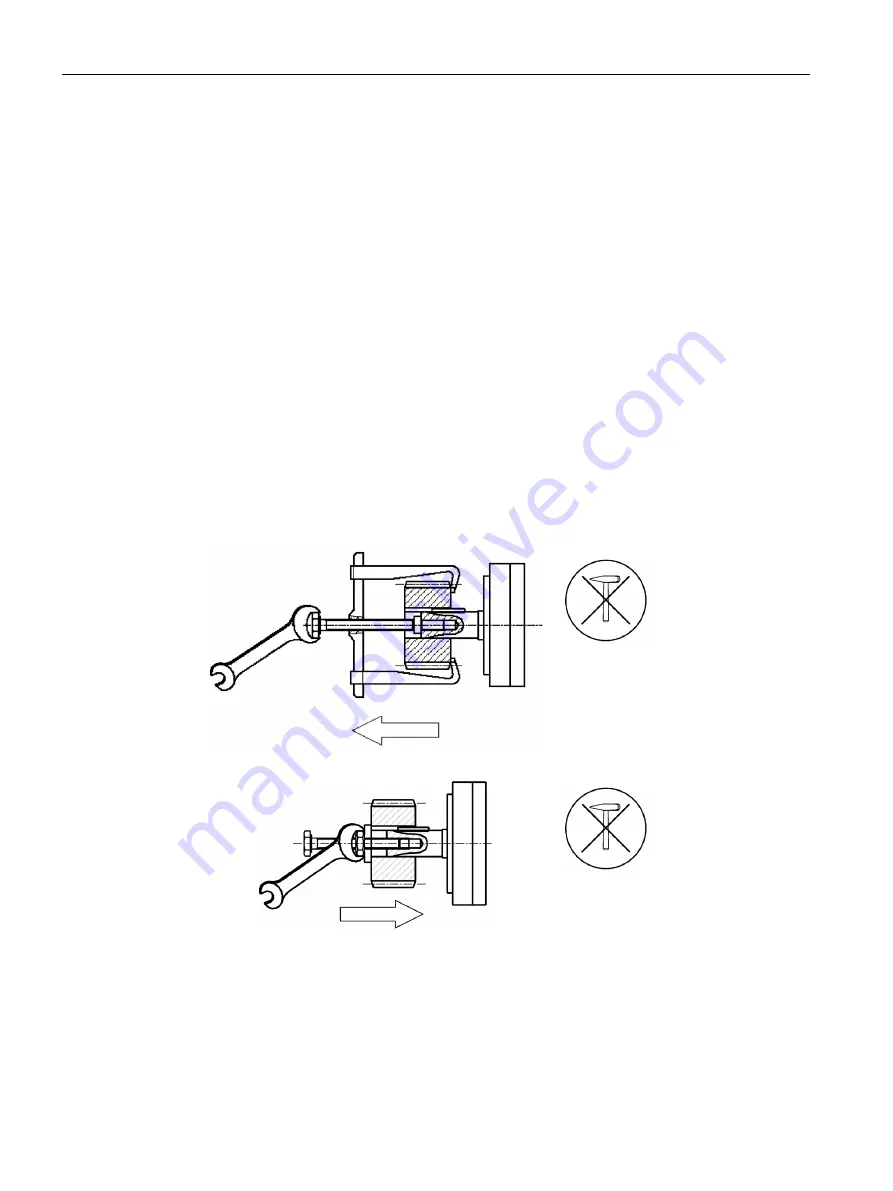
Assembly
5.5 Installing the machine
1LE5, 1PC4 shaft height 315/355
58
Operating Instructions, 10/2020, A5E41454666A
Pulling on drive output elements
•
Requirements:
–
The coupling and/or the drive output element must be appropriately dimensioned for
the operating case at hand.
–
Observe the coupling manufacturer's instructions.
–
Make sure that the balancing type of the drive output element correctly matches the
type of balance of the rotor.
–
Use only ready drilled and balanced drive output elements. Check the hole diameters
and the balancing status before pulling them on. Thoroughly clean the shaft extension.
•
Pulling on:
–
Heat up the drive output elements to expand them before pulling them on. Select the
temperature difference for the heating process to suit the coupling diameter, fit and
material. Observe the coupling manufacturer's instructions.
–
Drive output elements may only be pulled on or pulled off with the correct equipment.
The drive output element must be pulled on in one continuous operation via the front
thread holes in the shaft or pushed on by hand.
–
Do not use a hammer, as this will damage the bearings.
Withdrawing drive output elements
Mounting drive output elements
Only transfer radial or axial forces specified in the catalog to the motor bearings via the shaft
extension.
You can obtain the permissible values for axial and radial forces by contacting the Service