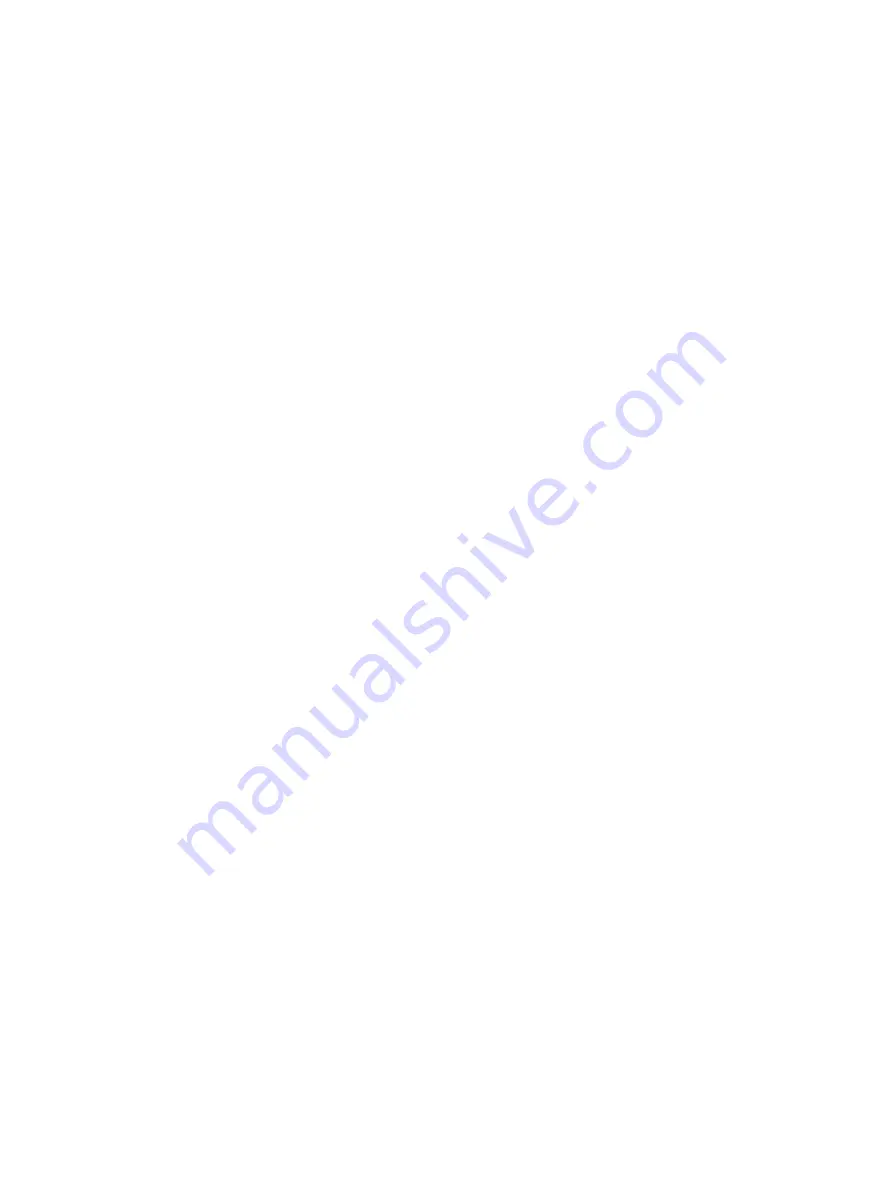
Transducers
Compact Operating Instructions, 09/2021, A5E43390688-AC
3
Table of contents
1
Introduction ........................................................................................................................................... 5
1.1
Purpose of this documentation ............................................................................................ 5
1.2
Checking the consignment ................................................................................................... 5
1.3
Security information ............................................................................................................ 6
1.4
Transportation and storage .................................................................................................. 6
1.5
Notes on warranty ............................................................................................................... 7
1.6
About Siemens' Transducers................................................................................................. 7
2
Safety notes ......................................................................................................................................... 10
2.1
Preconditions for use ......................................................................................................... 10
2.1.1
Warning symbols on device ................................................................................................ 10
2.1.2
Laws and directives ............................................................................................................ 10
2.1.3
Improper device modifications ........................................................................................... 11
2.1.4
Safety Precautions ............................................................................................................. 11
2.2
Use in hazardous areas ...................................................................................................... 12
2.3
Requirements for special applications ................................................................................. 13
3
Installing/mounting ............................................................................................................................. 14
3.1
Basic safety notes .............................................................................................................. 14
3.1.1
Installation location requirements ...................................................................................... 16
3.1.1.1
Insufficient air supply ......................................................................................................... 16
3.1.2
Proper mounting ............................................................................................................... 17
3.2
Disassembly ....................................................................................................................... 17
3.3
Outline and Dimensions ..................................................................................................... 18
3.3.1
XPS Transducers ................................................................................................................ 18
3.3.2
XRS-5 ................................................................................................................................ 19
3.3.3
ST-H .................................................................................................................................. 20
3.4
Mounting .......................................................................................................................... 21
3.4.1
Solids applications ............................................................................................................. 21
3.4.2
Liquids applications ........................................................................................................... 22
3.4.2.1
XPS Transducers ................................................................................................................ 22
3.4.2.2
XRS-5 ................................................................................................................................ 25
3.4.2.3
ST-H .................................................................................................................................. 28