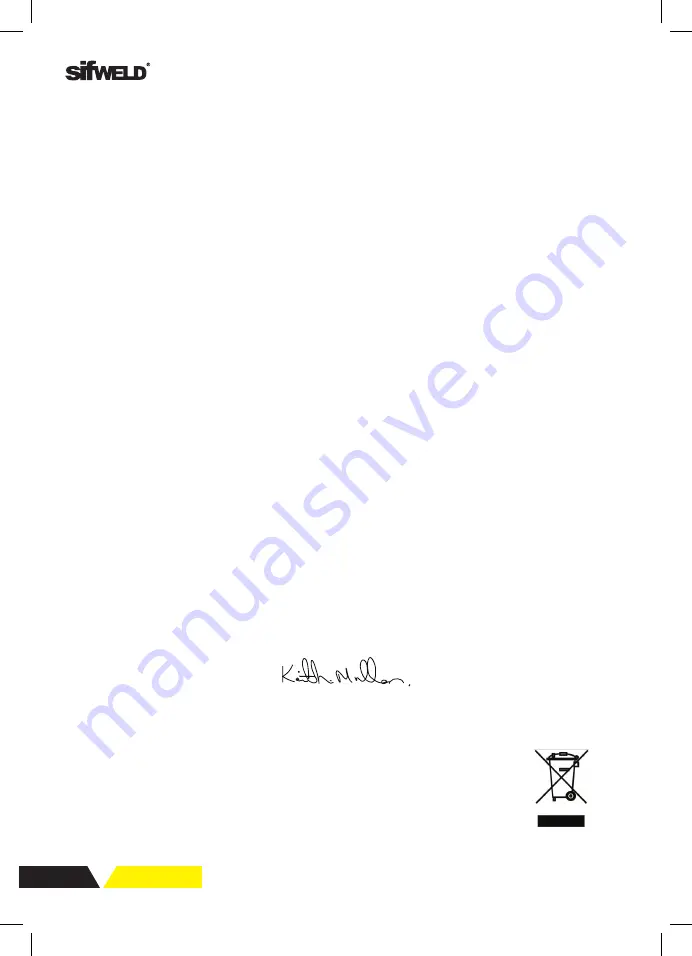
2
DECLARATION OF CONFORMITY
The Low voltage Directive 2006/95/EC of 12 December 2006, entering into force 16 January 2007
The EMC Directive 2004/108/EC, entering into force 20 July 2007
The RoSH Directive 2011/65/EC, entering into force 2 January 2013
Type of Equipment
Welding power source for TIG/TAG, MMA welding
Brand name or trade mark
SifWeld® Evolution
Type designation etc.
TS200ACDC
Manufacturer or his authorised representative established within the EEA
Name, address, telephone no, fax no
Weldability Sif
Peters House, The Orbital Centre
Icknield Way, Letchworth
Hertfordshire, SG6 1ET
United Kindom
Phone: +44 (0)845 130 7757 Fax: +44 (0)800 970 7757
The following harmonised standard in force with the EEA has been used in the design:
EN60974-1- Arc welding equipment- Part 1: Welding power sources
EN60974-10 Arc welding equipment - Part 10: Electromagnetic Compatibility (EMC) requirements
Additional information: restrictive use, Class A equipment, intended for use in locations other than residential
By signing this document, the undersigned declares as manufacturer, or the manufacturer’s authorised
representative established within the EEA, that the equipment in question complies with the safety
requirements stated above.
WEEE Directive & Product Disposal
At the end of its serviceable life, this product should not be treated as household
or general waste. It should be handed over to the applicable collection point for
the recycling of electrical and electronic equipment, or returned to the supplier for
disposal.
Place and Date
Letchworth, UK
01-04-2015
Position
Quality Manager
Weldability Sif
Signiture
Keith Mullan