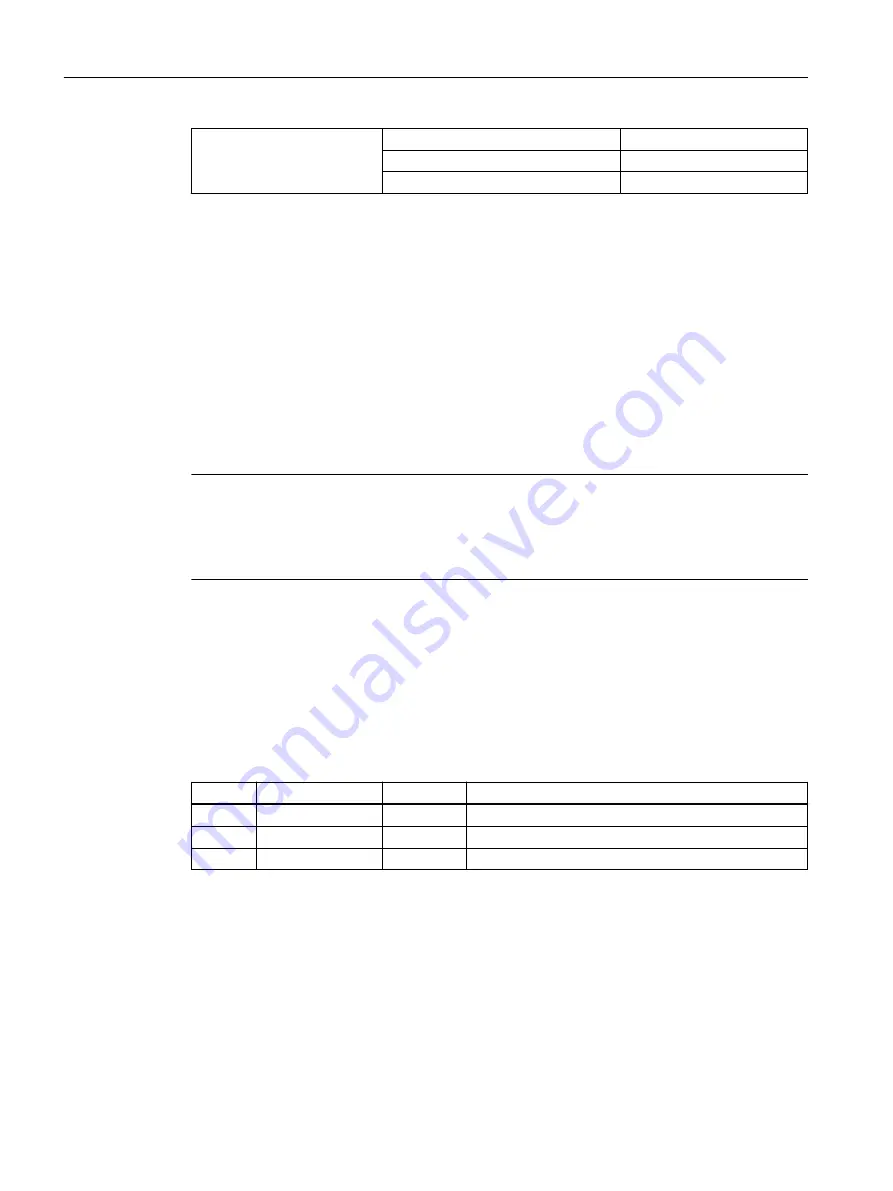
Transient voltage interruptions Outage time
≤ 3 ms
Recovery time
≥ 10 s
Events per hour
≤ 10
Digital inputs
The 24 V supplied at X1 are used to supply the 72 digital inputs.
If the internal supply voltage is not used to supply the digital inputs, this can optionally be
replaced by an external power supply (24 VDC). The reference ground of the power supply
source must each be connected with X111, X222, X333, pin 1 (GND). X111, X222, X333, pin
2 (P24OUT) then remains open.
Digital outputs
To supply (24 V DC) the digital outputs, an additional external power supply source is required.
The power supply is connected to terminals X111, X222 and X333 via pins 47, 48, 49 and 50
(DOCOMx). Ground pins must be connected to a common chassis ground.
Maximum current consumption: 3 x 4 A if all outputs are used simultaneously.
Note
It is the user's responsibility to ensure that the max. current consumption per DOCOMx pin
(X111, X222, X333: Pins 47, 48, 49, 50) does not exceed 1 A. The power supply (+24 VDC) for
the digital outputs must therefore be connected to all 4 pins per DOCOMx (X111, X222, X333:
pins 47, 48, 49, 50).
Analog inputs/outputs
The inputs and outputs are supplied with power on-board, i.e. no further external power supply
units are required.
Wiring the power supply
Table 11-35 Pin assignment at X1 screw-type terminal block
Pin
Signal name
Signal type Meaning
1
P24
VI
24 V DC power supply
2
M
GND
Ground
3
PE
GND
Protective ground
Current requirement
0.7 A (at 24 VDC) for PP 72/48D 2/2A PN and digital inputs plus 3 x 4 A at X111, X222 and X333
for supplying digital outputs.
Connectable components
11.3 PP 72/48D PN 2/2A PN
NCU 1760
128
Equipment Manual, 02/2020, A5E45627861B AB
Summary of Contents for SINUMERIK ONE NCU 1760
Page 8: ...Table of contents NCU 1760 8 Equipment Manual 02 2020 A5E45627861B AB ...
Page 36: ...Description 3 5 Dual fan module NCU 1760 36 Equipment Manual 02 2020 A5E45627861B AB ...
Page 154: ...Spare parts accessories 12 2 SD card NCU 1760 154 Equipment Manual 02 2020 A5E45627861B AB ...
Page 156: ...Safety symbols NCU 1760 156 Equipment Manual 02 2020 A5E45627861B AB ...