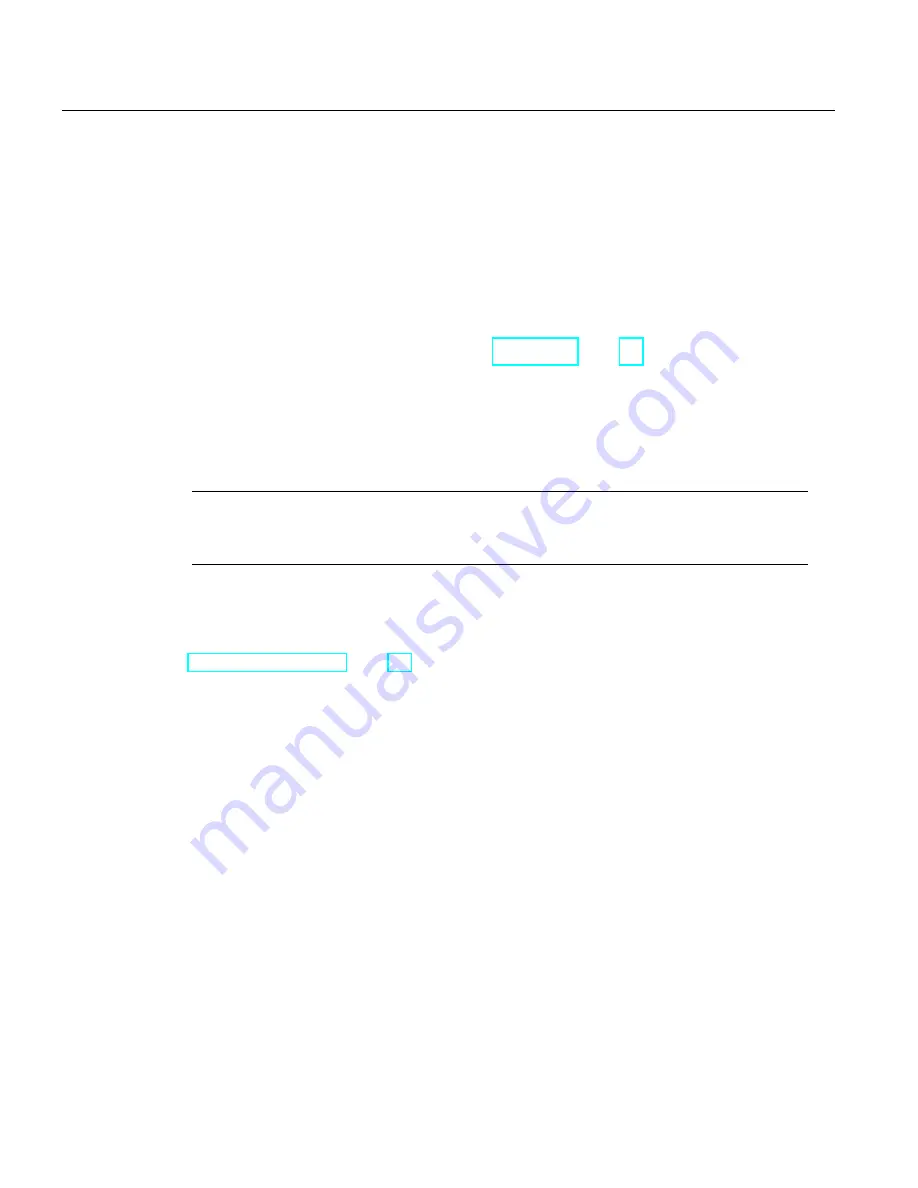
Start Up
8.5 Belt tracking
SITRANS WW310
26
Operating Instructions, 03/2014, A5E33490433-AA
length of the weighfeeder. This is only an approximate specification, as your application may
require more or less tension due to varying belt loading and other operating characteristics.
8.5
Belt tracking
Before attempting to track the belt, be sure:
• belt scraper is in place
• belt tension is near guidelines suggested in
Belt tension (Page 25).
• feeder is level and true
• installation has not warped or twisted the frame
• head and tail pulley are square to the frame and parallel to each other
• plow is contacting underside of the belt, belt is engaged with guide rollers.
Note
•
Do not adjust belt tracking rollers, they have been factory set.
•
Belt plow blades are adjustable vertically for proper contact to the belt.
• belt tension is properly set
Turn on the feeder and observe its tracking line on the head and tail pulleys. If the belt is drifting
toward one side of the feeder, then adjust the telescoper on either side of the machine (see
Telescoper adjustment (Page 26)).
8.6
Telescoper adjustment
1.
Determine which side of the weighfeeder you want to adjust. Compressing the telescoper on
one side will cause the belt to drift toward that side of the weighfeeder. Conversely, extending
the telescoper will cause the belt to drift away from that side of the weighfeeder.
2.
Loosen the jam nut.
3.
Turn the adjusting screw in the desired direction. Often, only a small amount of adjustment (1
turn or less) will be required.
Summary of Contents for SITRANS WW310
Page 1: ...SITRANS Weighfeeders SITRANS WW310 Operating Instructions 03 2014 ...
Page 8: ...Introduction 1 1 The Manual SITRANS WW310 6 Operating Instructions 03 2014 A5E33490433 AA ...
Page 14: ...Operation 4 1 Weighfeeders SITRANS WW310 12 Operating Instructions 03 2014 A5E33490433 AA ...
Page 20: ......
Page 22: ...Calibration 6 3 Span SITRANS WW310 20 Operating Instructions 03 2014 A5E33490433 AA ...
Page 24: ...Wiring SITRANS WW310 22 Operating Instructions 03 2014 A5E33490433 AA ...
Page 47: ......