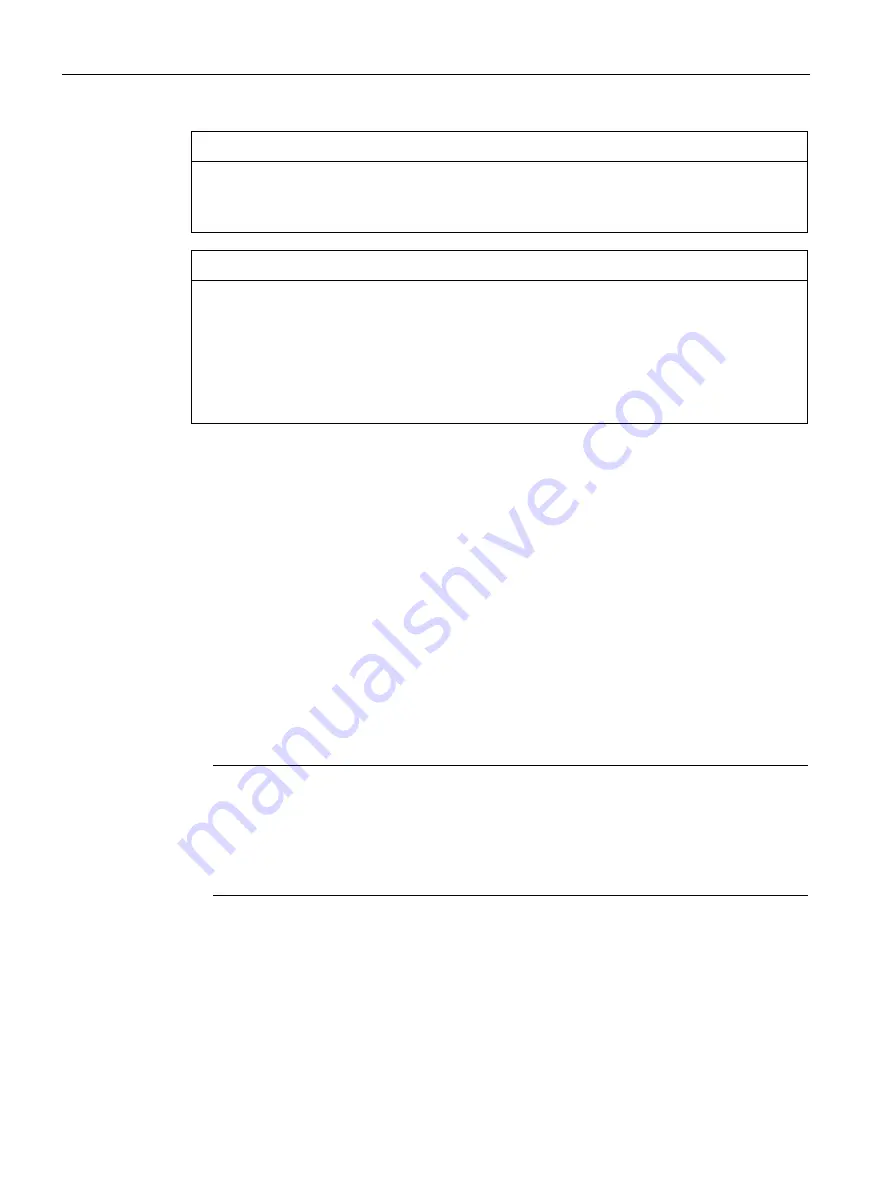
Electrical connection
6.6 Motor connection
Installation and Operating Instructions SINAMICS G180
102
Operating Instructions, 02/2019, 4BS0751-007
NOTICE
Destruction of the motor or the converter output filter
If you exceed the maximum motor cable length, this can destroy the motor or the converter
output filter. Consult the factory for longer motor cables.
NOTICE
Winding or bearing damage
If you use motors which are not designed for converter operation, premature winding or
bearing damage can occur. Consult the motor manufacturer to find out whether the motor is
suitable for converter operation. Please bear in mind that IEC 60034-17 is applicable to
motors that are designed for line operation but are operated with a converter. Smaller
values for the peak voltage apply here. Dimension the cable lengths after consultation with
the manufacturer.
6.6.6
Connecting motor cable
Connect the motor to terminals U2, V2, W2 of terminal strip -X1 of the inverter. Refer to the
technical data for the correct tightening torques for the power cable connection.
6.6.7
Connecting the PTC thermistor of the motor to the inverter
●
Connect the PTC thermistor of non-explosion-protected motors without peripheral board 2
/ 4 to terminals 27, 28 - 58 of control cable terminal block -X2.
●
If peripheral board 2 / 4 is installed, connect the PTC thermistor to terminals 90 to 94 of
control cable terminal block -X3. For additional information, refer to the description of the
accessories.
Note
Interference signals in PTC thermistor cables
If you lay sensor cables next to power cables, interference signals can be transmitted in
the sensor cables. Lay sensor cables separated from the motor power cables. Use
shielded cables in the case of stronger inductive or capacitive input couplings. Observe
the minimum cross section of the PTC thermistor cable in the technical data (Page 203).