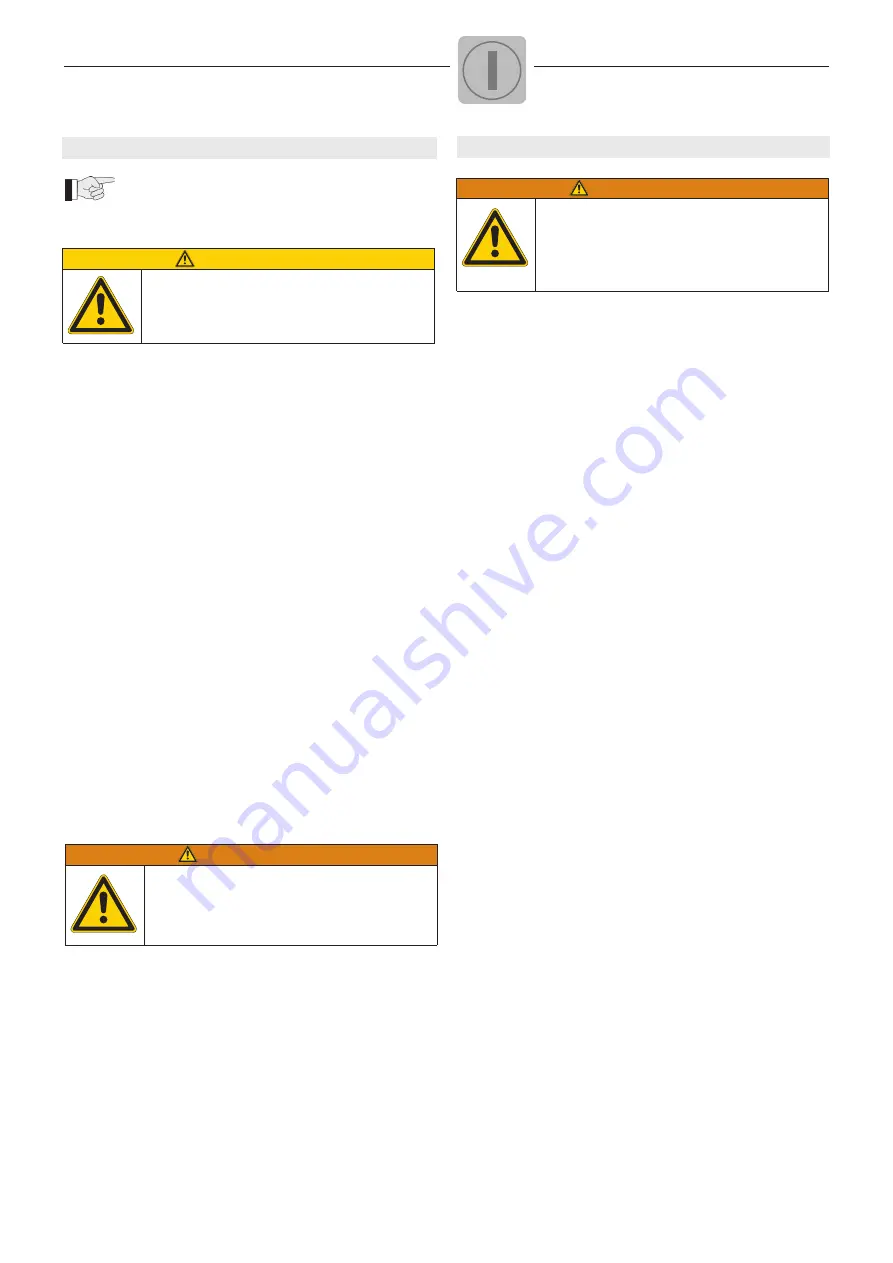
10.19
HSM 3000
23
6.5.1 WORKING BELOW CARRIAGE
– Set the machine in manual operation to a position
permitting work on the machine (e.g. carriage down).
– Unhook safety chain from parking position (on ma-
chine column).
– Slide safety chain to the right over the suspendeding
position mounted on carriage.
– Suspend the hook at the end of the safety chain in
the red marked carrying loop mounted on carriage.
– Use shortening hook of safety chain to tighten the
chain to optimum length.
– Leave the danger area, close the door from outside
and press „
Reset
“ button on HMI. Manually move
the carriage down until the safety chain is tightened.
– Enter danger area and perform maintenance work
on/below carriage.
After maintenance work:
– Leave the danger area, close the door from outside
and press „
Reset
“ button on HMI. Manually move
the carriage up until the safety chain is slackened
– Unhook shortening hook (if this was required).
– Remove hook of safety chain from red carrying loop
on carriage.
– Slide back and hook the safety chain into parking
position (on machine column).
– When work in the danger area is completed, the
door must be closed from outside and the
„
Reset
“ button pressed.
WARNING
Refer to Chapter 6.5 when working in the
danger area.
When working on and particularly
under the carriage it must be secured
against falling down as following:
6.5 WORKING IN DANGER AREA
It is sometimes necessary to open the door
in the safety fence to eliminate faults from
the machine. When working in the danger area refer
also to Chapter 2.
a) Set the machine in manual operation to a position
permitting work on the machine (e.g. carriage
down).
b) Open the door in the safety fence. With the door
open the machine motors are disconnected from
the supply and the conveyor unit is stationary.
c) When working on and particularly under the carria-
ge it must be secured against falling down, refer to
Chapter 6.5.1.
d) For work in the danger area, the following must be
carried out after operation of the key switch (Fig. 3/4)
to work with the enabling button (see Table 4.1).
e) For prolonged work in the danger zone the main
switch should be set to position „
0
“. Only qualified
personnel should work on electrical components.
f)
Working at heights above 2 metres
This work on the machine stand is seldom neces-
sary, e.g. to change defective flash lamp. Auxiliary
aids such as secure ladder, etc. should be used.
g)
Leaving the danger area
When work in the danger area is completed, the
door must be closed from outside and the
„
Reset
“ button pressed.
WARNING
Before acknowledging (Reset), ensure
without fail that there is nobody still in
the danger area.
CAUTION
In this case the following points should
be noted: