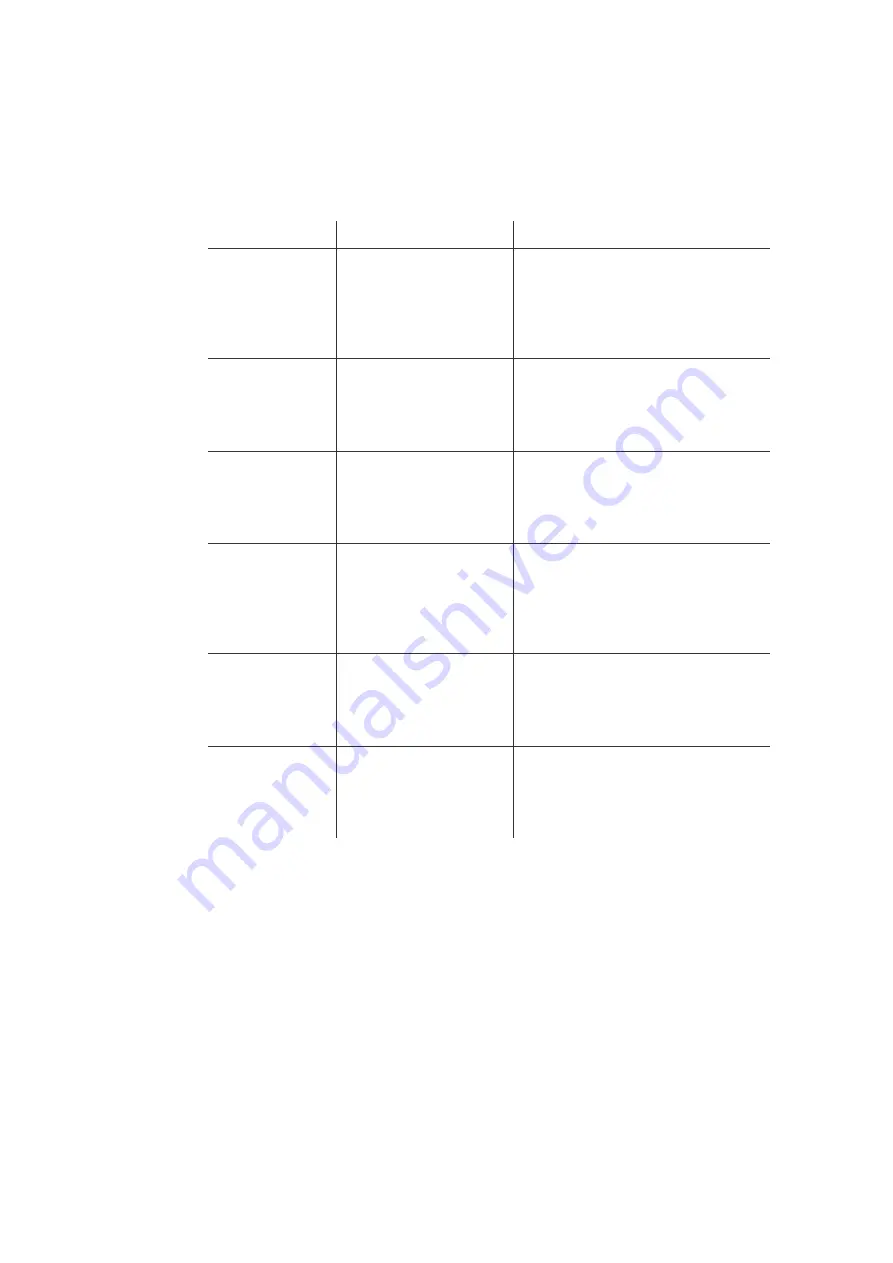
Instruction Manual OilGuard Ex M
44
10241E/2
6.3
Fault reports
If a fault occurs during operation,
**** Fault ****
appears in the display
with a fault report, which can help in determining the cause of the fault.
Message Meaning
Possible
causes
Connection
lost…
The control unit cannot
establish a connection
to the main electronics.
-
Interrupted connection between
control unit and the main
electronics
-
Defect in the electronic system
(
→
service engineer)
Light
The photocell does not
receive light.
-
Defective light source
(
→
Section 5.3)
-
Defective photocell or
electronics (
→
service engineer)
Measurement
A fault occurred while
measuring.
-
Chopper defective
(
→
service engineer)
-
Defective electronics
(
→
service engineer)
Current 1
The output signal is
faulty.
-
Connection terminals are open
on the output signal
(
→
Section 3.2)
-
Open circuit in the loop current
of the output signal
SystemFault
An internal system
fault has occurred
-
The parameter memory has lost
its values (
→
service engineer)
-
The fault history is overfilled
(
→
service engineer)
Flow rate
The external flow rate
monitor has determined
a fault.
-
Flow rate incorrect
-
Open terminals 10, 16a
(
→
Section 3.2.5,
→
Reference Handbook)