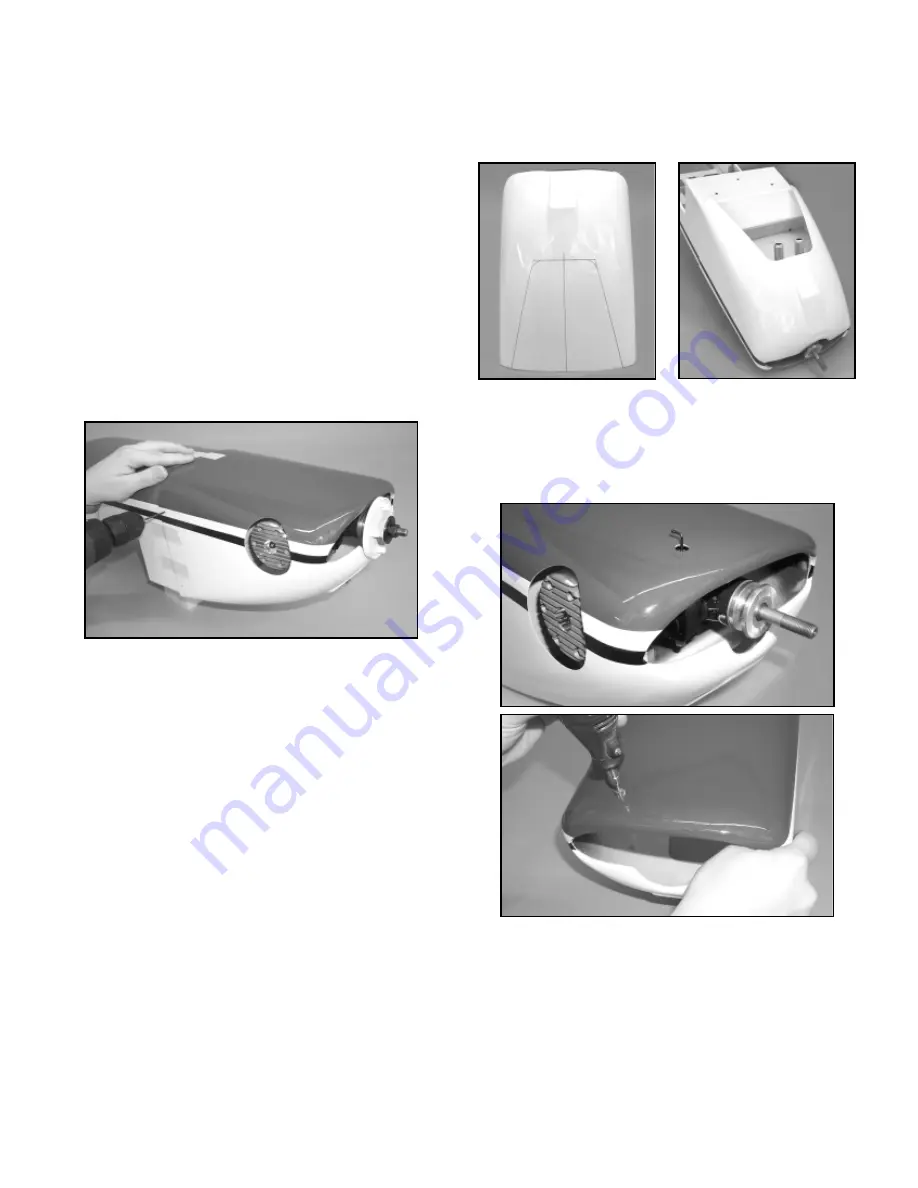
10
cut-off wheel for a sanding drum bit in your Dremel
®
Tool. Use the
drum sander bit to round the upper two corners and to lightly clean
up any jagged edges. Use 220 sandpaper to clean up the edges
of the cutout, without sanding the paint. Make sure the edges are
uniform and free of any loose glass. Remove all fiberglass dust
from the cowl with tack rag or with alcohol on a clean cloth.
❑
5) Mount the trimmed cowl back onto the fuselage. In this step
you will determine the location for the hole required for access to
your engine's needle valve. This is easiest done using the penlight
mentioned earlier in step #1 and fine-tip marker pen. First find the
approximate location of where the needle valve will exit by looking
carefully at your engine carburetor. Mark that location on the cowl.
Now look a little closer and use the penlight to adjust the mark just
made from the outside of the cowl.
Reposition the mark as
required to get as close as possible to the exact needle valve
location. Use the Dremel
®
Tool and a small tipped grinding bit to
make a small hole (maybe 1/16" in diameter) in the cowl, at the exit
mark just made. Chances are that you were quite close to the
actual exit point. Stick a piece of music wire into the hole, down to
the needle valve.
Carefully observe if the hole needs to be
repositioned to straighten up the wire, as if it were the needle valve.
Make another mark on the cowl and again use the Dremel
®
Tool to
open the hole just a little towards the correct position.
In this
manner, continue checking and adjusting the exit hole until it aligns
❑
2) Once the cowling is in place without any part of the engine
contacting it, push the cowl back onto the fuselage until the engine
prop mounting flange emerges from the front of the cowl. This
flange must clear the front of the cowl by at least 1/16" (1/16" to
1/8" is OK). Slip the spinner backplate in place over the engine
prop shaft, pushing it all the way back to the prop mounting flange.
Mount a prop or prop stub "dummy" in place on the drive shaft.
Tighten the prop assembly sufficiently to bring the spinner
backplate firmly in place against the prop mounting flange.
Recheck to make sure you have at least a 1/16" gap between the
back of the spinner backplate and the front of the cowl. Center the
spinner backplate to the cowl and use masking tape to secure the
back of the cowl to the fuselage, leaving the four pre-drilled
mounting holes along the back edge of the cowling uncovered.
❑
3) With the cowl securely taped in place, use a 3/64" (or #56)
dia. drill bit to drill pilot holes in the fuselage, centered in each of
the four pre-drilled mounting holes in the cowl. Mount the cowl to
the fuselage with four M2.6 x 10mm PWA Screws provided.
Double check your work one more time to make sure that the cowl
is bolted on in the correct location and alignment. Then remove the
cowling from the fuselage.
❑
4) An opening must now be made in the bottom of the cowling
to allow engine cooling air to properly flow through and exit the
cowling. This is absolutely necessary for proper cooling! Without
this opening, your engine will overheat and quit. If you are using a
2-stroke engine, such as the Irvine 1.20 or 1.50, or a 4-stroke such
as the Saito 1.20, 1.50, or the 1.80, we suggest using an opening
which measures 6-1/2" long from front to back, 6-1/2" wide at the
back edge by 3-1/2" wide at the front. This size opening allows the
exhaust pipes on the recommended SIG muffler for the Irvine
engines to clear the cowl with plenty of additional air exit area, as
well as allowing plenty of air for 4-stroke engines. The dimensions
of this opening may certainly be “customized" for your particular
engine/muffler set-up, as long as there is sufficient air exit area.
Stand the cowl upright on its rear edge, nose up, with the bottom
side facing you. Use a fine-point marker pen to draw an outline of
the area you need to cut out. Measure carefully to make sure that
the opening is properly centered and located. We suggest using a
circle guide to round the two upper corners of the cut out area for
a better look.
The air outlet can be easily cut from the fiberglass cowl using
a Dremel
®
Tool and a large cut-off wheel.
Before cutting out
the cowl opening be sure to wear safety glasses and a mask of
some kind to avoid inhaling any fiberglass dust.
Carefully cut
the fiberglass, using the lines previously drawn. If you are careful,
you will find that you can get fairly close to the lines with the
cut-off wheel. The goal is to remove most of the material within the
lines. Once the piece is cut and removed, exchange the cut-off