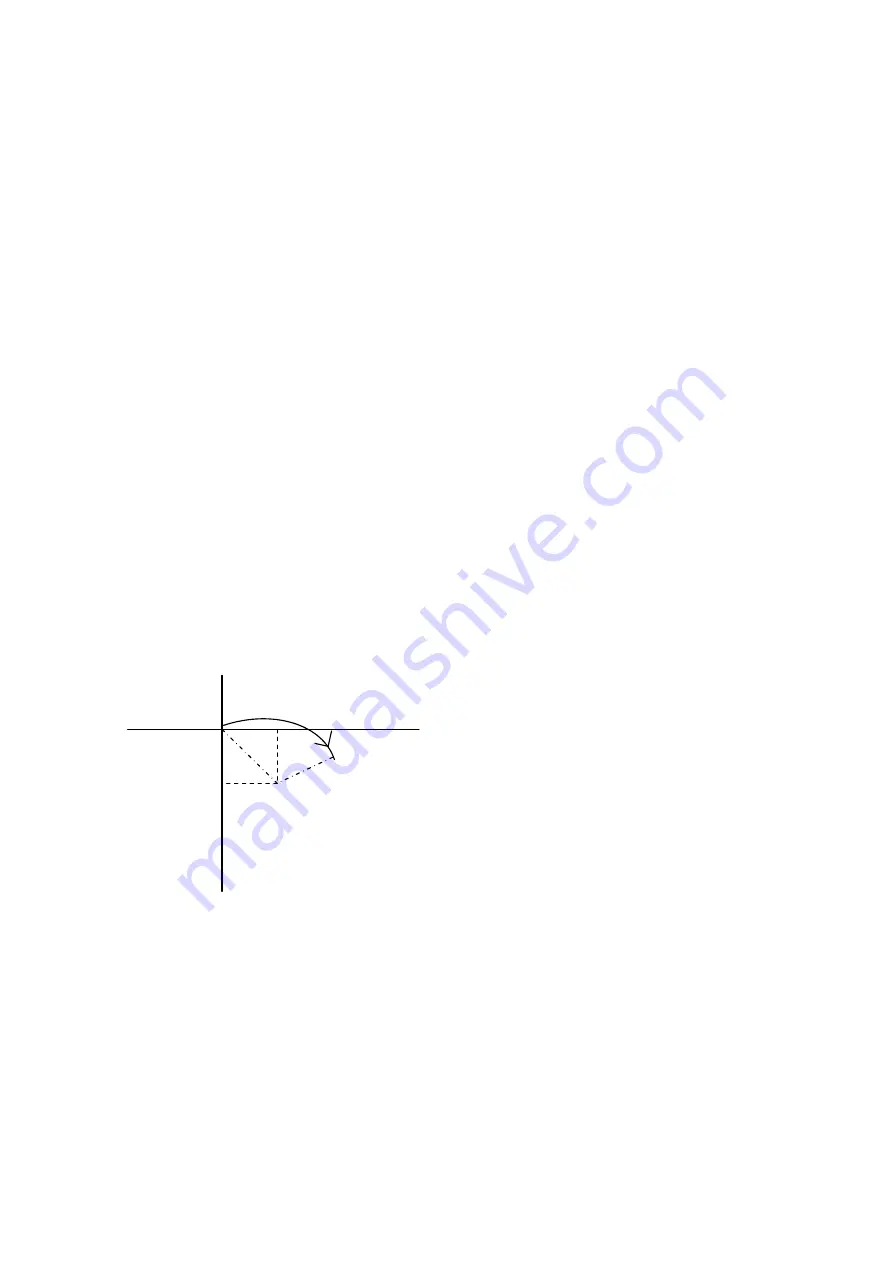
SC40401-K10-15002
1st
44
Copyright 2015, SIGMAKOKI Co.,Ltd.
4-1-6-2 E
:
:
:
:
1 command
(Arc interpolation movement command 1)
(1) Function
This command indicates a designation of center point and degree of ended point in order to operate the
arc movement
(2) Example
E
:
:
:
:
1, axis1,axis2,d,c1,c2,ae
axis1, axis2
:
:
:
:
1
~
~
~
~
4 means to designate the number of axis to operate arc interpolation
movement. Same number of axis or unconnect is prohibited. Axis1
represents X axis and axis2 represents Y axis.
d
:
:
:
:
0 or 1
0 is CW rotation(Clockwise). 1 is CCW rotation (Counterclockwise).
c
:
:
:
:
Center point coordinate (c1 axis1 setting value
、
c2 axis2 setting value)
(unit of setting 0.01
µ
m unit)
ae
:
:
:
:
Degree of ended point (deg) (Setting range
:
integer of 0°<ae
≦
360° The other degree
than mentioned is NG.)
E
:
:
:
:
1,3,4,0,5000,-5000,90
A center point coordinate is based on a relative coordinate of the current
position (0.05mm,-0.05mm) and move stages of axis No3
、
axis No4
90°from current position to degree of ended point position clockwise.
0.05mm
-0.05mm
90
°
Axis 3
Axis4