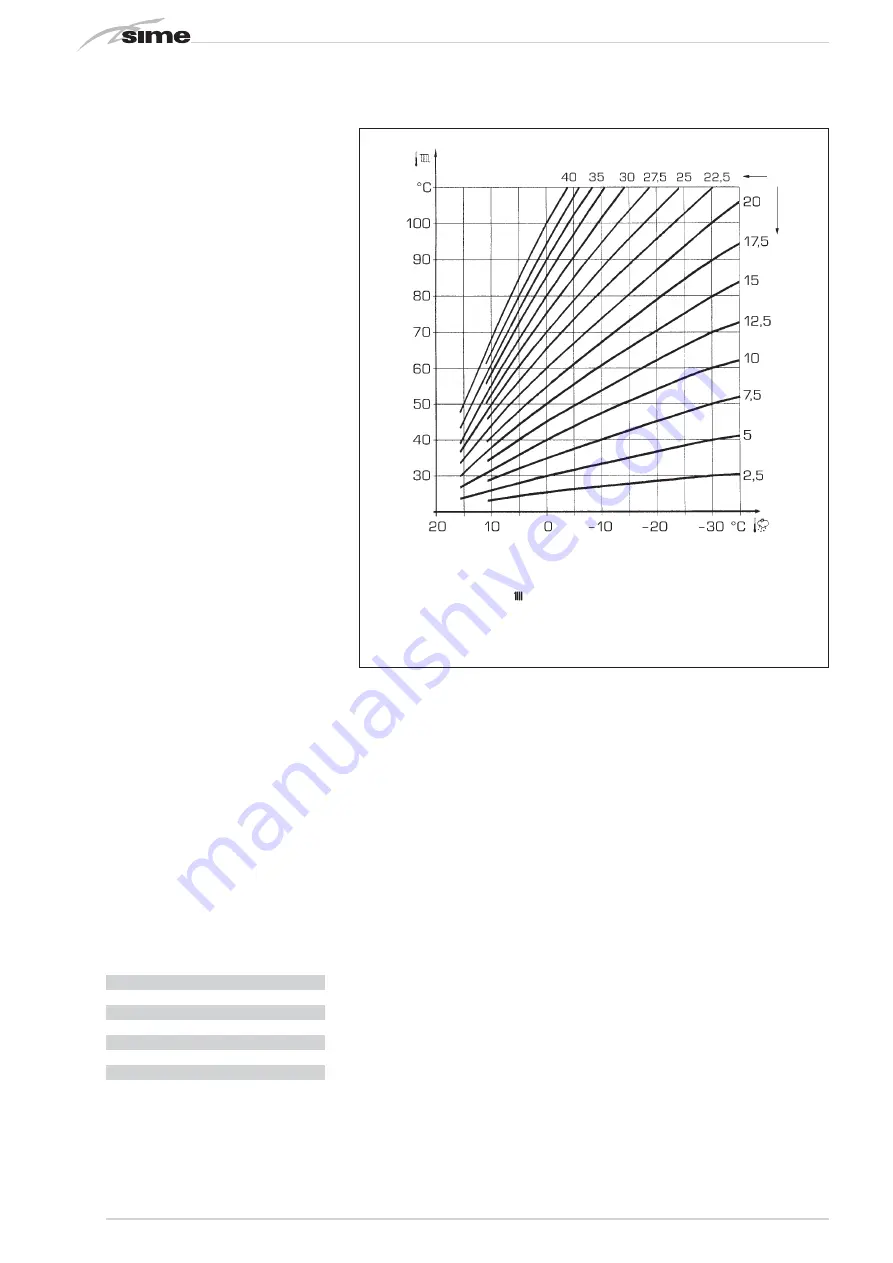
82
3.4
EXTERNAL SENSOR (fig. 15)
If there is an external sensor, the heating
settings SET can be taken from the climatic
curves according to the external tempera-
ture and, in any case, limited to with the
range values described in point 3.2 (para-
meters PAR 13 and PAR 14).
The climatic curve to be set can be selected
from a value of 3 and 40 (at step 1).
Increasing the steepness of the curves of
fig. 15 will increase the output temperature
as the external temperature decreases.
3.5
CARD FUNCTIONING
The electronic card has the following func-
tions:
– Antifreeze protection of the heating cir-
cuit.
– Ignition and flame detection system.
– Control panel setting for the power and
the gas for boiler functioning.
– Anti-block for the pump which is fed for
a few seconds after 48 hours of inacti-
vity.
– Chimney sweep function which can be
activated from the control panel.
– Temperature which can be shifted with
the external sensor connected.
It can be set from the control panel.
– Automatic regulation of the ignition
power
and
maximum
heating.
Adjustments are managed automati-
cally by the electronic card to guaran-
tee maximum flexibility in use of the
system.
– Interface with the following electronic
systems: remote control CR 73 o CR
63, with coupling kit card expansion
code 8092240.
3.6
TEMPERATURE
DETECTION SENSOR
Table 3
gives the values of the electrical
element (
Ω
) obtained on the heating sensor
according to the variations in temperature.
When the heating sensor (SM1/SM2) is
interrupted, the boiler will not function
for both services.
3.7
ELECTRONIC IGNITION
Ignition and flame detection is controlled by
a single electrode on the burner which gua-
rantees reaction in the case of accidental
extinction or lack of gas within one second.
3.7.1
Functioning cycle
Burner ignition occurs within max. 10
seconds after the opening of the gas valve.
Ignition failure with consequent activation of
block can be due to:
–
Lack of gas
The ignition electrode persists in dischar-
ging for max. 10 seconds. If the burner
does not ignite, the anomaly is signalled.
This can happen the first time the boiler
is switched on after a long period of inac-
tivity due to the presence of air in the gas
pipes.
It can be caused by a closed gas tap or by
a broken valve coil (the interruption does
not allow for opening).
–
The electrode does not discharge.
In the boiler, only the opening of the gas
to the burner can be detected. After 10
seconds the anomaly is signalled.
It can be caused by an interruption in the
electrode wire or if it is incorrectly ancho-
red to the connection points.
Or the electrode may be earthed or
strongly worn: it must be replaced.
Or the electronic card may be defective.
In the case of a sudden lack of voltage, the
burner will immediately switch off. When
voltage returns, the boiler will automatically
start up again.
3.8
FUMES THERMOSTAT
“25 OF”
This is a safety measure against the return
of the fumes into the environment due to
an inefficient or partially blocked chimney
(7 fig. 3).
It reacts by blocking the functioning of the
gas valve when the fumes are continually
forced back into the environment, in a
quantity that can be dangerous. If the boiler
repeatedly stops, it will be necessary to
carefully check the chimney, and to carry
out all modifications and take all measures
necessary to restore it to an efficient
working state. After every intervention car-
ried outon the device, check correct func-
tioning. In the case of replacement, use only
original spare parts.
3.9
FUMES PRESSURE SWITCH
“25-30 BF” (fig. 16)
The pressure switch is calibrated by the
manufacturer at the following values:
0.62 - 0.72 H
2
O for vers.
“25 BF”
0.45 - 0.55 H
2
O for vers.
“30 BF”
,
which can guarantee boiler functioning also
TABLE 3
Temperature (°C)
Resistance (
Ω
)
20
12.090
30
8.313
40
5.828
50
4.161
60
3.021
70
2.229
80
1.669
Fig. 15
ATTENTION: curves are calculated at an ambient temperature of
20°C. Using the
key on the control panel, the user can change
the set ambient by ± 5°C for which the curve is calculated.