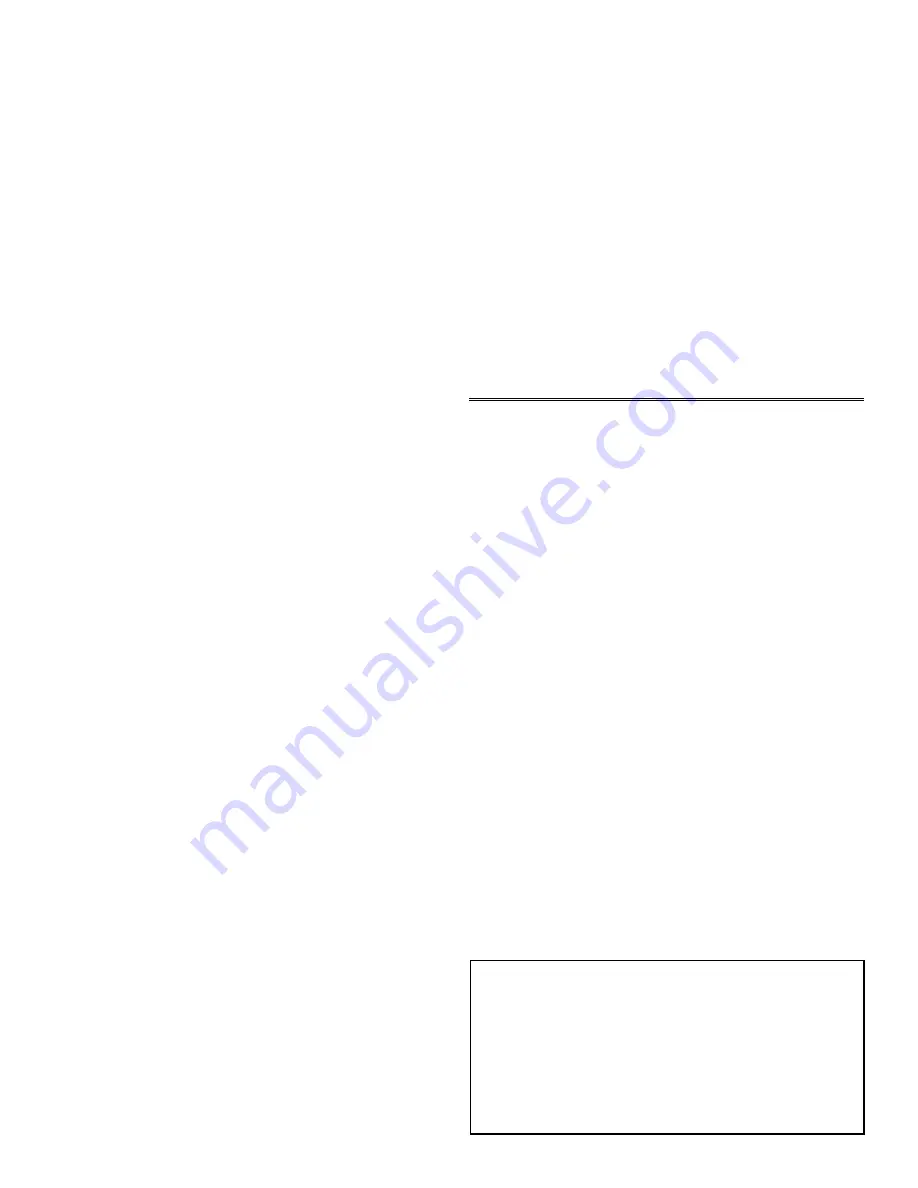
3
WINGS & related parts
❑
1 Right Wing Panel, covered
❑
1 Right Aileron, covered
❑
1 Left Wing Panel, covered
❑
1 Left Aileron, covered
❑
1 Right Aileron Servo Hatch, covered
❑
1 Left Aileron Servo Hatch, covered
❑
4 3/8" x 3/4" x 3/4" Hardwood Aileron Servo Mounts
❑
1 Hardwood Wing Joiner
❑
1 Aluminum Tube Rear Wing Joiner
❑
2 1/8" x 1-1/2" x 1-1/2" Plywood Wing Bolt Plates
❑
2 1/4-20 x 2 Nylon Wing Bolts
LANDING GEAR & related parts
❑
1 Aluminum Main Landing Gear
❑
3 M4 x 15mm PWA* Bolts; for landing gear
❑
2 Steel Wheel Axles
❑
2 M8 Lock Nuts; for wheel axles
❑
2 3-3/4" dia. Main Wheels
❑
4 Wheel Collars with Set Screws
❑
1 Right Fiberglass Wheel Pant, painted
❑
1 Left Fiberglass Wheel Pant, painted
❑
4 M3 x 15mm PWA* Bolts; for wheel pants
CONTROL SYSTEM PARTS
❑
3 RIGHT Metal Control Horns; for ail.(1), ele.(1), & rud.(1)
❑
3 LEFT Metal Control Horns; for ail.(1), ele.(1), & rud.(1)
❑
24 M2.6 x 10mm Metal Screws; for control horns
❑
2 4-40 x 2-3/4" Threaded Pushrods; for elevators
❑
2 4-40 x 3-5/8" Threaded Pushrods; for ailerons
❑
6 4-40 Threaded R/C Links; for ail.(2), ele.(2), rud.(2)
❑
6 4-40 Hex Nuts; jam nuts for R/C links
❑
4 4-40 Solder Links; for ail.(2), ele.(2)
❑
1 1/8" od x 18" Nylon Pushrod Tubing; for throttle pushrod
❑
1 1/16" od x 18" Stranded Steel Cable; for throttle pushrod
❑
1 1/8" x 5/8" x 1-1/4" plywood Throttle Tube Support
❑
1 2-56 size Solder Link; for engine end of thr. pushrod
❑
1 Brass Pushrod Connector Body; servo end of thr. pushrod
❑
1 Molded Nylon Retainer; for pushrod connector
❑
1 4-40 x 1/8" Socket Head Bolt; for pushrod connector
TAILWHEEL ASSEMBLY PARTS
❑
1 Main Leaf-Spring with Steering Arm, Wheel Yoke, and
Tailwheel installed
❑
1 Short Leaf-Spring
❑
2 Coiled Steering Springs
❑
1 Metal Rudder Horn (T-shaped)
❑
2 M2 x 9mm PWA* Screws
❑
3 M3 x 14mm PWA* Screws
PULL-PULL CABLE SYSTEM PARTS
❑
1 .024" dia. x 96" Steel Cable
❑
4 Copper Swage Tubes
❑
4 Threaded Rigging Couplers with Knurled Stop Nut
❑
4 Metal JDL R/C Links
FUEL TANK PARTS
❑
1 450cc (15.2 oz.) Oval Plastic Tank
❑
1 Rubber Stopper
❑
1 Metal Front Clamp
❑
1 Metal Rear Clamp
❑
1 Clamp Bolt
❑
1 Metal Clunk Pickup
❑
2 Aluminum Tubes
❑
1 Fuel Tubing for inside tank
❑
2 9" Fuel Tubing
SPINNER PARTS
❑
1
3" dia. Spinner, White
❑
1
3" dia. Back Plate, White
❑
1
Prop Shaft Adapters
❑
4
Self-Tapping Screws
MISCELLANEOUS
❑
20 M2.6 x 10mm PWA* Screws; for aileron servo hatches(8),
ail. servo mount blocks(4), fuselage hatch(4), cowling(4)
❑
6
M3 x 8mm PWA* Screws; for canopy
❑
2
Glass-Filled Engine Mounts
❑
4
10-32 x 1" Socket-Hd. Mtg. Bolts; for engine mount
❑
4
10-32 Blind Nuts; for engine mount
❑
4
#10 Flat Metal Washers; for engine mount
❑
1
Decal Sheet
* PWA = phillips washer-style head
NOTE ABOUT COVERING MATERIAL
Your EXTRA 300XS ARF has been professionally covered with
Oracover
®
#10 White, #54 Violet, and #71 Black. (Note: In the
United States, Oracover
®
is sold under the name of Hangar 9
Ultracoat
®
. The equivalent Ultracoat colors are called #870 White,
#868 Smoke Purple, #874 Black).
Oracover
®
is well known for its ease of application, light weight and
consistency of color. If you live in a drier climate, you may notice
that some wrinkles might develop after removing the covered parts
from their plastic bags. If that is the case, there is no need to be
alarmed. This is perfectly normal in low humidity climates. Your
model was built and covered in a part of the world with relatively
high humidity and therefore the wood was likely carrying a fair
amount of moisture. When exposed to drier air, the wood typically
loses this moisture, dimensionally "shrinking" in the process. In
turn, this may cause some wrinkles. (If you've been in modeling
long, you've undoubtedly noticed that most iron-on coverings stay
tight in the summer only to loosen a little in drier winter conditions.)
Any wrinkles that appear in the covering are easy to remove by
using a hobby-type heat iron. We suggest covering the iron's shoe
with a thin cotton cloth, such as an old T-shirt, to prevent scratching
the film. The iron should be set to about 280
O
- 300
O
F.
First, use the heated iron to go over all the seams and color joints
in the covering, making they are all sealed and well adhered. Then
use the heated iron to lightly shrink the material - do not press on
it. Once the covering is tight, lightly iron the material back down to
the wood. You can also use a hobby-type heat gun to re-shrink the
covering, but you must be extra careful around the seams. Re-
heating seams may cause them to "creep", making them unsightly.
MODELER’S TIP:
One of the most common problems
associated with shrinking any covering film is controlling the
heat around seams. Heat applied close to or directly onto
seams re-heats the covering adhesive and the seam will often
"crawl". This is easy to control. Just tear a few paper towels
into strips and soak them in cool tap water. Lay the wet strips
over any covering seam and use your heat gun or iron as you
normally would. The wet strips keep the seam cool while the
covering immediately next to it shrinks. This tip works great
with any iron-on covering.