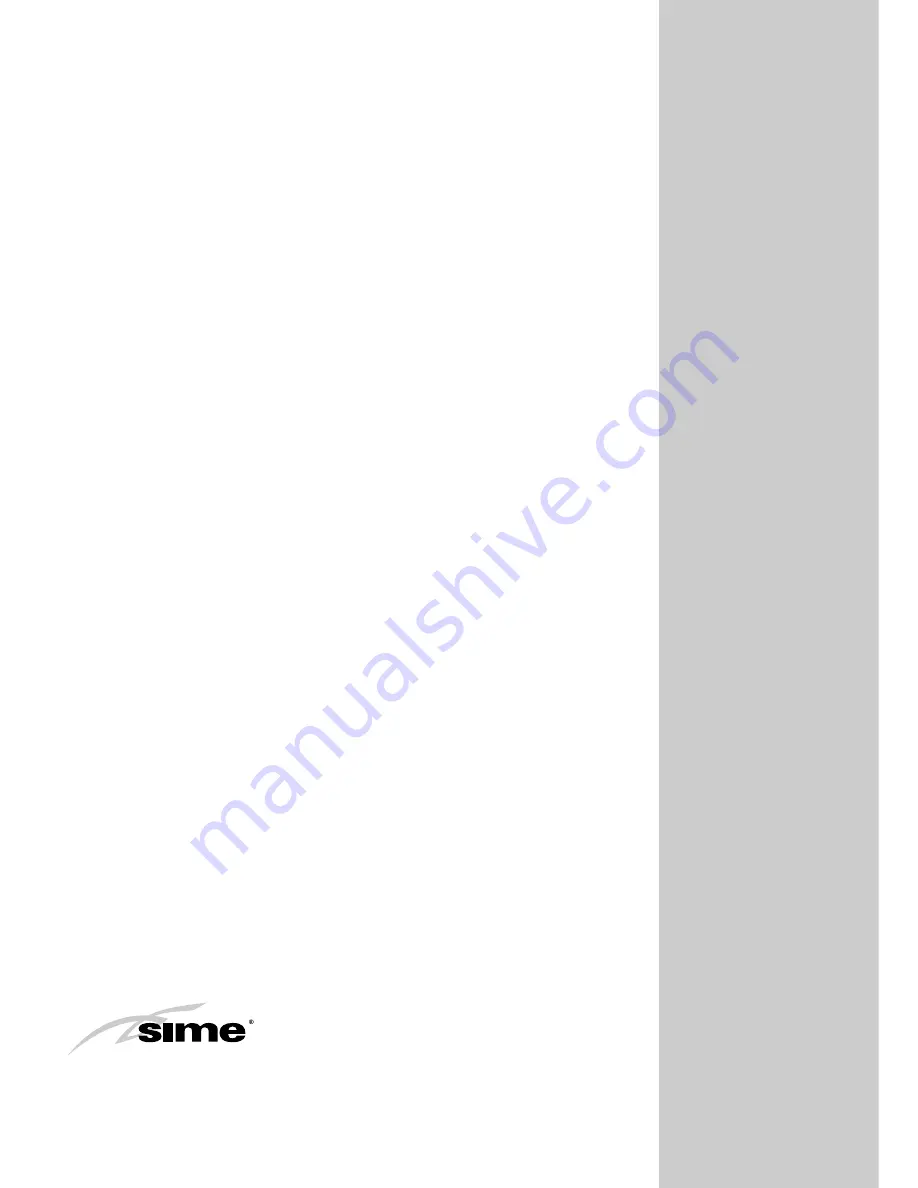
Cod.
6272206B
-
Documentation
Dpt.
Sime Ltd
Unit D2 Enterprise Way, Bradford Road, Idle, Bradford BD10 8EW
Tel. 0870 9911114 - Fax 0870 9911115
www.sime.ltd.uk - e-mail: [email protected]
Summary of Contents for benchmark FRIENDLY FORMAT
Page 1: ...Friendly Format Installation and servicing instructions GB ...
Page 33: ...Friendly Format User instructions GB ...
Page 34: ......
Page 39: ......