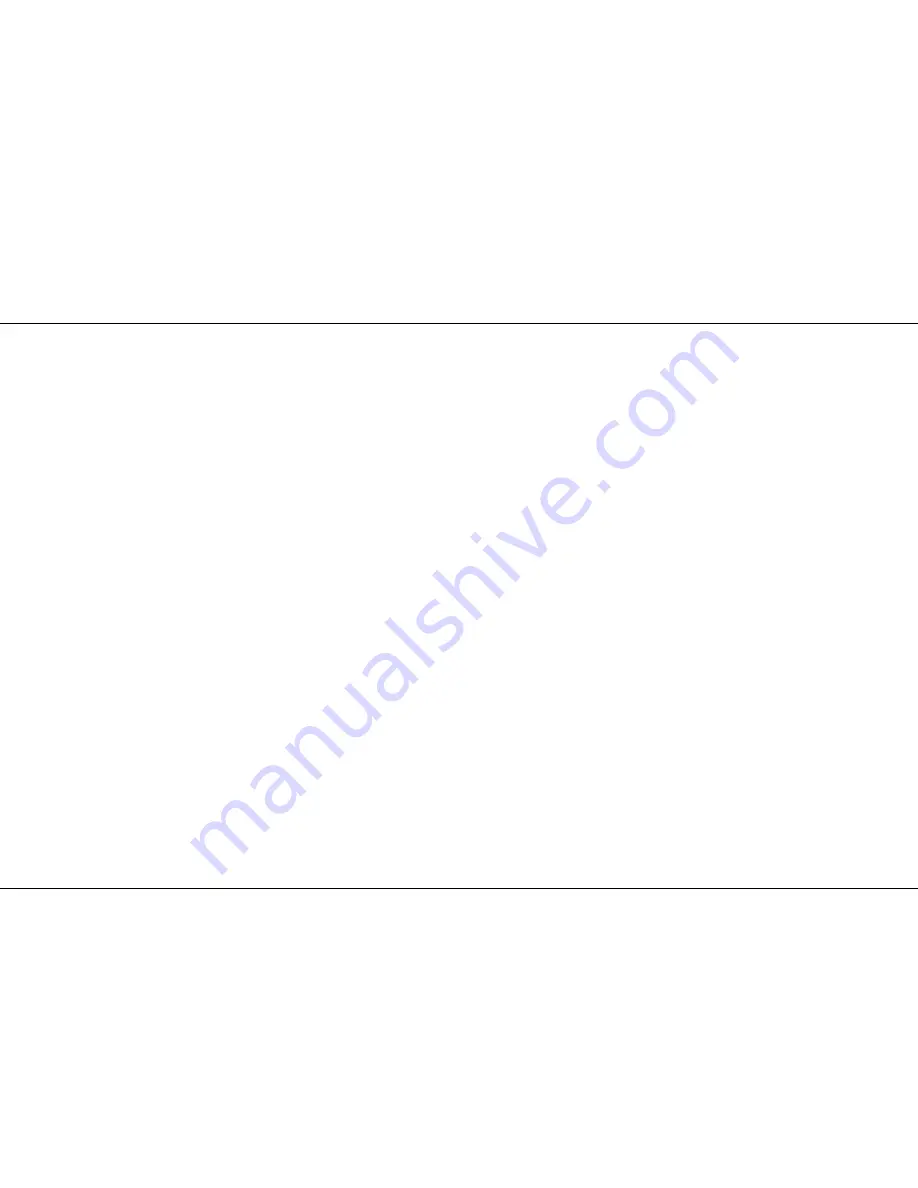
General repair instructions – Laundry
2015-09-07 / DIS 113_58300000171499_ara_en_c
Copyright by BSH Hausgeräte GmbH
Page 1 of 65
1 Concerning this document
3
1.1
Purpose and target group.............................................................................. 3
1.2
Other applicable documents...........................................................................3
2 Safety
4
2.1
Qualification.................................................................................................... 4
2.2
Information in warning messages...................................................................4
2.3
Basic safety instructions.................................................................................6
2.4
Grouped safety messages..............................................................................7
3 Design and function
8
3.1
Process air circuit........................................................................................... 8
3.2
Heat pump circuit........................................................................................... 9
3.3
Temperature control with fan (cooling air)....................................................11
3.4
Compressor...................................................................................................12
3.5
NTC...............................................................................................................13
3.6
Door lock.......................................................................................................14
3.7
Drum bearing (rear panel)............................................................................15
3.8
Drum bearing (bearing shield)......................................................................16
3.9
Condensate pump........................................................................................ 17
3.10 Condensate tank...........................................................................................19
3.11 Motor............................................................................................................. 20
3.12 Evaporator rinsing system............................................................................23
4 Fault diagnosis
25
4.1
Malfunctions................................................................................................ 25
Drying programme does not start.................................................................25
Drying programme only briefly starts running.............................................. 25
Drum not rotating..........................................................................................25
Driving system.............................................................................................. 25
Heating system............................................................................................. 26
4.2
Result faults................................................................................................ 27
Washing not drying / residual moisture excessive....................................... 27
„Drain tank" is displayed...............................................................................27
Laundry bunched up (laundry roller)............................................................ 28
Condensate in collector despite connected drain set...................................28
Clean filter/lint strainer flashes/lights up at end of programme.................... 28
4.3
Odours......................................................................................................... 29
Smell of oil....................................................................................................29
Chemical odour.............................................................................................29
Plastic odour / melted...................................................................................29
Charred smell............................................................................................... 29
Musty odour.................................................................................................. 29
4.4
Noise............................................................................................................ 30
Humming noise.............................................................................................30
Running noises from the drum bearing........................................................30
Clicking noises..............................................................................................30
Rattling noises.............................................................................................. 30
Banging noises............................................................................................. 30
Pulsating noises............................................................................................30
Slurping noises............................................................................................. 30
Buzzing noise............................................................................................... 30
Scraping noises............................................................................................ 31
4.5
Leaks............................................................................................................ 32
Condensate dripping between panel and display........................................ 32
Leakage bottom front left ............................................................................ 32
5 Test
33
5.1
Read out fault memory.................................................................................33
6 Repairs
34
6.1
Installing the appliance.................................................................................34
6.2
Transporting the appliance........................................................................... 35
6.3
Removing/installing the worktop...................................................................36
6.4
Replacing left / right side panel....................................................................37
6.5
Removing/installing control panel.................................................................39
6.6
Flashing the power module.......................................................................... 40
6.7
Removing/installing the power module.........................................................44
6.8
Removing/installing front panel.................................................................... 46
6.9
Removing/attaching air inlet panel............................................................... 47
6.10 Remove/install electrodes for conductivity measurement............................ 48
6.11 Replacing door switch.................................................................................. 50
6.12 Replacing rollers........................................................................................... 52