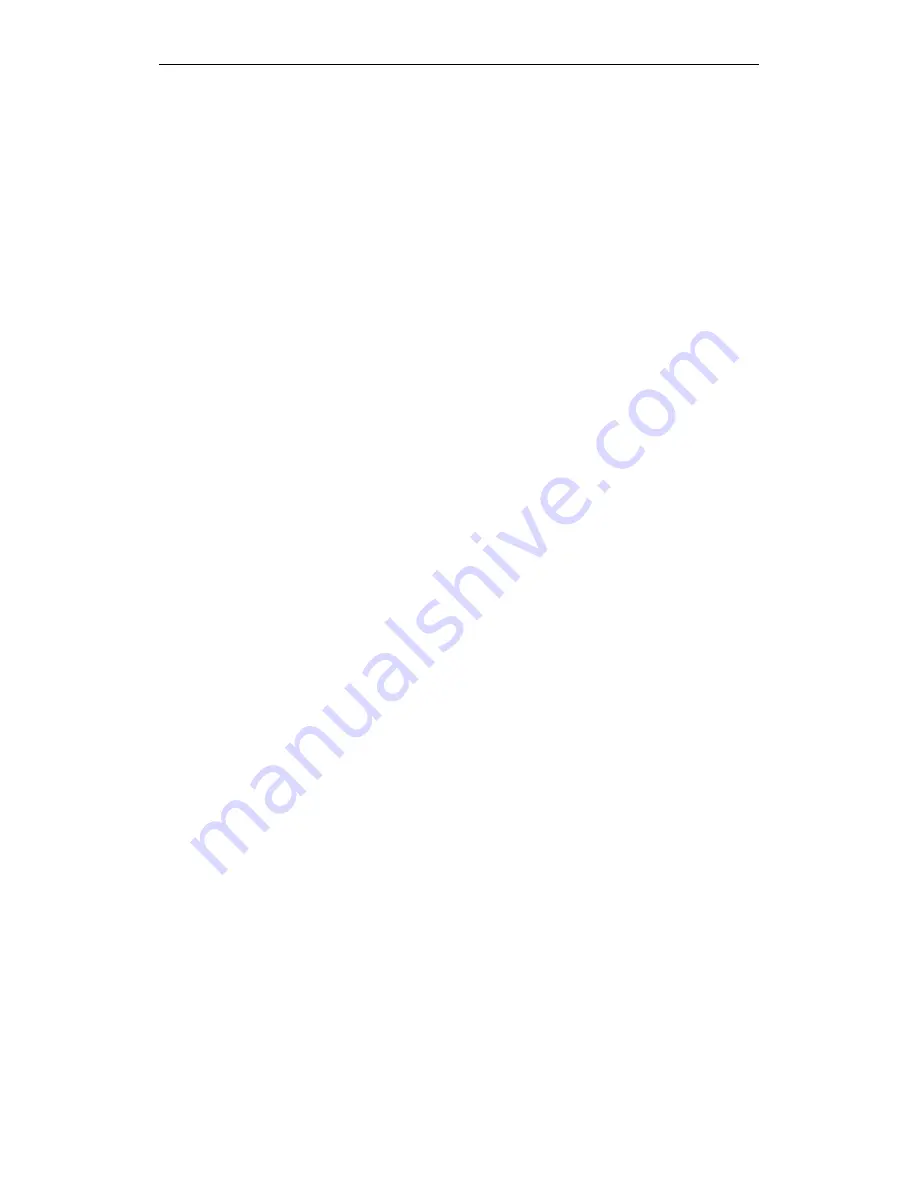
Control elements
© Siemens AG 2003 All Rights Reserved
4-32
SIMOTION Safety Unit (AP) - Edition 06.2003
4.4 Electro-sensitive protective equipment (ESPE)
Definition
These primarily include safety light curtains or light barriers that monitor access to
the hazardous areas of the press. These light curtains are intrinsically safe, i.e. in
the event of a malfunction they go into a safe state and they have certified their
suitability for presses by means of type examinations (confirmed by test
certificates).
Operating instructions
The light curtain provides two "light path unobstructed“ channels.
•
In some light curtains with semiconductor outputs, the short circuit test for
both channels is already integrated. In this case, the short circuit monitor of
the control unit should be switched off!
•
When using light curtains with relay outputs, the short circuit monitor of the
control unit must be active!
It is the task of the press safety control unit to correctly interpret the output signal of
the light curtain and to generate from it the subsequent operation and control of the
press safety valve. Light curtains can be operated in:
•
safety mode, as a substitute for a permanently-closed safety gate (see the
Safety Components chapter)
•
control mode. In this mode, the operator can reach into the protective zone
when the press is at a standstill in the TDC position in order to remove parts or
add material. After the operator leaves the protected area, the press
automatically resumes operation. Reaching into the machine while the ram is
descending causes the press to come to an immediate standstill. In the control
mode, there is both a
single-stroke mode and a two-stroke mode
. Which
mode is selected depends on whether a separate step is required when
material is fed to the machine during which the operator leaves the protective
zone.
The following light curtains have been tested with the control unit:
- Type 3RG78..., by Siemens in safety or clock mode (clock mode as of July 03)
- TypeC4000 advanced, by Sick in safety or clock mode
Others upon request